ALL >> General >> View Article
Printed Circuit Board Assembly process (pcba)
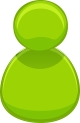
printed circuit board assembly process (PCBA)
Electronic products such as mobile phones, AIDS, TVS, Even cars, and so on use a core printed circuit board. So many small parts how to assemble into a complete printed circuit board? This article will introduce the entire process of printed circuit board assembly.
PCBA process flow
Printed circuit board assembly process refers to the specific operating steps and technical requirements of PCB assembly, and its process includes PCB design and fabrication, material procurement, SMT patch, testing, and three-proof paint.
Step one: PCB design and fabrication
PCB design is PCB engineers depend on the specific functional requirements design the PCB, including PCB schematic and circuit diagram design and drawing. Check the design and make sure it is correct. And then arrange for the PCB factory to do the PCB prototype and PCB fabrication.
Step two: BOM table design and material purchase
The BOM table, or bill of materials, is a detailed technical document that engineers design and select the corresponding electronic components according ...
... to the function of the product and PCB drawings and define the product structure in data file manufacturing.The procurement of materials includes the procurement of electronic components and wires.
Step three: The SMT patch
The SMT patch is a significant part of the PCB assembly process, which connects the components to the PCB substrate by welding. The welding forms include wave crest solder, re-flow soldering, and manual welding. Besides the choice of manual welding with rework, wave soldering, and re-flow welding are available. PCB must be cleaned sweep after welding. And they will be dried and sent for quality testing.
A. Apply solder paste:
Put the circuit board on a stainless steel plate and apply the solder paste correctly and evenly to the solder pad on the surface of the circuit board.
Solder paste is a gray substance composed of many tiny metal balls consisting of 96.5% tin, 3% silver, and 0.5% copper. Solder paste is a mixture of solder and flux. Flux is a chemical that helps the solder melt and stick to the surface.
B.SPI detection:
After the solder paste printing is complete, it is necessary to use the SPI machine to check it. To check is to confirm the printing quality of the solder paste and whether there exists tin leakage, tin less, and other problems.
C.Patch:
After the solder paste is applied, the robot will place the surface mount components on the prepared PCB, after the BGA, IC, resistor, capacitor, and other components through the machine equipment will welded to the PCB surface through the machine equipment.
D.Re-flow welding:
After the application of solder paste and surface mount components, due to the solder paste having no solidifying effect, the component is not very strong after mounting, so the process of re-flow welding is required to cause the component to be solid on the board. In popular terms, it is put into a furnace, melting and cooling through high temperature. Components are solidly on the board.
Step four: Insert the through-hole element
Depending on the type of circuit board, the welding chosen method is different. Besides the common SMD, there are electroplated through-hole components or PHT components. The electroplated through holes are the holes through the circuit board. The signal is from one side of the board to the other through these holes. The solder paste printing through the holes is not attached spot and needs to use a specific welding method.
A.Manual welding:
Using manual perforation welding.
B.Crest welding:
The component is put on the circuit board, the liquid flux applies to the component lead, and then the circuit board is preheated to a specific temperature, through the conveyor belt reaches the wave welding machine, which melts the solder paste wave to form the welding spot. The components are firmly attached to the circuit board.
Step five: PCB cleaning
After the printed circuit board is assembled, it must go through the cleaning step to clean up the welding traces or contaminants left over during the welding process. Deionized water or improvement solution is used to clean the circuit board, and deionized water is used to shoot the circuit board at high temperatures and pressure. After cleaning, use a power jet to dry the circuit board and send it for a final product test.
Step six: PCBA test
Printed circuit board assembly testing ensures that the product is in the correct working condition, and some automated tests are used to detect the PCB, further ensuring PCB quality and efficiency. The test includes functional testing, burn-in testing, and reliability testing. The test is the last and most crucial step in the PCBA process and determines the success of the previous process steps. There are several detection methods:
A.Visual inspection:
For a few circuit boards, we can choose a visual inspection. By the designer to check and ensure the quality of the PCB.
B.Automatic optical inspection:
This method is suitable for large-scale PCBA inspection. The automatic optical inspection machine uses high-performance cameras to observe and detect where there is a problem with welding from various angles.
C.X-ray:
Use infrared to check the printed circuit board assembly inner layer for potential problems.
D.In-Circuit Test System(ICT):
It is mainly through the test probe to contact the test point of the PCB layout to detect the PCBA line open circuit, short circuit, and welding of all parts. The fault will pass the printer or screen display accurately notice the user.
E.QC manual inspection:
According to the norm IPC-610 inspection standard, the finished board check to ensure 99.98% good product delivery.
F.QA Shipment inspection:
Strict inspection before delivery of products, and scan code checks to prevent unqualified products from being shipped.
Step seven: Apply three anti-paint
The three anti-paint are applied on the PCBA surface, which has the effect of moisture-proof and anti-corrosion, to extend the life of the product. After the above steps are both completed, you can pack and ship.
In general, the assembly of printed circuit boards is a complex and cumbersome process. It needs to be step by step, each link is crucial. In actual operation, depending on the requirements of customers, PCB assembly manufacturer need according to the design requirements of customers to plan a series of assembly processes to ensure the quality and function of products.
Keyword: PCBA、printed circuit board assembly、PCB、PCB assembly manufacturer、PCBA process 、PCB design、PCB prototype、PCB fabrication、PCB assembly、PCB layout 、PCB factory
Add Comment
General Articles
1. Affects Of Caffeine On Dental: Benefits & DemeritsAuthor: Rosalina Wolf
2. How To Write Ignou Project On Time
Author: Ignou project
3. Future Of Nicotine Pouches In India: Key Manufacturers And Market Potential
Author: Zvol
4. Sports Betting App Development: A Complete Guide For Startups
Author: Gamingcrab
5. Accutane Vs. Other Acne Treatments: Which Is Better?
Author: Lisa Miracle
6. Unlock The Perfect Blend Of Luxury, Location, And Investment At A G Landmark Studio, Wakad, Pune
Author: Armaan
7. Revolutionizing Legal Marketing: 360 Lawfirm Marketer Introduces Next-level Digital Services In Ny
Author: Mitesh Patel
8. Andaman With Kids: Safe, Fun, And Exciting Family Packages
Author: Probin Das
9. Buying Flats In Sahu City Pearl: Your Ultimate Guide
Author: Star Estate
10. Circuits En Inde Et Culture Locale : Plongez Au Cœur Des Traditions Indiennes
Author: UTTAM
11. Purchase Best Quality Round Bar In India
Author: Shashwat Stainless Inc.
12. Mud Crab Farming
Author: astroaquaculture
13. Need A Third-party Pharma Manufacturer With Global Reach?
Author: Medmom Pharma
14. How Often Should You Clean Your Mini Split For Optimal Performance?
Author: Tim Harrison
15. Critical Safety Technology For Vehicles
Author: Sandra McCall