ALL >> Business >> View Article
Plastic Extrusion: Know About Its Industrial Applications And Working
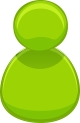
Plastic extrusion is a large-scale manufacturing method that produces continuous, homogeneous cross-sections. This method involves melting thermoplastic materials and pressurizing them to drive the melt through a die.
Pressure is generated when a revolving screw interacts with the barrel walls. As the melted plastic passes through the die, it takes on the shape of the die and exits as an extrudate. Later chilling processes, such as cooling rollers or water baths, harden the extrudate into its final shape.
Plastic extrusion is a flexible process that produces tubes, pipes, sheets, profiles, films, and bespoke forms. The extruder machinery used in this operation is part of a larger system designed to mass-produce plastic components. Other important components of a plastic extruder are the feed pipe/adapter, feed throat, hopper, breaker plate, die, barrel, and cooling system. These components combine to melt, form, and solidify plastic polymers.
Which Industries Use Plastic Extrusion?
Many businesses make use of extruded plastic tubing. It's especially important ...
... in the medical, automotive, construction, electronics, food, and beverage industries. In medicine, both flexible and stiff tubes are manufactured in this manner. They end up in devices such as catheters, IV lines, and medical pouches. Extruded plastic is valuable in the automobile industry because it is durable and cost-effective, as such parts are intended to withstand a broad variety of weather conditions.
In the food and beverage industry, this material is used in beverage dispensing systems and food-grade packaging.
How does plastic extrusion work?
Plastic extrusion from plastic extrusion manufacturer is a multistage process that includes melting, extrusion, cooling, and processing steps. It starts with feeding raw material, usually polymer resin pellets, into a hopper. Fillers and coloring agents are added to the resin pellets to form a homogeneous mixture suitable for melting and extrusion. Similar to plastic injection molding, a hopper of plastic pellet material feeds a barrel with a spinning screw that pushes the material forward. As the material travels between the screw and the barrel walls, shearing forces and friction cause it to heat up and melt. Heaters on the barrel provide extra heat, which aids the melting process. Drag forces created by the screw drive the melted polymer through a filter and breaker plate to eliminate impurities and provide a uniform distribution of polymer across the die assembly at the barrel's end. Extruded plastic may be utilized in a variety of applications, including basic pipes and precision medical implants.
Melted plastic is molded and sculpted to fit the contour of the exit die aperture. At this point, the extrusion is still hot and pliable. The material travels through a cooling bath filled with water, which evenly cools and solidifies the extrusion, assisting in its ultimate shape. Air or metal-contact cooling methods are also occasionally utilized. To reduce flaws and retain the form, extrusions with hollow parts may require a vacuum sizing stage before cooling. Pull rollers apply a consistent pulling pressure, which smoothes the plastic and moves it along the line. The plastic extrusion is quality-controlled using onboard laser measuring devices, and excellent parts are subsequently spooled or trimmed to final product specifications. The product is now ready for final quality tests, storage, and packing.
Add Comment
Business Articles
1. Elevate Your Style With Custom Tuxedos From La Rukico – The Best Bespoke Tailor In NycAuthor: La Rukico Custom Tailor
2. Short Term Loans Uk Direct Lender: The Initial And Final Step In Getting Quick Funding
Author: Helen Clark
3. Factors To Consider When Choosing Nano Ceramic Roofing Tiles In Andhra Pradesh
Author: Danish Fabrication
4. Short Term Loans Uk: Apply Online For A Loan From A Direct Lender
Author: Sarah Ferguson
5. How Appkodes Built Their Own Way To Revolutionize The Airbnb Clone
Author: John Daniel M
6. The Real Deal: What Actually Works For Seo Managers In 2025
Author: Rene
7. Unlocking The Advantages Of E-waste Management Awareness Training
Author: Emma
8. Trimbakeshwar Temple Kaal Sarp Puja | Shree Trimbakeshwar
Author: Rakesh Guruji
9. Mandatory Procedures In Iso 15378 Documents: A Comprehensive Overview
Author: John
10. Concrete Sealers With Corrosion Inhibitors: Enhancing Durability And Longevity
Author: Ivar
11. Top-rated Restroom Cubicles – Installations & Maintenance
Author: super creations
12. Your Trusted Real Estate Agents In Bihar - Bhushan Realtors Pvt. Ltd
Author: Bhushan Realtors
13. Iron Casting Company In India: Aqeel Industries
Author: Aqeel Industries
14. How Many Days Do You Need To Explore Panama? Panama Mission India
Author: Panama Mission india
15. Mg Hector Price In Chennai: A Complete Guide
Author: balaji