ALL >> Business >> View Article
What Are Mold Material Used In Thermoforming Process?
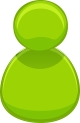
Vacuum forming often referred to as thermoforming, is a plastic processing technology, the main principle is to spread the plastic hard sheet heating and softening, using vacuum adsorption on the surface of the mold, after cooling molding, widely used in plastic packaging, lighting, advertising, decoration and other industries.
There are several thermoforming methods used in actual production, and the most basic ones are six: differential pressure forming, overmolding, plunger-assisted molding, suction molding, countermolding, and twin sheet forming.
What is Thermoforming Mold?
Thermoforming mold, refers to the mold used in the production of thermoforming, the lowest cost is plaster mold, followed by electroplated copper mold, the most expensive is aluminum mold. The molds are drilled with small holes for vacuum adsorption of thermoformed hard film to form the thermoforming product.
Thermoforming mold is a plastic plate, sheet as raw material molding some of the simpler plastic products of a mold, the principle is to use the vacuum method or compressed air molding method so that the plastic sheet ...
... fixed in the concave or convex mold in the case of heating and softening of deformation and affixed to the cavity of the mold to get the required molded products, mainly used in a number of daily necessities, food, toys, packaging products production aspects. Thermoforming molds for molding pressure is low, so the mold material is mostly cast aluminum or non-metallic materials manufacturing, structure is relatively simple.
Vacuum forming mold is an indispensable part of the thermoforming process, its role is to make the thermoplastic sheet deformed into the product desired shape under a certain temperature and pressure.
Vacuum forming molds are mainly composed of two parts, the upper and lower parts of the mold, the middle of the general heating device and air flow control device.
In the vacuum forming process, the plastic materials sheet is firstly placed on the upper position of the suction molding machine, heated to a certain temperature, and then through suction or compressed air, the sheet is adsorbed on the thermoforming mold, and then through the role of heating and pressurization, so that the thermoplastic sheet is slowly deformed, plastic flow, and ultimately formed into the shape of the product.
Thermoforming Mold Classification
Thermoforming mold refers to the mold used in thermoforming production. The lowest cost is plaster mold, followed by electroplated copper mold, aluminum mold and steel mold. The mold is drilled with small holes for vacuum adsorption of the heated hard film to form a blister product.
Plaster mold
Plaster molds are mainly made of yellow foaming plaster powder. If have drawings, the plaster material will be made by milling machine and by hand according to the data and requirements of the drawings. If have the physical object, the mold is first completed with handmade clay. Contour, vacuum molding for vacuum cover, then re-form the plaster mold and modify the mold, it takes about 2-4 days, the plaster mold is easy to make, short time, conducive to modification The product is well packaged, low price, but low durability, easy to be damaged after a period of time of use. The transparency of the produced products is poor. It is mainly suitable for the first edition confirmation and the products with low transparency requirement of outer packaging.
Plastic Molds
Plastic molds are a kind of common molds for vacuum forming products, which are mainly made of plastic, resin and rubber. They have the advantages of low manufacturing cost, long service life, easy processing and manufacturing, but also have the disadvantages of low precision and strength. Plastic molds are generally suitable for making small and simple thermoforming products, such as tableware and toys.
Electrolytic Copper Mold
Electrolytic copper mold is polished and ready for use, it takes about 3-5 days, it is a metal mold, so it is more durable. The appearance and transparency of the products produced with this type of mold are better; the mold production price is lower, and it is widely used. It is usually The first choice mold in any situation; mainly suitable for products with higher requirements such as electronics, toys, stationery, cosmetics, automobile boutiques, etc.
Aluminum Molds
Aluminum mold manufacturing cost is relatively low, the manufacturing process is simple, but its strength and precision are not as good as steel mold. Cast aluminum molds are mainly suitable for small batch, not high complexity of the production of thermoforming products, such as handles, lids and so on.
Steel Molds
The manufacturing process of steel mold is relatively complex, but also its strength and precision is much higher than plastic mold. At the same time, the wear resistance of steel molds is also better, suitable for the production of large, complex, high-intensity plastic products, such as car interiors, furniture and so on.
Thermoforming Mold Materials
As a packaging process widely used in medical, food, toys, household and other fields, the material of the mold for pressure forming technology has a crucial impact on the quality and dimensional stability of packaging products.
Usually, the material of the thermoforming mold is selected according to the shape and size of the mold, the material of the product and its usage. The following are the most commonly used materials for thermoforming molds at present.
ABS: ABS material has the characteristics of strong, impact resistance, not easy to deform, etc. It is suitable for the production of small or medium-sized plastic products.
PC: PC material is high temperature resistant, high hardness and high rigid plastic , suitable for producing large or complex structure of the thermoforming mold, such as TV set-top box.
PMMA: PMMA material is easy to process into complex shapes, suitable for the production of high transparency or a variety of colors of products, such as cosmetic packaging.
TPR: TPR material has good elasticity and abrasion resistance, which is suitable for producing soft thermoforming materials, such as toys.
Plaster: Use gypsum to carve and shape in a semi-wet state, and then dry it to form a mold. The cost of the plaster mold is low and easy to modify. However, the precision of the plaster mold is not high enough, the surface is not smooth, and it is fragile and not durable. Therefore, thermoforming trays are commonly used It comes to proofing.
Copper: It belongs to the metal mold type, so it is more durable. The thermoforming tray produced with this type of mold has better appearance and transparency. Molds are relatively cheap to make and have a wide range of uses. They are the most common molds and are mainly used in industries such as cosmetics, food, toys, electronics and hardware.
Aluminum Alloy: Aluminum alloy is another commonly used material for vacuum forming molds, with light weight, corrosion resistance, good thermal conductivity, etc. It is suitable for making small and medium-sized air pressure forming molds. Aluminum alloy for making thermoforming molds can greatly reduce the production cost, and the processing difficulty is relatively low.
Resin: Resin, also known as thermoplastic, is another commonly used material for making thermoforming molds. Resin has the characteristics of short molding cycle, high strength and good stability, which is suitable for making small and complex thermoforming molds.
There are many different types of resin, such as ABS resin, PC resin, etc. Choosing the right resin has a great impact on the quality and efficiency of making thermoforming molds.
Silicone Rubber: Silicone rubber is a high temperature resistant, aging resistant and corrosion resistant material, which is suitable for making high-precision and high-demanding thermoforming molds. Silicone rubber molds can guarantee the quality and precision of products, but the difficulty and cost of making them are relatively high.
In short, the choice of suitable material for thermoforming molds can give full play to the characteristics of various materials to improve product quality and production efficiency.
How to Choose the Material of Thermoforming Mold?
The following factors need to be considered when selecting materials for thermoforming molds:
Characteristics of Products
The material and characteristics of the product will have an impact on the choice of thermoforming mold material.
For example, the production of high-density polyethylene terephthalate packaging products, you can choose to use ABS materials, the production of high-transparency cosmetic packaging, you can choose PMMA materials.
Mold Shape and Size
The shape and size of the mold also has a great impact on the choice of thermoforming mold materials. Usually, to manufacture complex shapes or larger molds, you can choose PC materials or metal materials.
Mold Life
The length of the mold life is also a factor to be considered when choosing the thermoforming mold material. If the mold needs to be used frequently, you need to choose high wear-resistant, high toughness materials, such as PC and TPR material.
Production Efficiency
Production efficiency is also a key factor in the choice of thermoforming mold materials. Usually, the mold production efficiency is high, need to use strong, easy to process, easy to maintain and other characteristics of the material.
High Corrosion Resistance
Many resins and additives have a corrosive effect on the surface of the mold. This corrosion will cause the metal on the surface of the mold to dissolve and peel off, and the surface condition will deteriorate, resulting in poor quality of the vacuum formed components.
Therefore, it is best to use corrosion-resistant materials, or perform chrome plating or cymbal nickel treatment on the mold surface.
Good Wear Resistance
The gloss and precision of the surface of the plastic product are directly related to the wear resistance of the mold surface. Especially when glass fiber, inorganic fillers and certain pigments are added to some plastics, they will work with the plastic melt in the runner and mold.
The flow in the cavity will cause great friction on the surface of the mold. If the material is not wear-resistant, it will wear out quickly, causing damage to the quality of the plastic parts.
Good Dimensional Stability
During thermoforming process, the temperature of the sheet and mold must reach above 300°C. For this purpose, it is best to use tool steel that has been properly tempered (heat-treated steel).
Otherwise, it will cause changes in the microstructure of the material, resulting in changes in mold dimensions.
Easy to Process
Some steel mold parts have complex structural shapes. In order to shorten the production cycle and improve efficiency, the mold materials are required to be easy to process into the shape and accuracy required by the drawings.
Good Polishing Performance
Thermoforming products usually require good gloss and surface condition, so the roughness of the mold surface is required to be very small. Therefore, usually the mold must undergo surface processing, such as polishing, grinding, etc. Therefore, the materials selected for mold making should not contain rough impurities and pores.
Little Affected by Heat Treatment
In order to improve the hardness and wear resistance, the mold is generally heat treated, but this treatment should make the dimensional changes very small. Therefore, it is best to use high temperature grade material.
Heavy Gauge Thermoforming Machine Model and Mold Selection
Important factors that usually determine the choice include molds, products, plastic types and output requirements. Therefore, the following information must be collected or possessed before making a choice:
Product dimensions (length, width, height).
The wall thickness of the product.
Type and quantity of products used.
After obtaining the above information, you can follow the following steps to choose a suitable thick sheet blister machine:
1. The maximum external dimension of the product determines the wellhead size of the machine. If the molding area is less than 1.5 square meters, a small thickness machine should be selected. If the molding area is between 1.5 and 3.7 square meters, a large thickness machine should be selected. If the molding area is above 3.7 square meters, a large thickness machine should be selected. , as described in the above model classification.
2. If the wall thickness of the product is between 1.5-2mm, and the stretch ratio of the product (ratio of average dimensions of height/length + width) is greater than 1, a double-layer heating model should be selected. If it is less than 1 , choose a single-layer heating model.
If the wall thickness of the product is below 1.5mm, no matter how large the stretch ratio is (of course products with a stretch ratio exceeding 1.5 are not suitable for blister molding), then a single-layer heating model can be used.
If the wall thickness of the product is above 2mm and the draw ratio is below 0.5, a single-layer heating model should be selected. If the draw ratio exceeds 0.5, a double-layer heating model should be selected.
3. If you choose according to the type and quantity of the product, if the product is relatively single and the quantity is large, and the annual output is more than 60,000-80,000, then a double-station or multi-station model should be selected, such as synchronous heating and molding blister machine, and aluminum alloy molds are suitable for blister molds.
If the product specifications are large and the single quantity is small, it is suitable to choose a single station, and the heating unit can be controlled by one, the pressing frame and the supporting plate can all be used. A model that is easy to adjust and change molds is better. Most blister molds are made of resin or bakelite.
Conclusion
The choice of thermoforming molds has a great impact on the quality of products and production efficiency and other aspects, the correct choice of materials can improve production efficiency and product quality.
Thermoforming mold selection needs to be based on specific product requirements, cost and production batch and other factors for comprehensive consideration.
In the selection of mold materials, according to the size, shape, use, production and other factors to ensure that the production efficiency and product quality.
Add Comment
Business Articles
1. Essential Photo Editing Tips To Enhance Your Website's AppealAuthor: ukclippingpath
2. 5 Ways To Revolutionize Telecom With Smart Inventory Management Software
Author: Kevin
3. Rubber Roller: Enhancing Industrial Efficiency And Performance
Author: Anar rub tech pvt.ltd.
4. Tips For Cleaning And Prepping Jars For Candle Making
Author: Namo Creations
5. Vip Desert Safari Dubai
Author: Safari kings deserts
6. Why Byst Offers The Best Mentorship Programs For Entrepreneurs
Author: Byst Youth
7. How A 5kw Solar System Can Power Your Home And Save You Money
Author: Keyur Patel
8. How Long To Get A Title Loan In Wyoming | Ez Car Title Loans
Author: Ez Car Title Loans
9. Lucintel Forecasts The Global Thermoplastic Composites Market To Reach $26 Billion By 2030
Author: Lucintel LLC
10. Essential Features To Look For In An Event Management App
Author: Event Management App
11. Technology Landscape, Trends And Opportunities In The Global Micro-led Market
Author: Lucintel LLC
12. Data Visualization Software Market Forecast: Growth In Cloud Solutions
Author: mmr
13. Lucintel Forecasts The Global Food Packaging Market To Reach $xx Billion By 2024
Author: Lucintel LLC
14. Beyond Wealth: Unlocking The Power Of Family Office Services In India
Author: Drishti Desai
15. Enteral Single Use Syringes Market Size & Share, Analysis 2031
Author: Andy