ALL >> Business >> View Article
Overview Of The Vacuum Casting Process
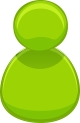
Vacuum casting, also known as resin casting or polyurethane casting, is a manufacturing process used to create prototypes and small production runs of plastic or rubber parts. It's particularly popular in industries like automotive, aerospace, and consumer electronics for its ability to produce high-quality parts with complex geometries and fine surface details.
Here's a step-by-step overview of the vacuum casting process:
Master Pattern Creation: The process begins with the creation of a master pattern, which serves as the original model for the desired part. This master pattern can be made from various materials such as wood, plastic, or metal, and it's typically produced using techniques like CNC machining or 3D printing.
Mold Making: A silicone rubber mold is then created around the master pattern. This mold captures all the intricate details and features of the master pattern. Multiple parts can be cast from a single mold, making it efficient for small-batch production.
Vacuum Chamber ...
... Preparation: The mold is placed inside a vacuum chamber, which helps to remove any trapped air and ensure that the resin fills the mold completely and evenly. The vacuum chamber is sealed tightly to create a vacuum environment.
Resin Casting: Liquid resin material, usually a two-part polyurethane or epoxy resin, is poured into the mold cavity. The vacuum is applied, causing the air bubbles within the resin to expand and rise to the surface. This process helps to eliminate voids and defects in the final part.
Curing: After the resin has been cast into the mold, it undergoes a curing process to harden and solidify. This can be achieved through various methods such as heat curing or exposure to ultraviolet (UV) light, depending on the type of resin used.
Demolding: Once the resin has fully cured, the mold is opened, and the newly formed part is removed. Any excess material or flash around the edges of the part may need to be trimmed or removed manually.
Finishing: Depending on the specific requirements, additional finishing processes such as sanding, painting, or assembly may be performed to achieve the desired final product.
Vacuum casting offers several advantages, including the ability to produce parts with precise dimensions, excellent surface finish, and mechanical properties similar to injection-molded parts. It's a cost-effective solution for prototyping and small-scale production, allowing manufacturers to iterate quickly and efficiently during the product development process.
Add Comment
Business Articles
1. Elevate Your Style With Custom Tuxedos From La Rukico – The Best Bespoke Tailor In NycAuthor: La Rukico Custom Tailor
2. Short Term Loans Uk Direct Lender: The Initial And Final Step In Getting Quick Funding
Author: Helen Clark
3. Factors To Consider When Choosing Nano Ceramic Roofing Tiles In Andhra Pradesh
Author: Danish Fabrication
4. Short Term Loans Uk: Apply Online For A Loan From A Direct Lender
Author: Sarah Ferguson
5. How Appkodes Built Their Own Way To Revolutionize The Airbnb Clone
Author: John Daniel M
6. The Real Deal: What Actually Works For Seo Managers In 2025
Author: Rene
7. Unlocking The Advantages Of E-waste Management Awareness Training
Author: Emma
8. Trimbakeshwar Temple Kaal Sarp Puja | Shree Trimbakeshwar
Author: Rakesh Guruji
9. Mandatory Procedures In Iso 15378 Documents: A Comprehensive Overview
Author: John
10. Concrete Sealers With Corrosion Inhibitors: Enhancing Durability And Longevity
Author: Ivar
11. Top-rated Restroom Cubicles – Installations & Maintenance
Author: super creations
12. Your Trusted Real Estate Agents In Bihar - Bhushan Realtors Pvt. Ltd
Author: Bhushan Realtors
13. Iron Casting Company In India: Aqeel Industries
Author: Aqeel Industries
14. How Many Days Do You Need To Explore Panama? Panama Mission India
Author: Panama Mission india
15. Mg Hector Price In Chennai: A Complete Guide
Author: balaji