ALL >> Business >> View Article
Are You Searching A Best Vacuum Forming
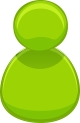
Vacuum forming is a manufacturing process used to create hollow plastic parts by heating a thermoplastic sheet and then forming it over a mold using vacuum pressure. It's a versatile and relatively low-cost method for producing large or small quantities of parts with simple to moderately complex shapes.
Here's an overview of the vacuum forming process:
Sheet Heating: The process begins with a flat thermoplastic sheet, typically made of materials like ABS, polystyrene, PVC, or acrylic. This sheet is clamped in place and heated until it becomes pliable but not fully melted. Heating can be done using various methods, such as radiant heaters, infrared heaters, or convection ovens.
Forming: Once the sheet reaches the optimal temperature, it is quickly transferred to the forming station, where it is draped over a mold. The mold can be made from various materials, including wood, aluminum, or composite materials, and it defines the shape of the final part. The edges of the sheet are clamped in place to create a seal.
Vacuum Pressure: A vacuum is then applied underneath ...
... the mold, pulling the heated plastic tightly against the surface of the mold. This vacuum pressure helps to form the plastic sheet into the desired shape, conforming to the contours of the mold.
Cooling: After the plastic has been formed over the mold, it is allowed to cool and harden. Cooling can be accelerated using fans or water cooling systems. Once cooled, the plastic retains the shape of the mold.
Trimming and Finishing: Once the formed part has cooled sufficiently, it is removed from the mold and trimmed to remove any excess material or flash. Additional finishing processes, such as drilling, cutting, or machining, may be performed as needed to achieve the desired final shape and surface finish.
Vacuum forming is commonly used to produce a wide range of parts and products, including packaging trays, automotive interior components, consumer electronics housings, point-of-sale displays, and medical equipment enclosures. It offers advantages such as fast production speeds, low tooling costs, and the ability to create parts with consistent wall thicknesses and detailed surface textures.
Add Comment
Business Articles
1. Lucintel Forecasts The Global Polyvinylidene Difluoride (pvdf) Market To Reach $2 Bllion By 2030Author: Lucintel LLC
2. Electronics Thermal Management Solutions Market Size & Share, Analysis 2031
Author: Andy
3. Choosing The Right Custom Injection Mould Manufacturer For Your Needs
Author: MOULDING-INJECTION
4. Discover The Timeless Beauty Of Handmade Ceramic Products
Author: Matthew Edwards
5. The Power Of Advanced C Frame Mechanical Power Presses
Author: Mankoo Presses
6. Lucintel Forecasts The Global Short Fiber Thermoplastic Market To Reach $24 Billion By 2030
Author: Lucintel LLC
7. Lucintel Forecasts The Polyurethane Resin In The Global Composites Market To Reach $188 Million By 2030
Author: Lucintel LLC
8. Custom Sticker Printing In Dubai: The Answer To Individual Branding
Author: Digital glob
9. Lucintel Forecasts The Global Greaseproof Paper Sheet Market To Reach $3 Billion By 2030
Author: Lucintel LLC
10. Speech Development Experts For Kids In Hyderabad
Author: pavitra
11. Lucintel Forecasts The Global Polypropylene (pp) Compound Market To Reach $15 Billion By 2030
Author: Lucintel LLC
12. Forecasting The Expansion Of The Ginger Powder Market
Author: mmr
13. Why Work With A Leadership Consulting Firm: A Complete Guide
Author: cluboneair
14. Unlocking The Billionaires Mindset: 10 Transformative Habits To Achieve Limitless Success
Author: Ourbusinessladder
15. Embrace Solar Energy With Elite Electrical Kent: Your Trusted Partner In Bromley And Beyond
Author: nicola