ALL >> Business >> View Article
What’s The Difference between Thermoforming And Injection Molding
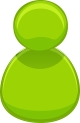
Often, customers in their own hands of the product in the thermoforming process or injection molding process can not tell the difference, or their own design in the end should be used in the injection molding process or thermoforming process?
In the market, the most common plastic parts in the market are thermoforming products or injection molded product. and thermoforming and injection molding are popular manufacturing processes. In fact, for many products, both can vacuum form and also can be plastic injection molding,. That specifically. In which way, do different users have different choices, exactly how is good? Cost, efficiency, and quality are often the most important considerations.
Of course, they are not opposites but complementary. In this blog, we will introduce the Difference Between Thermoforming and Injection Molding in detail.
Different Manufacturing Process
Thermoforming processing
The principle of thermoforming technology is also called the vacuum forming molding process. It is a thermoforming processing method, the use of the thermoplastic sheet, the manufacture of open plastic ...
... shell products the method, is the plastic sheet is cut to a certain size after heating and softening, with the help of the heated plastic sheet on both sides of the difference in air pressure and mechanical pressure, so that the deformation of a specific mold profile, after cooling and shaping, and cutting and trimming to complete the thermoforming products process!
Injection molding process
Injection molding is a process in which thermoplastic plastic pellets are heated and molten liquid polymers are, and then the molten plastic is injected into the injection molds through the injection molding machine with high pressure, after a certain cooling time, the plastic is solidified and shaped in the injection molding tooling.
Different materials used
The most significant difference between thermoforming and injection molding is the different materials used. The commonly used materials are PP, PE, ABS, PVC, PET, PS, and other thermoplastic pellets and sheets, while injection molding uses more thermosetting plastics, such as PP, PA, PC, ABS, POM, PE, and other granular raw materials.
Thermoforming uses plates and sheets, so the raw materials will be more expensive compared to injection molding granular materials.
Different design structure of products
Injection molded products are more accurate and can produce complex shapes and structures, while thermoforming products generally produce simpler shapes.
The shape obtained by injection molding is often the final product, and no further processing is required before it is installed or used as a final product. Many details, such as projections, ribs, and threads, can be molded in a single step in injection molding.
Thermoforming products can be produced in simple shapes, with smooth surfaces, are easy to process and assemble, and require post-processing to make holes and remove excess material after the product has been molded. The products mainly include packaging boxes, handicrafts, cards, and so on. Thermoforming products are also widely used in electronics, home appliances, medical and toys.
Different product usage
Due to the different materials and processes, there are some differences between the products made of thermoforming and injection molding. Thermoforming products usually have strong flexibility, impact resistance, and wear resistance, especially suitable for the production of curved and arched products, such as blister packaging boxes, three-dimensional billboards, and so on.
While injection molding products usually have the characteristics of high precision, high strength, good dimensional stability, etc., they are suitable for the production of electronic product shells, automobile parts, industrial equipment, and so on.
Different equipment and tools
Injection molding requires injection molding machines, molds, and other equipment and tools; injection molding machines are mainly divided into vertical injection molding machines, horizontal injection molding machines, two-colour injection molding machines, single-colour injection molding machines, high-speed injection molding machines and so on.
Thermoforming products require equipment and tools such as thermoforming machines and thermal processing devices. According to the different types of pressurization of thermoforming, the mainstream thermoforming equipment is mainly divided into the following three categories:
(1) Vacuum negative pressure forming machine, mainly through the negative pressure vacuum method, so that the plastic sheet is affixed to the mold;
(2) Positive pressure vacuum machine, through the air compressor on the front of the plastic sheet with atmospheric pressure, so that the softened plastic sheet is affixed to the mold;
(3) Positive and negative pressure vacuum molding machines, which form a strong pressure difference between the two sides of the plastic sheet by means of pressurization and vacuum, so that the softened plastic sheet is molded. These three kinds of equipment, each has its own advantages and disadvantages, need to be based on the characteristics of the product to choose the machine.
The parameters of temperature, pressure, and flow rate of injection molding equipment in the process of product processing can be precisely adjusted through the control system, which ensures the precision of product making. At the same time, injection molding equipment consumes less raw materials when processing high-precision products, which also reduces product costs.
In contrast, blister molding equipment is limited in the means of controlling parameters such as temperature, pressure, and flow rate, which is a limitation to the production of products requiring high precision.
Different production efficiency
Injection molding is a kind of high volume production runs plastic processing method. The general production efficiency of injection molding equipment can reach a production capacity of hundreds to thousands of pieces per hour.
At the same time, the degree of automation of injection molding equipment is also very high, and it can quickly complete the processing of products and improve production efficiency. In contrast, the production speed of thermoforming is slower compared to injection molding, and the processing time of the products usually takes several minutes to tens of minutes.
Different costs
A. Tooling Costs
Injection mold according to the complexity of the product, different precision, and mold material at different prices. The commonly used mold materials are S50C, P20, H13, 718H, NAK80, S136, etc., due to the complexity of the product is different, and involves a lot of complexity of the mold processing process than the thermoforming mold, the cost of the relative thermoforming molds are also higher than 5 to 10 times.
The molds used for thermoforming: The molds commonly used for blistering are gypsum molds, aluminum molds, copper molds, wood molds, and steel molds.
The materials used in plastic injection molds are relatively low, and the product structure is simple, so the molds are relatively simple, the materials are cheap, and there are lower tooling costs.
Gypsum mold: the material is gypsum powder, simple to manufacture and amend, usually a single piece of mold only needs 1~3 days, because it is brittle and difficult to dissipate heat, gypsum molds are usually used for the case of having samples handmade samples, not for production.
Aluminum mold: it is made of aluminum through machining and grinding. The aluminum mold has high precision, a smooth surface and is hard and durable, but the price is very expensive, generally used under strict requirements of the product, and ordinary molds can't achieve the precision effect of the use of such molds.
Copper mold: Copper mold should be made with plaster mold first, then take the sample to copper plating, and then fill with gypsum inside.
The copper mold has a better appearance and finish, strength can also reach the usual production requirements, and it is one of the widely used thermoforming molds.
Substitute wood mold: the material is substitute wood, the material cost is higher, needs CNC processing, the manufacturing cycle is short, usually a few hours, easy to sand and punch. The material is also brittle, suitable for sampling in the scene with 3D drawing files, not for production.
Steel mold: generally S45C, S50C, and P20 materials; generally thermoforming, use this type of steel mould.
B. Product costs
The cost of thermoforming vs injection molding is not the same. As the production process of injection molding is relatively simple, the cost advantage of injection molding is obvious when producing large quantities and high-cost products; while thermoforming molding is suitable for smaller production quantities, short production cycles, complex shape products, etc., which is relatively more economical.
The initial cost of injection molds is higher, but the cost per piece is lower when producing large quantities, and the start-up cost of thermoforming is lower, but the cost rises with the increase in production.
In injection molding equipment in the production process, recycling raw material loss will be much less than the vacuum forming molding equipment, especially in the production of larger batches of products, injection molding equipment in the cost savings have obvious advantages.
In addition, injection molding equipment has a higher degree of automation, which does not require much manual operation and also reduces production costs, it's more cost effective for high volume production.
Overall, injection molding is more efficient than blister molding is proven, although the investment in injection molding equipment is larger, in the long run, its production efficiency and production cost advantage will bring more profits and competitive advantage for enterprises.
Conclusion
To sum up, although both thermoforming and injection molding belong to the plastic molding process, there are obvious differences in their materials, production processes, uses, production precision, and product characteristics.
When choosing the molding process, you need to select the most suitable process according to the requirements and characteristics of the specific product. In the actual production and use need to choose the right type of product according to the specific needs.
Add Comment
Business Articles
1. Lucintel Forecasts The Global Polyvinylidene Difluoride (pvdf) Market To Reach $2 Bllion By 2030Author: Lucintel LLC
2. Electronics Thermal Management Solutions Market Size & Share, Analysis 2031
Author: Andy
3. Choosing The Right Custom Injection Mould Manufacturer For Your Needs
Author: MOULDING-INJECTION
4. Discover The Timeless Beauty Of Handmade Ceramic Products
Author: Matthew Edwards
5. The Power Of Advanced C Frame Mechanical Power Presses
Author: Mankoo Presses
6. Lucintel Forecasts The Global Short Fiber Thermoplastic Market To Reach $24 Billion By 2030
Author: Lucintel LLC
7. Lucintel Forecasts The Polyurethane Resin In The Global Composites Market To Reach $188 Million By 2030
Author: Lucintel LLC
8. Custom Sticker Printing In Dubai: The Answer To Individual Branding
Author: Digital glob
9. Lucintel Forecasts The Global Greaseproof Paper Sheet Market To Reach $3 Billion By 2030
Author: Lucintel LLC
10. Speech Development Experts For Kids In Hyderabad
Author: pavitra
11. Lucintel Forecasts The Global Polypropylene (pp) Compound Market To Reach $15 Billion By 2030
Author: Lucintel LLC
12. Forecasting The Expansion Of The Ginger Powder Market
Author: mmr
13. Why Work With A Leadership Consulting Firm: A Complete Guide
Author: cluboneair
14. Unlocking The Billionaires Mindset: 10 Transformative Habits To Achieve Limitless Success
Author: Ourbusinessladder
15. Embrace Solar Energy With Elite Electrical Kent: Your Trusted Partner In Bromley And Beyond
Author: nicola