ALL >> General >> View Article
Exploring The Mesh Belt Furnace: Applications, Advantages, And Innovations
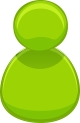
In the realm of industrial thermal processing, the mesh belt furnace stands out as a versatile and efficient tool for heat treatment, sintering, brazing, and drying applications across various industries. With its unique conveyor belt design, precise temperature control, and adaptability to continuous production, the mesh belt furnace has become a cornerstone in manufacturing processes worldwide. Let's delve into the workings of the mesh belt furnace, its applications, advantages, and recent innovations driving its evolution.
Understanding the Mesh Belt Furnace:
The mesh belt furnace, also known as a conveyor belt furnace, is a type of continuous heat-treating equipment designed for thermal processing of bulk materials or components. It consists of a conveyor belt made of stainless steel mesh or wire mesh, which transports the workpieces through the heating chamber. The furnace typically comprises multiple heating zones with individual temperature controls, allowing for precise thermal profiles tailored to the specific process requirements.
Applications Across Industries:
The versatility of mesh belt ...
... furnaces makes them indispensable across a wide range of industries, where thermal processing plays a crucial role in manufacturing operations. Some key applications include:
Heat Treatment: Mesh belt furnaces are extensively used for heat treating metal components to improve their mechanical properties, hardness, and durability. Processes such as annealing, quenching, tempering, and carburizing can be carried out efficiently and uniformly in these furnaces.
Sintering: In the powder metallurgy industry, mesh belt furnaces facilitate the sintering of metal powders to form dense, consolidated parts with precise dimensional control. This process is vital for manufacturing components used in automotive, aerospace, and tooling applications.
Brazing and Soldering: Mesh belt furnaces provide a controlled atmosphere for brazing and soldering operations, ensuring strong and reliable joints between metal parts. These furnaces are widely employed in the production of heat exchangers, electrical components, and automotive assemblies.
Drying and Curing: Industries such as ceramics, textiles, and electronics utilize mesh belt furnaces for drying, curing, and bonding of coatings, adhesives, and polymers. The continuous conveyor system enables efficient processing of large volumes of materials with consistent quality.
Advantages of Mesh Belt Furnaces:
The adoption of mesh belt furnaces offers several advantages over batch processing and other types of heat-treating equipment:
Continuous Processing: Mesh belt furnaces enable continuous production, resulting in higher throughput and reduced cycle times compared to batch furnaces. This continuous operation ensures consistent quality and uniformity of heat-treated products.
Precise Temperature Control: The multi-zone heating system allows for precise control over temperature profiles, ensuring that workpieces are subjected to the optimal thermal conditions for the desired process outcome. This level of control enhances product quality and repeatability.
Energy Efficiency: Mesh belt furnaces are designed to minimize heat loss and optimize energy efficiency. Advanced insulation materials and heating elements contribute to reduced energy consumption, lowering operating costs and environmental impact.
Versatility and Flexibility: These furnaces can accommodate a wide range of materials, shapes, and sizes, making them highly versatile for diverse manufacturing applications. The adjustable conveyor speed and temperature settings offer flexibility to tailor the process parameters according to specific requirements.
Innovations Driving Evolution:
Recent innovations in mesh belt furnace technology focus on enhancing performance, reliability, and automation capabilities. Advancements such as advanced control systems with real-time monitoring and predictive maintenance capabilities, improved conveyor designs for enhanced material handling, and novel heating elements for faster ramp-up times and energy savings are driving the evolution of these furnaces.
Conclusion:
The mesh belt furnace has emerged as a cornerstone in industrial thermal processing, offering unparalleled efficiency, precision, and versatility across a myriad of applications. As industries continue to demand higher throughput, quality, and sustainability in manufacturing operations, the evolution of mesh belt furnace technology will play a pivotal role in meeting these requirements. With ongoing innovations and advancements, mesh belt furnaces are poised to remain indispensable assets in the arsenal of modern manufacturing facilities, driving progress and innovation in the years to come.
Add Comment
General Articles
1. Affects Of Caffeine On Dental: Benefits & DemeritsAuthor: Rosalina Wolf
2. How To Write Ignou Project On Time
Author: Ignou project
3. Future Of Nicotine Pouches In India: Key Manufacturers And Market Potential
Author: Zvol
4. Sports Betting App Development: A Complete Guide For Startups
Author: Gamingcrab
5. Accutane Vs. Other Acne Treatments: Which Is Better?
Author: Lisa Miracle
6. Unlock The Perfect Blend Of Luxury, Location, And Investment At A G Landmark Studio, Wakad, Pune
Author: Armaan
7. Revolutionizing Legal Marketing: 360 Lawfirm Marketer Introduces Next-level Digital Services In Ny
Author: Mitesh Patel
8. Andaman With Kids: Safe, Fun, And Exciting Family Packages
Author: Probin Das
9. Buying Flats In Sahu City Pearl: Your Ultimate Guide
Author: Star Estate
10. Circuits En Inde Et Culture Locale : Plongez Au Cœur Des Traditions Indiennes
Author: UTTAM
11. Purchase Best Quality Round Bar In India
Author: Shashwat Stainless Inc.
12. Mud Crab Farming
Author: astroaquaculture
13. Need A Third-party Pharma Manufacturer With Global Reach?
Author: Medmom Pharma
14. How Often Should You Clean Your Mini Split For Optimal Performance?
Author: Tim Harrison
15. Critical Safety Technology For Vehicles
Author: Sandra McCall