ALL >> General >> View Article
Unlocking The Power Of High-temperature Furnaces: Innovations And Applications
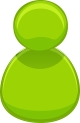
High-temperature furnaces stand as marvels of engineering, enabling the manipulation of materials at extreme temperatures for various industrial and scientific purposes. These furnaces, with their ability to reach temperatures exceeding 1000°C and even surpassing 3000°C in some cases, play a pivotal role in numerous fields, ranging from materials science and metallurgy to research and development. Let's delve into the intricacies of high-temperature furnaces, exploring their innovations, applications, and significance in modern industries.
Understanding High-Temperature Furnaces:
High-temperature furnaces are specialized heating devices designed to subject materials to intense heat, enabling processes such as sintering, annealing, melting, and heat treatment. They utilize advanced heating elements, insulation materials, and control systems to achieve and maintain precise temperature conditions. These furnaces can operate under various atmospheres, including vacuum, inert gas, and controlled atmospheres, allowing for tailored thermal treatments to suit specific materials and applications.
Innovations Driving ...
... Performance:
Recent advancements in materials science and furnace technology have led to significant improvements in the performance and capabilities of high-temperature furnaces. Innovations such as refractory materials with enhanced thermal stability, advanced insulation techniques to minimize heat loss, and sophisticated heating elements capable of rapid heating and precise temperature control have revolutionized the functionality of these furnaces. Additionally, the integration of automation and digital control systems has enabled greater efficiency, repeatability, and flexibility in furnace operation.
Applications Across Industries:
The versatility of high-temperature furnaces renders them indispensable across various industries, where thermal processing plays a critical role in materials synthesis, fabrication, and characterization. Some key applications include:
Metallurgy and Materials Science: High-temperature furnaces are extensively used in metallurgical processes such as alloy production, heat treatment, and powder metallurgy. They facilitate the sintering of ceramics, annealing of metals, and diffusion bonding of materials, enabling the development of advanced alloys and engineered materials with tailored properties.
Semiconductor Manufacturing: In the semiconductor industry, high-temperature furnaces are employed for processes like epitaxial growth, oxidation, and diffusion of dopants in silicon wafers. These furnaces ensure precise control over temperature profiles and gas environments, crucial for achieving desired thin-film properties and device performance.
Glass and Ceramics Production: Glass melting furnaces and ceramic kilns utilize high temperatures to melt raw materials and shape them into desired forms. These furnaces play a vital role in the production of glassware, ceramics, refractories, and specialized materials used in construction, electronics, and aerospace industries.
Research and Development: High-temperature furnaces serve as indispensable tools in research laboratories and academic institutions, supporting a wide range of studies in materials science, chemistry, and physics. They enable experiments such as crystal growth, phase transformations, and thermal analysis, providing insights into material behavior under extreme conditions.
Future Prospects and Challenges:
As industries continue to push the boundaries of materials performance and functionality, the demand for high-temperature furnaces will likely escalate. Future developments may focus on enhancing energy efficiency, reducing environmental impact, and expanding the operational range of these furnaces to accommodate novel materials and processes. Challenges such as thermal management, material compatibility, and scalability remain areas of active research and innovation.
In conclusion, high-temperature furnaces stand as indispensable tools driving innovation and progress across diverse industries. Their ability to manipulate materials at extreme temperatures unlocks a realm of possibilities for material synthesis, processing, and characterization, paving the way for advancements in technology, manufacturing, and scientific discovery. As research and development efforts continue to evolve, high-temperature furnaces will remain at the forefront of thermal processing technologies, shaping the future of materials science and engineering.
User
write article mesh belt furnace
ChatGPT
Exploring the Mesh Belt Furnace: Applications, Advantages, and Innovations
In the realm of industrial thermal processing, the mesh belt furnace stands out as a versatile and efficient tool for heat treatment, sintering, brazing, and drying applications across various industries. With its unique conveyor belt design, precise temperature control, and adaptability to continuous production, the mesh belt furnace has become a cornerstone in manufacturing processes worldwide. Let's delve into the workings of the mesh belt furnace, its applications, advantages, and recent innovations driving its evolution.
Understanding the Mesh Belt Furnace:
The mesh belt furnace, also known as a conveyor belt furnace, is a type of continuous heat-treating equipment designed for thermal processing of bulk materials or components. It consists of a conveyor belt made of stainless steel mesh or wire mesh, which transports the workpieces through the heating chamber. The furnace typically comprises multiple heating zones with individual temperature controls, allowing for precise thermal profiles tailored to the specific process requirements.
Applications Across Industries:
The versatility of mesh belt furnaces makes them indispensable across a wide range of industries, where thermal processing plays a crucial role in manufacturing operations. Some key applications include:
Heat Treatment: Mesh belt furnaces are extensively used for heat treating metal components to improve their mechanical properties, hardness, and durability. Processes such as annealing, quenching, tempering, and carburizing can be carried out efficiently and uniformly in these furnaces.
Sintering: In the powder metallurgy industry, mesh belt furnaces facilitate the sintering of metal powders to form dense, consolidated parts with precise dimensional control. This process is vital for manufacturing components used in automotive, aerospace, and tooling applications.
Brazing and Soldering: Mesh belt furnaces provide a controlled atmosphere for brazing and soldering operations, ensuring strong and reliable joints between metal parts. These furnaces are widely employed in the production of heat exchangers, electrical components, and automotive assemblies.
Drying and Curing: Industries such as ceramics, textiles, and electronics utilize mesh belt furnaces for drying, curing, and bonding of coatings, adhesives, and polymers. The continuous conveyor system enables efficient processing of large volumes of materials with consistent quality.
Advantages of Mesh Belt Furnaces:
The adoption of mesh belt furnaces offers several advantages over batch processing and other types of heat-treating equipment:
Continuous Processing: Mesh belt furnaces enable continuous production, resulting in higher throughput and reduced cycle times compared to batch furnaces. This continuous operation ensures consistent quality and uniformity of heat-treated products.
Precise Temperature Control: The multi-zone heating system allows for precise control over temperature profiles, ensuring that workpieces are subjected to the optimal thermal conditions for the desired process outcome. This level of control enhances product quality and repeatability.
Energy Efficiency: Mesh belt furnaces are designed to minimize heat loss and optimize energy efficiency. Advanced insulation materials and heating elements contribute to reduced energy consumption, lowering operating costs and environmental impact.
Versatility and Flexibility: These furnaces can accommodate a wide range of materials, shapes, and sizes, making them highly versatile for diverse manufacturing applications. The adjustable conveyor speed and temperature settings offer flexibility to tailor the process parameters according to specific requirements.
Innovations Driving Evolution:
Recent innovations in mesh belt furnace technology focus on enhancing performance, reliability, and automation capabilities. Advancements such as advanced control systems with real-time monitoring and predictive maintenance capabilities, improved conveyor designs for enhanced material handling, and novel heating elements for faster ramp-up times and energy savings are driving the evolution of these furnaces.
Conclusion:
The mesh belt furnace has emerged as a cornerstone in industrial thermal processing, offering unparalleled efficiency, precision, and versatility across a myriad of applications. As industries continue to demand higher throughput, quality, and sustainability in manufacturing operations, the evolution of mesh belt furnace technology will play a pivotal role in meeting these requirements. With ongoing innovations and advancements, mesh belt furnaces are poised to remain indispensable assets in the arsenal of modern manufacturing facilities, driving progress and innovation in the years to come.
Add Comment
General Articles
1. Affects Of Caffeine On Dental: Benefits & DemeritsAuthor: Rosalina Wolf
2. How To Write Ignou Project On Time
Author: Ignou project
3. Future Of Nicotine Pouches In India: Key Manufacturers And Market Potential
Author: Zvol
4. Sports Betting App Development: A Complete Guide For Startups
Author: Gamingcrab
5. Accutane Vs. Other Acne Treatments: Which Is Better?
Author: Lisa Miracle
6. Unlock The Perfect Blend Of Luxury, Location, And Investment At A G Landmark Studio, Wakad, Pune
Author: Armaan
7. Revolutionizing Legal Marketing: 360 Lawfirm Marketer Introduces Next-level Digital Services In Ny
Author: Mitesh Patel
8. Andaman With Kids: Safe, Fun, And Exciting Family Packages
Author: Probin Das
9. Buying Flats In Sahu City Pearl: Your Ultimate Guide
Author: Star Estate
10. Circuits En Inde Et Culture Locale : Plongez Au Cœur Des Traditions Indiennes
Author: UTTAM
11. Purchase Best Quality Round Bar In India
Author: Shashwat Stainless Inc.
12. Mud Crab Farming
Author: astroaquaculture
13. Need A Third-party Pharma Manufacturer With Global Reach?
Author: Medmom Pharma
14. How Often Should You Clean Your Mini Split For Optimal Performance?
Author: Tim Harrison
15. Critical Safety Technology For Vehicles
Author: Sandra McCall