ALL >> Business >> View Article
Single Screw Plastic Extruder Demystified For Manufacturers
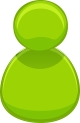
When it comes to plastic manufacturing, understanding the intricacies of the single screw plastic extruder is crucial for optimizing production processes and enhancing efficiency. This comprehensive guide aims to demystify the single screw plastic extruder, shedding light on its key components, benefits, selection criteria, troubleshooting methods, operational tips, technological advancements, maintenance practices, and real-world applications.
Understanding Single Screw Plastic Extruders: A Comprehensive Guide
Single screw plastic extruders are versatile machines used in the plastic industry to melt, mix, and shape raw plastic materials into desired forms. The extrusion process involves feeding plastic resins or compounds into the extruder barrel where they are conveyed, melted, and forced through a die to create a continuous profile. The single screw design features a rotating screw within a heated barrel, ensuring uniform melting and mixing of the plastic material.
The Extruder Barrel
The extruder barrel serves ...
... as the main housing for the screw and is typically heated to facilitate the melting process. It is crucial for maintaining the desired temperature profile to ensure consistent material flow and product quality.
The Screw
The heart of single screw used extruders for sale is the screw itself, which rotates within the barrel to convey, compress, melt, and homogenize the plastic material. The design of the screw, including its flight depth, pitch, and compression ratio, plays a significant role in determining the extrusion process parameters and final product characteristics.
The Drive System
The drive system of the extruder controls the speed and torque of the screw, influencing the material's residence time in the barrel and the overall extrusion rate. Proper tuning of the drive system is essential for achieving the desired output and product quality.
Key Components of a Single Screw Plastic Extruder Explained
To delve deeper into the functioning of used extruder equipment, it is essential to understand the key components that contribute to its operation and performance. These components work in harmony to ensure efficient plastic processing and product consistency.
Heater Bands
Heater bands are used to heat the extruder barrel to the required temperature for melting the plastic material. Proper temperature control is essential to prevent overheating or underheating, which can affect the material's flow properties and result in product defects.
Cooling System
In addition to heating, single screw plastic extruders require a cooling system to maintain optimal operating temperatures and prevent overheating of critical components. Effective cooling ensures prolonged machine life and consistent production output.
Die and Calibration Tooling
The die and calibration tooling are essential components that shape the extruded plastic material into the desired profile or dimensions. Precision in die design and calibration is crucial for achieving accurate product specifications and meeting quality standards.
Benefits of Using Single Screw Plastic Extruders in Manufacturing
The utilization of single screw plastic extruders offers manufacturers a plethora of benefits that contribute to enhanced productivity, cost efficiency, and product quality. Understanding these advantages can help manufacturers make informed decisions regarding their production processes.
Cost-Effectiveness
Single screw plastic extruders are known for their simplicity in design and operation, making them cost-effective solutions for a wide range of plastic extrusion applications. Their efficiency in melting and shaping plastic materials translates to lower energy consumption and reduced production costs.
Versatility
These extruders are highly versatile and can process a variety of plastic materials, including thermoplastics, thermosets, and elastomers. Their adaptability to different formulations and product requirements makes them suitable for diverse manufacturing applications.
Consistent Output
The continuous operation of single screw plastic extruders ensures a consistent output of extruded products with uniform dimensions and properties. This reliability is essential for meeting quality standards and customer expectations in manufacturing.
How to Choose the Right Single Screw Plastic Extruder for Your Needs
Selecting the appropriate single screw plastic extruder for a specific manufacturing application requires careful consideration of various factors to ensure optimal performance and productivity. Manufacturers should assess their production requirements, material characteristics, output specifications, and budget constraints before making a decision.
Production Capacity
The extruder's output capacity, expressed in kilograms per hour (kg/hr), should align with the production demand of the manufacturing facility. Choosing an extruder with the right throughput capacity ensures efficient production without overloading the machine or causing bottlenecks.
Material Compatibility
Different plastic materials have varying melting points, viscosities, and processing requirements. It is essential to select an extruder that is compatible with the specific materials being processed to achieve optimal melting, mixing, and extrusion performance.
Energy Efficiency
Opting for a single screw plastic extruder with energy-efficient features, such as advanced heating and cooling systems, can lead to significant cost savings over the machine's operational lifespan. Energy-efficient extruders help reduce electricity consumption and minimize environmental impact.
Troubleshooting Common Issues with Single Screw Plastic Extruders
Despite their reliability and efficiency, single screw plastic extruders may encounter operational issues that can disrupt production and affect product quality. Manufacturers should be aware of common problems and their troubleshooting methods to minimize downtime and maintain consistent performance.
Material Feeding Problems
Issues with material feeding, such as bridging, surging, or uneven flow, can lead to inconsistent output and product defects. Adjusting the feed rate, screw speed, or barrel temperature can help address feeding issues and ensure smooth material flow.
Overheating
Excessive heat buildup in the extruder barrel or screw can cause material degradation, discoloration, or burning, resulting in poor product quality. Monitoring and controlling the temperature settings, cooling system, and screw speed can prevent overheating and maintain optimal processing conditions.
Screw Wear and Damage
Continuous operation and exposure to abrasive materials can lead to wear and damage to the extruder screw, affecting its performance and extrusion quality. Regular inspection, maintenance, and timely replacement of worn components can prevent costly downtime and production losses.
Maximizing Efficiency: Tips for Operating Your Single Screw Plastic Extruder
To optimize the performance and efficiency of a single screw plastic extruder, manufacturers can implement various operational strategies and best practices that enhance productivity, quality, and machine longevity. These tips can help streamline production processes and maximize the extruder's potential.
Optimize Screw Design
Customizing the screw design to suit specific material properties and processing requirements can improve mixing efficiency, melt homogeneity, and overall extrusion performance. Working with experienced screw designers or suppliers can help optimize the extruder's screw geometry for enhanced productivity.
Implement Process Control Systems
Integrating advanced process control systems, such as automated temperature monitoring, screw speed adjustment, and material flow control, can enhance operational efficiency and product consistency. Real-time monitoring and feedback mechanisms enable operators to fine-tune process parameters for optimal results.
Conduct Regular Maintenance
Scheduled maintenance routines, including cleaning, lubrication, inspection, and component replacement, are essential for prolonging the extruder's lifespan and preventing unexpected breakdowns. Following manufacturer recommendations and maintenance schedules can help sustain machine performance and reliability.
Innovations in Single Screw Plastic Extruder Technology
The field of single screw plastic extrusion continues to witness advancements in technology and design that aim to improve processing efficiency, product quality, and sustainability. Manufacturers can benefit from staying informed about the latest innovations and integrating cutting-edge solutions into their production processes.
High-Performance Screw Materials
The development of high-performance screw materials, such as bimetallic alloys, ceramic coatings, and nitrided steels, enhances wear resistance, corrosion protection, and extrusion performance. These advanced materials prolong screw life and maintain consistent product quality over extended production runs.
Smart Extrusion Controls
Smart extrusion control systems incorporate sensors, actuators, and data analytics to monitor and optimize extrusion parameters in real time. These intelligent systems enable predictive maintenance, process optimization, and quality assurance, enhancing overall production efficiency and product consistency.
Energy-Efficient Heating Systems
Innovative heating technologies, such as induction heating, infrared heating, and radiant heating, offer energy-efficient alternatives to traditional heating methods in single screw plastic extruders. These systems reduce heat loss, improve temperature control, and lower operational costs while minimizing environmental impact.
Maintenance Practices to Prolong the Lifespan of Your Machine
Proper maintenance practices are essential for prolonging the lifespan of a single screw plastic extruder and ensuring consistent performance throughout its operational life. By adhering to preventive maintenance routines and addressing potential issues promptly, manufacturers can maximize their machine's longevity and productivity.
Regular Cleaning and Lubrication
Cleaning the extruder components, including the barrel, screw, and die, and applying lubricants to moving parts prevent material buildup, corrosion, and wear. Regular cleaning and lubrication routines maintain machine hygiene and reduce the risk of contamination or malfunction.
Inspection and Component Replacement
Scheduled inspections of critical components, such as the screw, heater bands, and drive system, help identify wear, damage, or alignment issues early on. Timely replacement of worn or damaged parts prevents breakdowns and ensures smooth operation of the extruder.
Calibration and Alignment Checks
Periodic calibration of the die and alignment checks of the screw and barrel are essential for maintaining product quality and dimensional accuracy. Misalignment or wear in these components can lead to extrusion defects and variations in product specifications.
Case Studies: Real-World Applications of Single Screw Plastic Extruders
Real-world applications of single screw plastic extruders span a wide range of industries and products, showcasing the machine's versatility, efficiency, and reliability in various manufacturing processes. Examining these case studies provides insights into the diverse applications and benefits of single screw extrusion technology.
Case Study 1: PVC Pipe Manufacturing
In the construction industry, single screw plastic extruders are commonly used for manufacturing PVC pipes of different sizes and specifications. The extruders efficiently process PVC compounds, ensuring consistent pipe dimensions, smooth surfaces, and high strength for structural applications.
Case Study 2: Sheet Extrusion for Packaging
In the packaging sector, single screw plastic extruders play a vital role in producing plastic sheets used for packaging materials, containers, and films. The extruders enable precise control of sheet thickness, surface finish, and material properties, meeting the stringent requirements of the packaging industry.
Case Study 3: Profile Extrusion for Building Materials
Single screw plastic extruders are instrumental in producing plastic profiles for building materials, such as window frames, door seals, and trim components. The extruders deliver accurate profile shapes, consistent dimensions, and excellent surface finish, meeting the architectural and structural demands of the construction sector.
In conclusion, single screw plastic extruders serve as indispensable tools in the plastic manufacturing industry, offering manufacturers a reliable and efficient means of processing plastic materials into a diverse range of products. By understanding the key components, benefits, selection criteria, troubleshooting methods, operational tips, technological advancements, maintenance practices, and real-world applications of single screw extrusion technology, manufacturers can optimize their production processes, enhance product quality, and stay ahead in a competitive market landscape.
Add Comment
Business Articles
1. Lucintel Forecasts The Glass Fiber In The Global Marine Market To Grow With A Cagr Of 3.7% From 2024 To 2030Author: Lucintel LLC
2. Lucintel Forecasts The Glass Fiber In The Global E&e Market To Grow With A Cagr Of 3.9% From 2024 To 2030
Author: Lucintel LLC
3. Lucintel Forecasts The Global Frp Pole In Telecommunication Market To Grow With A Cagr Of 6.5% From 2024 To 2030
Author: Lucintel LLC
4. Lucintel Forecasts The Global Frp Pole In Power Transmission & Distribution Market To Grow With A Cagr Of 6% From 2024 To 2030
Author: Lucintel LLC
5. Lucintel Forecasts The Global Frp Pipe In Oil And Gas Market To Grow With A Cagr Of 5.1% From 2024 To 2030
Author: Lucintel LLC
6. Lucintel Forecasts The Global Frp Pipe In Chemical Market To Grow With A Cagr Of 3.6% From 2024 To 2030
Author: Lucintel LLC
7. Adopt A Modern Telecom Commission Management System To Fix Revenue Leakages
Author: Kevin
8. Quality Steel Pipes And Tubes With Commitment And Trusted Service
Author: CONTENT EDITOR FOR SAMPHIRE IT SOLUTIONS PVT LTD
9. Lucintel Forecasts The Global Foam Core For The Construction Market To Grow With A Cagr Of 3.7% From 2024 To 2030
Author: Lucintel LLC
10. How Important Is Mutual Fund?
Author: Sagar Shah
11. What Do You Need To Know About Customize Your Own Clothes
Author: Guangzhou Beianji Clothing
12. Detailed Tips To Choose Quality Cabinets And Joinery Melbourne
Author: William Harvey
13. Lucintel Forecasts The Global Foam Core For The Transportation Market To Grow With A Cagr Of 5.4% From 2024 To 2030
Author: Lucintel LLC
14. Silicone Sealing Foam Cord: The Valuable Option For You
Author: Dongguan Senma New Materials Technology Co., Ltd
15. How Investment Banking Companies And Credit Solutions Elevate Wealth Management
Author: Drishti Desai