ALL >> General >> View Article
The Crucial Components Of Forged Fittings: Balancing Strength, Durability, And Cost-effectiveness
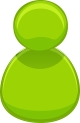
Forged fittings play a pivotal role in various industries, providing essential connections in pipelines and systems. The manufacturing process of these fittings involves shaping metal through localized compressive forces, resulting in components with superior strength and durability. Western Steel Agency is the best Forged Fittings Manufacturers in India.
In this article, we will delve into the key factors influencing forged fittings, examining the tradeoffs, challenges, and the critical role of considering environmental impact in decision-making.
Factors Influencing Forged Fittings:
Material Selection:
The choice of material is a fundamental factor affecting the performance of forged fittings. Common materials include carbon steel, stainless steel, and alloy steel. Carbon steel offers robustness and affordability, while stainless steel provides corrosion resistance. Alloy steel combines elements for enhanced strength and durability.
Tradeoff: ...
... While carbon steel may be more cost-effective, it may lack the corrosion resistance of stainless steel, leading to a shorter lifespan in corrosive environments.
Pressure and Temperature Ratings:
Forged fittings must withstand varying levels of pressure and temperature based on the application. Understanding the working conditions is crucial for selecting fittings with appropriate pressure and temperature ratings.
Tradeoff: Fittings designed for higher pressure and temperature ratings often come with increased manufacturing costs, necessitating a balance between performance and budget constraints.
Threaded vs. Socket Weld Fittings:
Two common types of forged fittings are threaded and socket weld. Threaded fittings are easy to install and dismantle, providing flexibility, while socket weld fittings offer better structural integrity. The choice between them depends on the application requirements and installation preferences.
Tradeoff: While threaded fittings offer ease of installation, they may not provide the same level of leak resistance as socket weld fittings.
Size and Dimensions:
The size and dimensions of forged fittings must align with the overall system requirements. Oversized or undersized fittings can compromise the system's efficiency and integrity.
Tradeoff: Larger fittings may offer increased flow capacity but could lead to higher costs and potential challenges in installation.
Tradeoffs and Challenges in Balancing Factors:
Cost vs. Performance:
Achieving a balance between cost and performance is a perpetual challenge in the selection of forged fittings. While cost-effective materials may be tempting, compromising on quality could lead to frequent replacements and increased maintenance costs.
Installation and Maintenance:
The ease of installation and maintenance is a crucial consideration. Threaded fittings are often preferred for their simplicity, but socket weld fittings offer a more robust solution. The choice depends on the specific needs of the application and the available resources for installation and maintenance.
Corrosion Resistance vs. Material Cost:
The tradeoff between corrosion resistance and material cost is significant. In corrosive environments, investing in stainless steel or alloy steel fittings may be essential to ensure a longer lifespan and reduce the frequency of replacements.
Considering Environmental Impact:
In today's environmentally conscious landscape, businesses and industries are increasingly aware of the ecological footprint associated with their operations. The production, use, and disposal of forged fittings can contribute to environmental impact.
Sustainable Material Choices:
Opting for materials with higher recyclability and lower environmental impact during production is a step towards sustainability. Manufacturers are exploring eco-friendly alloys and production processes to minimize their carbon footprint.
Longevity and Life Cycle Analysis:
Evaluating the lifecycle of forged fittings, including production, usage, and disposal, is crucial. Fittings with longer lifespans may contribute to reduced waste and resource consumption over time.
Energy-Efficient Manufacturing:
Manufacturers are increasingly adopting energy-efficient processes in the production of forged fittings, reducing greenhouse gas emissions and energy consumption.
Best Forged Fittings Manufacturers in India - WSAIndia
Western Steel Agency is a leading Forged Fittings Suppliers in India.We produce these ASME SA 790 Stainless Steel Forged Fittings with extra benefits and functionality to satisfy industrial demands.
Beside Forged Fittings Suppliers, We provide forged fittings worldwide, we are
Forged Plug Fittings Manufacturers in India
Forged Bushing Fittings Manufacturers in India
Forged Caps Fittings Manufacturers in India
Forged Elbow Fittings Manufacturers in India
Forged Tee Fittings Manufacturers in India
Our dynamic products are made with precision and premium raw materials. The purpose of ANSI B16.11 Forged Pipe Fittings is to enable on-site welding of pipe connections and path adjustments. Being a top manufacturer of forged fittings, we produce goods that meet high international standards and are known for their durability and functionality.
Conclusion:
Forged fittings are indispensable components in numerous industries, connecting pipelines and systems with strength and durability. The decision-making process involves a delicate balance between factors such as material selection, pressure and temperature ratings, and the choice between threaded and socket weld fittings. Tradeoffs and challenges are inherent in these decisions, requiring careful consideration to meet both performance and budgetary requirements.
Moreover, the environmental impact of forged fittings should not be overlooked. Sustainable material choices, life cycle analysis, and energy-efficient manufacturing practices contribute to minimising the ecological footprint associated with these essential components. As industries continue to evolve, the careful consideration of these factors ensures that forged fittings not only meet functional requirements but also align with broader sustainability goals.
Add Comment
General Articles
1. Categorization Of Plant Life CycleAuthor: Anthea Johnson
2. Commercial Spaces Need Style Too! Transforming Cafés & Resorts With Custom Pergolas
Author: Noor Mariam
3. Level Up Your Hana Adventure: Why An Audio Tour Is Your Best Road Trip Companion
Author: Katie Law
4. Best Erp Software Solution Company In Noida For Schools And Colleges
Author: CONTENT EDITOR FOR SAMPHIRE IT SOLUTIONS PVT LTD
5. Hinduism: Environmental Friendliness And Protecting Nature
Author: Chaitanya Kumari
6. From Ai To App Store: How Generative Tech Is Reshaping Ios Experiences
Author: Sara Wilson
7. Faston Service In Noida — Reliable, Affordable & Quick Home Ac Repair Services
Author: faston services
8. What Are The Uses And Benefits Of A Vegetable And Fruit Dryer?
Author: DYNAMIC DRYERS INTERNATIONAL
9. Primary Care Without Insurance In Raleigh
Author: satyamprimarycare
10. All Four Paws Offers Champion English Cream Golden Retriever Puppies In Indiana
Author: Geroge
11. Box Truck Wraps: The Ultimate Moving Billboard For Your Brand
Author: Saifee Signs
12. Generative Ai And Data Science Course In Hyderabad
Author: Hari
13. Mca Guidelines For Company Name
Author: Startupporta Business Services
14. Seo Services In Chennai: Boost Your Online Visibility With Proven Strategies
Author: istudio technologies
15. Best Internet Marketing Service In India
Author: Matrix Web Studio