ALL >> Business >> View Article
The Ultimate Industrial Sandblaster Handbook For Beginners
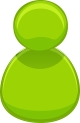
Industrial sandblasting, also known as industrial sandblasting, industrial sandblaster, or industrial blaster, is a powerful and versatile process used in various industries for cleaning, smoothing, or roughening surfaces. Whether you are new to industrial sandblasting or looking to expand your knowledge, this comprehensive handbook will guide you through the essential aspects of industrial sandblasting, from choosing the right equipment to troubleshooting common issues.
Choosing the Right Industrial Sandblaster for Your Needs
When it comes to industrial sandblasting, selecting the right equipment is crucial for achieving optimal results. There are several types of industrial sand blasters available, each designed to meet specific application requirements.
Understanding Pressure and Siphon Feed Systems
One of the primary considerations when choosing an industrial sandblaster is the feed system. Pressure feed systems are ideal for heavy-duty industrial applications, as they deliver ...
... a consistent flow of abrasive material at high pressures, making them suitable for removing tough coatings and corrosion. On the other hand, siphon feed systems are more commonly used for light to medium-duty tasks and are simpler in design, making them easier to maintain.
Evaluating Abrasive Capacity and Nozzle Size
Another important factor to consider is the abrasive capacity and nozzle size of the industrial blaster. Larger abrasive capacities are suitable for extended use without frequent refills, while the nozzle size determines the pattern and velocity of the abrasive stream, impacting the efficiency and precision of the sandblasting process.
Considering Portable vs. Stationary Units
Additionally, you should determine whether a portable or stationary industrial sandblaster is better suited for your needs. Portable units offer flexibility and convenience for projects that require mobility, while stationary units are designed for continuous, high-volume operations.
Consideration
Pressure Feed System
Siphon Feed System
Application
Heavy-duty industrial tasks
Light to medium-duty tasks
Maintenance
Requires more maintenance
Simpler and easier to maintain
Abrasive Consumption
Higher abrasive consumption
Lower abrasive consumption
Safety Precautions and Best Practices for Operating an Industrial Sandblaster
Safety should always be the top priority when operating an industrial sandblaster. The high-pressure abrasive materials used in sandblasting can pose serious hazards if proper precautions are not taken.
Personal Protective Equipment (PPE)
Before initiating any sandblasting activities, it is imperative to wear appropriate personal protective equipment, including a respirator to prevent inhalation of abrasive particles, protective clothing, gloves, and eye protection to shield against abrasive ricochets.
Proper Ventilation and Containment
Adequate ventilation and containment measures are essential to minimize the dispersion of abrasive dust and maintain a safe working environment. Utilizing enclosed sandblasting cabinets or setting up temporary containment structures can help control the spread of abrasive materials.
Equipment Inspection and Maintenance
Regular inspection and maintenance of the industrial sandblaster are crucial for ensuring safe operation. This includes checking hoses, fittings, and nozzles for wear and tear, as well as verifying the integrity of safety interlocks and pressure relief systems.
Tips for Maintaining and Cleaning Your Industrial Sandblaster
Proper maintenance and cleaning are fundamental to prolonging the lifespan and optimizing the performance of an industrial sandblaster.
Regular Cleaning of Abrasive Residue
After each sandblasting session, it is essential to thoroughly clean the equipment to remove abrasive residue and prevent clogging. This involves flushing out the abrasive material from the system and inspecting the interior components for any accumulation.
Lubrication of Moving Parts
Applying lubrication to the moving parts of the industrial sandblaster, such as valves, triggers, and air regulators, helps prevent corrosion and ensures smooth operation.
Storage in a Dry Environment
When the industrial sandblaster is not in use, it should be stored in a dry environment to prevent moisture-related damage and corrosion. Additionally, covering the equipment with a protective tarp or sheet can provide an extra layer of defense against environmental elements.
Exploring Different Abrasives for Industrial Sandblasting Applications
Abrasives play a pivotal role in industrial sandblasting, and selecting the appropriate abrasive material is essential for achieving the desired surface preparation results.
Common Abrasives Used in Sandblasting
Several types of abrasive materials are commonly used in industrial sandblasting, including aluminum oxide, silicon carbide, glass beads, and steel grit. Each abrasive material possesses unique characteristics, such as hardness, particle shape, and recyclability, making them suitable for specific applications.
Matching Abrasives to Surface Materials
The choice of abrasive material should be tailored to the composition and condition of the surface being treated. For instance, softer abrasives like glass beads are suitable for delicate surfaces, while harder abrasives like aluminum oxide are effective for removing tough coatings and rust from metal substrates.
Recycling and Disposal Considerations
In line with environmental sustainability practices, some abrasive materials can be recycled and reused, reducing waste and minimizing environmental impact. Proper disposal methods should be adhered to for non-recyclable abrasive materials to ensure compliance with environmental regulations.
Troubleshooting Common Issues with Industrial Sandblasters
Despite proper maintenance and operation, industrial sandblasters may encounter various issues that can impede performance.
Abrasive Clogging and Flow Interruptions
Abrasive clogging within the blasting system or interruptions in abrasive flow can hinder the sandblasting process. This issue can often be attributed to inadequate filtration or moisture accumulation in the abrasive material, necessitating thorough system purging and maintenance.
Uneven Abrasive Distribution
Uneven distribution of abrasive material can result in inconsistent surface preparation. Adjusting the nozzle size and abrasive flow rate, as well as ensuring proper air pressure, can help achieve uniform abrasive distribution.
Air Compressor Irregularities
The air compressor is integral to the operation of an industrial sandblaster, and irregularities in air pressure or volume can impact the efficiency of the sandblasting process. Regular monitoring and maintenance of the air compressor are essential to prevent such issues.
In conclusion, mastering the art of industrial sandblasting involves a comprehensive understanding of equipment selection, safety protocols, maintenance practices, abrasive materials, and effective troubleshooting. By following the guidelines outlined in this handbook, beginners and professionals alike can enhance their proficiency in industrial sandblasting and achieve superior results in surface preparation and restoration projects.
Add Comment
Business Articles
1. Lucintel Forecasts The Glass Fiber In The Global Marine Market To Grow With A Cagr Of 3.7% From 2024 To 2030Author: Lucintel LLC
2. Lucintel Forecasts The Glass Fiber In The Global E&e Market To Grow With A Cagr Of 3.9% From 2024 To 2030
Author: Lucintel LLC
3. Lucintel Forecasts The Global Frp Pole In Telecommunication Market To Grow With A Cagr Of 6.5% From 2024 To 2030
Author: Lucintel LLC
4. Lucintel Forecasts The Global Frp Pole In Power Transmission & Distribution Market To Grow With A Cagr Of 6% From 2024 To 2030
Author: Lucintel LLC
5. Lucintel Forecasts The Global Frp Pipe In Oil And Gas Market To Grow With A Cagr Of 5.1% From 2024 To 2030
Author: Lucintel LLC
6. Lucintel Forecasts The Global Frp Pipe In Chemical Market To Grow With A Cagr Of 3.6% From 2024 To 2030
Author: Lucintel LLC
7. Adopt A Modern Telecom Commission Management System To Fix Revenue Leakages
Author: Kevin
8. Quality Steel Pipes And Tubes With Commitment And Trusted Service
Author: CONTENT EDITOR FOR SAMPHIRE IT SOLUTIONS PVT LTD
9. Lucintel Forecasts The Global Foam Core For The Construction Market To Grow With A Cagr Of 3.7% From 2024 To 2030
Author: Lucintel LLC
10. How Important Is Mutual Fund?
Author: Sagar Shah
11. What Do You Need To Know About Customize Your Own Clothes
Author: Guangzhou Beianji Clothing
12. Detailed Tips To Choose Quality Cabinets And Joinery Melbourne
Author: William Harvey
13. Lucintel Forecasts The Global Foam Core For The Transportation Market To Grow With A Cagr Of 5.4% From 2024 To 2030
Author: Lucintel LLC
14. Silicone Sealing Foam Cord: The Valuable Option For You
Author: Dongguan Senma New Materials Technology Co., Ltd
15. How Investment Banking Companies And Credit Solutions Elevate Wealth Management
Author: Drishti Desai