ALL >> Business >> View Article
6 Preventions For Keeping Processes Running Smoothly With Instrument Calibration
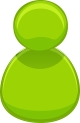
Hundreds of very accurate electronic devices are used in manufacturing plants to ensure that processes function smoothly. These devices must be inspected, repaired, and calibrated regularly to continue performing without interruption and to specifications. Electrical sensors, timing sensors, flow sensors, temperature sensors, and pressure sensors all require calibration. When this occurs, the instruments are often transported to a calibration lab for calibration, or a calibration engineer is brought within the plant to conduct the calibration tests.
Here are six preventive steps that automation and calibration engineers should be assisted with for successful instrument calibration and keeping your facility operational.
Preventive Calibration Maintenance: Examine your mechanical resources in the same manner you would examine your electrical assets during a preventive maintenance route. They can give results that make the component appear uncalibrated even if it only has to be cleaned or tuned up. Begin by inspecting the fans and filters; depending on the equipment, they should be cleaned monthly or quarterly. ...
... Dirt and dust can prevent an asset from performing according to its specifications. For example, a part may be correctly calibrated, but the fan is not sufficiently cooling it, leading the entire computer to underperform.
Stick to the Calibrating Plan: Calibrations are often certified for a set period, after which the accuracy of your product may begin to deteriorate. It is critical to adhere to the schedule established by the manufacturer or calibration lab for each product. Calibration plans are typically based on:
o Instrument type
o How is the instrument used?
o How frequently the instrument is utilised
o Its usage environment
o Accuracy is required
Describe your Equipment: When sending an asset out for calibration or bringing a calibration engineer into your company, make sure to provide particular information on the equipment. Tell the lab or engineer why you're calibrating it, such as if you've seen a decrease in accuracy or something isn't working properly. Describe where you've witnessed the deterioration and how long the problem has been there. Providing context can help inform what tests are performed to confirm the product's accuracy.
Understand the Product's Measurement Limitations: Calibration does not ensure that every measurement is accurate. A calibration lab or mobile calibration engineer follows specifications for what tests to perform on each product to calibrate it. That is, the item in question is tested by the manufacturer's standards rather than at every single test point conceivable. If you utilise a product to the limit of its measurement uncertainty, the basic calibration recommended by the manufacturer may not be sufficient. Inquire with the lab about additional calibration points based on how you want to use the product. In this manner, you can be confident that the calibration is correct for your needs.
Inspect for Transportation Damage: If you packed and delivered the item for calibration, double-check it when it arrives. It is critical to ensure that everything is working properly before reintroducing it into your production line. Perform a few checks on sanity to ensure that it was not damaged in transit from the calibration lab to you. When a product is dropped or handled roughly, the precision and accuracy of the calibration can suffer.
Conduct an MSA Before and After Calibration: Measurement system analysis (MSA) is an excellent method to determine if you need to calibrate your equipment or if it was improperly calibrated when it was returned from a calibration facility. This study is best used before and after calibration, so you have before and after data points to compare. MSA is a mathematical method for calculating variation in a measuring procedure. It is used to certify the accuracy, precision, and stability of the measurements and controls being employed.
Calibration of instruments is more than a normal task; it is a key component of sustaining smooth and efficient processes in a variety of industries. The benefits of certified instrument calibration training are numerous, ranging from understanding precise data for informed decision-making to regulatory compliance and cost savings. After successfully completing this Certified Instruments Calibration - E-learning course, user will be able to: Learn the fundamentals of calibration, such as calibration needs, why we need calibration, equipment selection, equipment kinds, metrological, mechanical, thermal, and electro-technical traceability, calibration agency selection, and so on.
Source link: https://www.calibrationlaboratory.in
Add Comment
Business Articles
1. Lucintel Forecasts The Glass Fiber In The Global Marine Market To Grow With A Cagr Of 3.7% From 2024 To 2030Author: Lucintel LLC
2. Lucintel Forecasts The Glass Fiber In The Global E&e Market To Grow With A Cagr Of 3.9% From 2024 To 2030
Author: Lucintel LLC
3. Lucintel Forecasts The Global Frp Pole In Telecommunication Market To Grow With A Cagr Of 6.5% From 2024 To 2030
Author: Lucintel LLC
4. Lucintel Forecasts The Global Frp Pole In Power Transmission & Distribution Market To Grow With A Cagr Of 6% From 2024 To 2030
Author: Lucintel LLC
5. Lucintel Forecasts The Global Frp Pipe In Oil And Gas Market To Grow With A Cagr Of 5.1% From 2024 To 2030
Author: Lucintel LLC
6. Lucintel Forecasts The Global Frp Pipe In Chemical Market To Grow With A Cagr Of 3.6% From 2024 To 2030
Author: Lucintel LLC
7. Adopt A Modern Telecom Commission Management System To Fix Revenue Leakages
Author: Kevin
8. Quality Steel Pipes And Tubes With Commitment And Trusted Service
Author: CONTENT EDITOR FOR SAMPHIRE IT SOLUTIONS PVT LTD
9. Lucintel Forecasts The Global Foam Core For The Construction Market To Grow With A Cagr Of 3.7% From 2024 To 2030
Author: Lucintel LLC
10. How Important Is Mutual Fund?
Author: Sagar Shah
11. What Do You Need To Know About Customize Your Own Clothes
Author: Guangzhou Beianji Clothing
12. Detailed Tips To Choose Quality Cabinets And Joinery Melbourne
Author: William Harvey
13. Lucintel Forecasts The Global Foam Core For The Transportation Market To Grow With A Cagr Of 5.4% From 2024 To 2030
Author: Lucintel LLC
14. Silicone Sealing Foam Cord: The Valuable Option For You
Author: Dongguan Senma New Materials Technology Co., Ltd
15. How Investment Banking Companies And Credit Solutions Elevate Wealth Management
Author: Drishti Desai