ALL >> General >> View Article
Lean Six Sigma, Lean & Six Sigma: A Definitive Guide
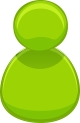
In today's competitive business landscape, organizations strive to improve efficiency, reduce waste, and deliver high-quality products and services. Two popular methodologies that have gained widespread recognition for achieving these goals are Lean and Six Sigma. While Lean focuses on eliminating waste and streamlining processes, Six Sigma aims at reducing variations and defects. Combining these methodologies, Lean Six Sigma provides a powerful approach to process improvement and organizational excellence. Embark on a dynamic learning journey with Six Sigma course training, acquiring vital problem-solving and data analysis techniques to make a lasting impact. This definitive guide explores the key concepts, principles, tools, and benefits of Lean Six Sigma.
What is Lean?
Lean, often referred to as Lean Manufacturing or Lean Thinking, originated in the manufacturing industry and was popularized by Toyota's renowned Toyota Production System (TPS). The core principle of Lean is to maximize customer value while minimizing waste. It identifies and eliminates non-value-added activities or "waste" in processes. The key ...
... types of waste identified in Lean are:
Transportation: Unnecessary movement of materials or products.
Inventory: Overstock that locks up funds and resources.
Motion: Unnecessary movement of people or equipment.
Waiting: Idle time and delays in the process.
Overproduction: Producing more than what is required by the customer.
Over processing: Bringing unnecessary activities to the table.
Defects: Rework or errors that lead to defects.
Skills underutilization: Not fully utilizing the skills and capabilities of employees.
Lean adopts a systematic approach to eliminate waste by focusing on continuous improvement, standardized work, visual management, and empowering employees to identify and solve problems. Secure a globally recognized Six Sigma certification in Chennai, attesting to your prowess in statistical analysis and process improvement methodologies.
What is Six Sigma?
Six Sigma is a data-driven methodology that focuses on reducing process variations and defects to achieve consistent and high-quality results. Motorola invented it in the 1980s, and businesses like General Electric went on to make it mainstream. The term "Six Sigma" refers to a statistical concept that represents a process performance level with a defect rate of 3.4 parts per million opportunities (PPM). Select from the finest Six Sigma training options available, offering profound knowledge and hands-on experience for organizational excellence.
The key steps in the Six Sigma methodology, commonly known as DMAIC, are:
Define: Clearly state the issue, the objectives of the project, and the demands of the client.
Measure: Identify relevant metrics and collect data to measure the current performance.
Analyse: Analyse the data to identify the root causes of variations and defects.
Improve: Implement solutions to address the root causes and improve the process.
Control: Establish control measures to sustain the improvements and monitor performance.
Six Sigma utilizes statistical tools and techniques, such as process capability analysis, control charts, regression analysis, and hypothesis testing, to make data-driven decisions and drive process improvements.
What is Lean Six Sigma?
Lean Six Sigma combines the principles and methodologies of Lean and Six Sigma to create a comprehensive approach to process improvement and waste reduction. Lean Six Sigma aims to achieve operational excellence by eliminating waste and reducing process variations simultaneously. It leverages the strengths of both Lean and Six Sigma, integrating Lean's focus on waste elimination and process flow with Six Sigma's emphasis on data analysis and defect reduction. Join a leading Six Sigma training institute to become an adept practitioner of process improvement, fostering a culture of continuous quality enhancement.
The integration of Lean and Six Sigma brings several benefits, including:
Waste Reduction: Lean Six Sigma identifies and eliminates waste throughout the entire value stream, resulting in improved process efficiency and cost reduction.
Quality Improvement: By reducing process variations and defects, Lean Six Sigma enhances product and service quality, leading to increased customer satisfaction.
Faster Process Cycle Times: Streamlining processes and eliminating non-value-added activities allows for faster cycle times, enabling organizations to respond to customer demands more efficiently.
Employee Engagement: Lean Six Sigma promotes a culture of continuous improvement and empowers employees to actively participate in problem-solving and process improvement initiatives.
Data-Driven Decision Making: The use of statistical tools and analysis in Lean Six Sigma enables organizations to make informed decisions based on reliable data rather than relying on assumptions or guesswork.
Business Growth and Competitive Advantage: Lean Six Sigma provides organizations with a competitive edge by improving operational efficiency, reducing costs, and delivering high-quality products and services.
Customer Focus: Lean Six Sigma emphasizes understanding customer needs and aligning processes to meet those needs, resulting in improved customer satisfaction and loyalty.
End Note
Lean Six Sigma is a powerful methodology that combines the principles of Lean and Six Sigma to drive process improvement, waste reduction, and organizational excellence. By eliminating waste and reducing process variations, organizations can achieve higher levels of operational efficiency, improved quality, and increased customer satisfaction. Implementing Lean Six Sigma requires a systematic approach, data-driven decision-making, and a culture of continuous improvement. With its broad applicability across industries, Lean Six Sigma has proven to be a valuable tool for organizations seeking to achieve sustainable growth, streamline processes, and deliver superior products and services in today's competitive marketplace. Embrace a data-driven approach to process optimization through comprehensive Six Sigma training in Bangalore, enabling continuous improvement and efficiency mastery.
Add Comment
General Articles
1. Categorization Of Plant Life CycleAuthor: Anthea Johnson
2. Commercial Spaces Need Style Too! Transforming Cafés & Resorts With Custom Pergolas
Author: Noor Mariam
3. Level Up Your Hana Adventure: Why An Audio Tour Is Your Best Road Trip Companion
Author: Katie Law
4. Best Erp Software Solution Company In Noida For Schools And Colleges
Author: CONTENT EDITOR FOR SAMPHIRE IT SOLUTIONS PVT LTD
5. Hinduism: Environmental Friendliness And Protecting Nature
Author: Chaitanya Kumari
6. From Ai To App Store: How Generative Tech Is Reshaping Ios Experiences
Author: Sara Wilson
7. Faston Service In Noida — Reliable, Affordable & Quick Home Ac Repair Services
Author: faston services
8. What Are The Uses And Benefits Of A Vegetable And Fruit Dryer?
Author: DYNAMIC DRYERS INTERNATIONAL
9. Primary Care Without Insurance In Raleigh
Author: satyamprimarycare
10. All Four Paws Offers Champion English Cream Golden Retriever Puppies In Indiana
Author: Geroge
11. Box Truck Wraps: The Ultimate Moving Billboard For Your Brand
Author: Saifee Signs
12. Generative Ai And Data Science Course In Hyderabad
Author: Hari
13. Mca Guidelines For Company Name
Author: Startupporta Business Services
14. Seo Services In Chennai: Boost Your Online Visibility With Proven Strategies
Author: istudio technologies
15. Best Internet Marketing Service In India
Author: Matrix Web Studio