ALL >> Business >> View Article
The Evolution Of Tube Manufacturing: From Traditional Methods To Modern Techniques
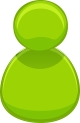
Tubes have been an essential component of human civilization for centuries, serving a multitude of purposes across various industries. Over time, the manufacturing of tubes has witnessed a remarkable evolution, transitioning from labor-intensive traditional methods to highly efficient and innovative modern techniques. This article delves into the fascinating journey of tube manufacturing, tracing the historical roots and highlighting the significant advancements that have reshaped this critical industry.
Hardware Tubes and Flat Bars: Versatile Components for Various Applications
Hardware tubes and flat bars are fundamental components used across a wide range of industries and applications. These versatile shapes come in various materials and sizes, making them essential for construction, manufacturing, and DIY projects. In this article, we will explore the characteristics, applications, and benefits of hardware tubes and flat bars.
Hardware Tubes:
Hardware tubes are cylindrical hollow structures typically made from materials such as steel, aluminum, brass, or copper. They are available in various sizes ...
... and thicknesses, making them suitable for diverse applications. Here are some key characteristics and applications of hardware tubes:
Characteristics:
1. Versatility: Hardware tubes are available in a wide range of diameters and lengths, making them adaptable to various projects.
2. Strength: Depending on the material and thickness, tubes can offer excellent structural strength, making them ideal for load-bearing applications.
3. Corrosion Resistance: Many hardware tubes are coated or made from materials that resist corrosion, extending their lifespan.
4.
Applications:
1. Construction: Hardware tubes are used in construction for structural support, scaffolding, and the creation of handrails and guardrails.
2. Plumbing: They are essential components for water and gas distribution systems, with copper and PVC tubes commonly used.
3. Transportation: In the automotive and aerospace industries, tubes are used for components such as exhaust systems, roll cages, and hydraulic lines.
4. Manufacturing: Tubes play a crucial role in the manufacturing of furniture, machinery, and agricultural equipment.
5. DIY Projects: Hardware tubes are popular among DIY enthusiasts for creating structures like shelving units, furniture frames, and garden trellises.
I. Early Beginnings: The Birth of Tube Manufacturing
The history of tube manufacturing dates back to ancient civilizations. Early cultures, such as the Egyptians, Romans, and Chinese, crafted primitive tubes for irrigation, transportation, and musical instruments. These tubes were typically made from materials like bamboo, clay, and animal bladders, representing the first steps in tube development.
II. The Industrial Revolution: A Paradigm Shift
The Industrial Revolution marked a turning point in tube manufacturing. Traditional handcrafted methods were replaced by mechanized processes, revolutionizing production. Key developments during this era include:
1. The Invention of Seamless Tubes: In 1824, French engineer Léon Guillet developed a method to produce seamless iron tubes, which were a significant improvement over earlier seamed tubes in terms of strength and durability.
2. The Bessemer Process: Sir Henry Bessemer's 1856 invention of the Bessemer converter allowed for the mass production of steel, enabling the creation of stronger and more versatile tubes.
3. The Rise of Steel Tubes: Steel tubes gained popularity due to their superior strength and corrosion resistance, making them suitable for various applications, from transportation to infrastructure.
III. Twentieth Century Innovations
The 20th century brought further advancements in tube manufacturing:
1. Welded Tubes: The development of electric resistance welding (ERW) and submerged arc welding (SAW) techniques allowed for the mass production of welded tubes, expanding their range of applications.
2. Aluminum Tubes: The use of aluminum as a tube material gained traction, particularly in the aviation industry, due to its lightweight and corrosion-resistant properties.
3. Plastic Tubes: The mid-20th century witnessed the introduction of plastic tubes, which found applications in packaging, plumbing, and electrical conduits.
IV. Modern Techniques in Tube Manufacturing
The 21st century has ushered in a new era of tube manufacturing, marked by cutting-edge technologies and innovative materials. Here are some of the modern techniques reshaping the industry:
A. Extrusion Technology
1. Continuous Casting: Continuous casting processes allow for the production of long, continuous metal tubes with improved structural integrity.
2. Hot Extrusion: Hot extrusion techniques are used to create seamless tubes from metals like aluminum, copper, and titanium.
B. Advanced Materials
1. Composite Tubes: The development of composite materials, such as carbon fiber-reinforced composites, has revolutionized tube manufacturing by offering lightweight and high-strength solutions.
2. Nano-Enhanced Tubes: Nanotechnology has enabled the creation of tubes with enhanced properties, including improved thermal conductivity, electrical conductivity, and resistance to wear.
C. Precision Machining
1. Computer Numerical Control (CNC) Machining: CNC machining allows for precise and customizable tube production, particularly in industries like aerospace and automotive.
2. 3D Printing: Additive manufacturing, including 3D printing, is changing the way tubes are produced by allowing for complex and customized designs.
D. Automated Quality Control
1. Non-Destructive Testing (NDT): NDT methods, such as ultrasonic testing and radiographic testing, ensure the integrity and quality of tubes without damaging them.
2. Robotic Inspection: Automated robotic systems are increasingly used for inspecting tubes, improving accuracy and efficiency.
V. Specialized Tube Manufacturing
Modern tube manufacturing techniques have facilitated the production of specialized tubes for various industries and applications:
A. Medical Tubes: Precision and biocompatible materials are used in the production of medical tubes, including catheters, endoscopes, and intravenous tubes.
B. Automotive Tubes: Tubes for automotive applications, such as exhaust systems, fuel lines, and air conditioning, are designed for durability and resistance to extreme conditions.
C. Aerospace Tubes: Lightweight and high-strength materials like titanium and composites are used in aerospace tube manufacturing, ensuring reliability in aviation and space exploration.
D. Energy Sector Tubes: Tubes in the energy sector, such as heat exchanger tubes and oil and gas pipelines, must meet stringent standards for safety and efficiency.
VI. Sustainability in Tube Manufacturing
In the 21st century, sustainability has become a significant focus in tube manufacturing:
1. Recycled Materials: The use of recycled materials, especially in steel and aluminum tubes, reduces the environmental impact of production.
2. Energy-Efficient Processes: Manufacturers are adopting energy-efficient technologies to reduce greenhouse gas emissions and lower production costs.
3. Reduced Waste: Minimizing waste through precision machining and recycling programs contributes to sustainable tube manufacturing.
VII. Future Trends and Challenges
The future of tube manufacturing holds exciting possibilities:
1. Smart Tubes: Integration of sensors and data-tracking capabilities in tubes for monitoring structural integrity and performance in real-time.
2. Biofabricated Tubes: Advancements in biotechnology may lead to the development of tubes made from biological materials, offering unique properties and biodegradability.
3. Nanotubes: Exploration of carbon nanotubes for applications in electronics, materials science, and even space elevators.
Challenges include:
1. Environmental Impact: Continued efforts are needed to reduce the environmental impact of tube manufacturing, particularly in terms of energy consumption and emissions.
2. Quality Control: As tubes become more specialized, maintaining high levels of quality control becomes increasingly crucial.
3. Supply Chain Resilience: Ensuring a stable supply chain, especially for critical industries like aerospace and healthcare, is essential.
Conclusion
The evolution of tube manufacturing from its humble beginnings to the cutting-edge techniques of the 21st century is a testament to human innovation and ingenuity. These cylindrical structures, once crafted from rudimentary materials by hand, have transformed into high-tech, precision-engineered components that underpin countless industries.
As the world continues to advance, the future of tube manufacturing holds the promise of even more groundbreaking developments. From smart tubes that can monitor their condition to bio fabricated tubes with unprecedented properties, the possibilities are limitless. Yet, amidst the technological marvels, the industry must remain committed to sustainability and quality, ensuring that tubes continue to play a vital role in our increasingly complex and interconnected world.
Add Comment
Business Articles
1. Lucintel Forecasts The Glass Fiber In The Global Marine Market To Grow With A Cagr Of 3.7% From 2024 To 2030Author: Lucintel LLC
2. Lucintel Forecasts The Glass Fiber In The Global E&e Market To Grow With A Cagr Of 3.9% From 2024 To 2030
Author: Lucintel LLC
3. Lucintel Forecasts The Global Frp Pole In Telecommunication Market To Grow With A Cagr Of 6.5% From 2024 To 2030
Author: Lucintel LLC
4. Lucintel Forecasts The Global Frp Pole In Power Transmission & Distribution Market To Grow With A Cagr Of 6% From 2024 To 2030
Author: Lucintel LLC
5. Lucintel Forecasts The Global Frp Pipe In Oil And Gas Market To Grow With A Cagr Of 5.1% From 2024 To 2030
Author: Lucintel LLC
6. Lucintel Forecasts The Global Frp Pipe In Chemical Market To Grow With A Cagr Of 3.6% From 2024 To 2030
Author: Lucintel LLC
7. Adopt A Modern Telecom Commission Management System To Fix Revenue Leakages
Author: Kevin
8. Quality Steel Pipes And Tubes With Commitment And Trusted Service
Author: CONTENT EDITOR FOR SAMPHIRE IT SOLUTIONS PVT LTD
9. Lucintel Forecasts The Global Foam Core For The Construction Market To Grow With A Cagr Of 3.7% From 2024 To 2030
Author: Lucintel LLC
10. How Important Is Mutual Fund?
Author: Sagar Shah
11. What Do You Need To Know About Customize Your Own Clothes
Author: Guangzhou Beianji Clothing
12. Detailed Tips To Choose Quality Cabinets And Joinery Melbourne
Author: William Harvey
13. Lucintel Forecasts The Global Foam Core For The Transportation Market To Grow With A Cagr Of 5.4% From 2024 To 2030
Author: Lucintel LLC
14. Silicone Sealing Foam Cord: The Valuable Option For You
Author: Dongguan Senma New Materials Technology Co., Ltd
15. How Investment Banking Companies And Credit Solutions Elevate Wealth Management
Author: Drishti Desai