ALL >> Business >> View Article
Choosing The Best 304 Stainless Steel Welding Wire
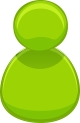
Are you planning to weld 304 stainless steel and want to ensure a strong, durable weld? Selecting the right welding wire is crucial for a successful welding project. In this article, we will explore the factors to consider when selecting the best 304 stainless steel welding wire for your project, as well as some safety precautions and tips for effective use.
Factors to Consider When Selecting 304 Stainless Steel Welding Wire
Several factors must be considered when choosing the best welding wire for your 304 stainless steel project, from welding wire manufacturers. These include:
Type and Thickness of Metal
The type and thickness of the metal being welded are essential considerations when selecting welding wire. For instance, thin sheets of stainless steel require a more basic type of welding wire, such as ER304, while thicker materials require stronger welding wire, such as ER308.
Welding ...
... Position
The welding position is also an important consideration when selecting a welding wire. For example, overhead welding requires a specific type of welding wire that can prevent spatter and avoid welding defects.
Strength and Appearance of Weld
The desired strength and appearance of your weld should also be considered when selecting a welding wire. For instance, if you need a strong weld with good corrosion resistance, you should consider a higher-grade welding wire, such as ER316.
Shielding Gas
The type of shielding gas used can also impact the success of your welding project. Ensure that you select the appropriate shielding gas for the job.
Diameter of Welding Wire
Choose the correct diameter of welding wire for the thickness of the metal being welded. Using the wrong diameter of welding wire can result in a weak weld and poor penetration.
Manufacturer's Reputation
Choose a reputable manufacturer with a proven track record of producing high-quality welding wire.
Choosing the Best 304 Stainless Steel Welding Wire
304 stainless steel welding wire is a popular choice for welding applications due to its excellent corrosion resistance and high strength.
When selecting 304 stainless steel welding wire, important factors to consider include wire diameter, type and grade, and the specific application it will be used for.
Proper safety precautions should also be taken when working with 304 stainless steel welding wire.
Types and Grades of 304 Stainless Steel Welding Wire
304 stainless steel welding wire comes in several different types and grades. The most common types include ER304, ER308, and ER316. ER304 is a basic type of welding wire that is suitable for welding thin sheets of stainless steel. ER308 is a stronger wire that is suitable for welding thicker stainless steel materials, while ER316 is a higher grade of wire that is suitable for welding stainless steel alloys with molybdenum.
However, it is worth noting that 304 stainless steel welding wire may not be suitable for all applications. For instance, in some cases, a different type of welding wire may be more appropriate due to its specific properties or cost-effectiveness.
Common Applications for 304 Stainless Steel Welding Wire
304 stainless welding wire is used in a wide range of applications, including automotive, construction, and aerospace industries. It is commonly used for welding stainless steel pipes, tanks, and other structures. The wire is also used for welding stainless steel parts in food processing equipment, medical devices, and other applications where corrosion resistance is critical.
Tips and Techniques for Using 304 Stainless Steel Welding Wire Effectively
To achieve the best results when using 304 stainless steel welding wire, it is important to follow some key tips and techniques. First, ensure that the welding surface is clean and free of any contaminants. Use the correct diameter of welding wire for the thickness of the metal being welded, and select the appropriate shielding gas for the job. It is also important to maintain the correct welding angle and travel speed to ensure a strong, durable weld.
However, it's important to note that welding techniques and tips can vary depending on the specific application and project requirements. Always consult with a welding professional or manufacturer for specific recommendations and guidelines.
Comparisons: How Does 304 Stainless Steel Welding Wire Stack Up Against Other Options?
Compared to other types of welding wire, such as aluminum and carbon steel, 304 stainless steel welding wire is a more expensive option. However, it is also more resistant to corrosion and wear, making it a popular choice for projects where durability is critical.
Safety Precautions When Working with 304 Stainless Steel Welding Wire
When working with 304 stainless steel welding wire, it is important to take proper safety precautions to avoid injury or damage to equipment. Always wear protective clothing, including gloves and eye protection, when welding. Follow all manufacturer's instructions and guidelines for using the welding wire, and ensure that the work area is well-ventilated to prevent exposure to fumes and gases.
Choosing the Right Welding Wire Manufacturer
Choosing a reputable welding wire manufacturer is crucial for ensuring the quality and reliability of the welding wire. When selecting a manufacturer, consider factors such as their experience in the industry, the quality control processes they have in place, and their customer service and support.
In conclusion, selecting the best 304 stainless steel welding wire is critical to ensuring a successful welding project. Consider the specific needs of the project, including the type and thickness of metal being welded, and select the appropriate type and grade of welding wire. Follow key tips and techniques to ensure a strong, durable weld, and take proper safety precautions when working with 304 stainless steel welding wire to avoid injury or damage to equipment. Finally, choose a reputable welding wire manufacturer to ensure the quality and reliability of the welding wire.
Add Comment
Business Articles
1. Lucintel Forecasts The Glass Fiber In The Global Marine Market To Grow With A Cagr Of 3.7% From 2024 To 2030Author: Lucintel LLC
2. Lucintel Forecasts The Glass Fiber In The Global E&e Market To Grow With A Cagr Of 3.9% From 2024 To 2030
Author: Lucintel LLC
3. Lucintel Forecasts The Global Frp Pole In Telecommunication Market To Grow With A Cagr Of 6.5% From 2024 To 2030
Author: Lucintel LLC
4. Lucintel Forecasts The Global Frp Pole In Power Transmission & Distribution Market To Grow With A Cagr Of 6% From 2024 To 2030
Author: Lucintel LLC
5. Lucintel Forecasts The Global Frp Pipe In Oil And Gas Market To Grow With A Cagr Of 5.1% From 2024 To 2030
Author: Lucintel LLC
6. Lucintel Forecasts The Global Frp Pipe In Chemical Market To Grow With A Cagr Of 3.6% From 2024 To 2030
Author: Lucintel LLC
7. Adopt A Modern Telecom Commission Management System To Fix Revenue Leakages
Author: Kevin
8. Quality Steel Pipes And Tubes With Commitment And Trusted Service
Author: CONTENT EDITOR FOR SAMPHIRE IT SOLUTIONS PVT LTD
9. Lucintel Forecasts The Global Foam Core For The Construction Market To Grow With A Cagr Of 3.7% From 2024 To 2030
Author: Lucintel LLC
10. How Important Is Mutual Fund?
Author: Sagar Shah
11. What Do You Need To Know About Customize Your Own Clothes
Author: Guangzhou Beianji Clothing
12. Detailed Tips To Choose Quality Cabinets And Joinery Melbourne
Author: William Harvey
13. Lucintel Forecasts The Global Foam Core For The Transportation Market To Grow With A Cagr Of 5.4% From 2024 To 2030
Author: Lucintel LLC
14. Silicone Sealing Foam Cord: The Valuable Option For You
Author: Dongguan Senma New Materials Technology Co., Ltd
15. How Investment Banking Companies And Credit Solutions Elevate Wealth Management
Author: Drishti Desai