ALL >> Business >> View Article
Abs Plastic Machining 101: Essential Strategies For Success
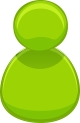
Are you looking to create high-quality, precision parts using ABS plastic? Then, ABS plastic machining is a crucial skill that you need to master. ABS plastic is a highly versatile and durable material that is widely used in various industries, including automotive, aerospace, and electronics. In this article, we will explore the essential strategies and techniques for successful ABS plastic machining.
Getting Started with ABS Plastic Machining: Tools and Equipment
Before diving into ABS machining, it's important to ensure you have the right tools and equipment for the job. Some essential tools for ABS plastic machining include:
CNC machines: These machines use computerized controls to cut and shape ABS plastic with precision and accuracy.
Lathes: Lathes are used for turning and shaping ABS plastic into cylindrical shapes.
Milling machines: Milling machines can be used to create complex shapes and contours in ABS plastic.
Cutting tools: ...
... High-speed steel (HSS) or carbide cutting tools can be used for ABS plastic machining. HSS tools are ideal for low-volume work, while carbide tools are better suited to high-volume production.
It's also important to have a dust collection system in place to keep the work area clean and free of debris, as well as safety equipment such as gloves, goggles, and dust masks.
ABS Plastic Machining 101
Machining ABS plastic involves using specific tools and techniques to shape and cut ABS plastic.
The article covers the essential strategies, techniques, and tools needed for successful ABS plastic machining.
It also includes tips for achieving precision, overcoming common challenges, and optimizing machining processes.
Understanding ABS Plastic: Properties and Applications
ABS plastic is a thermoplastic polymer that is composed of three monomers: acrylonitrile, butadiene, and styrene. This combination of materials gives ABS plastic its unique properties, including excellent impact resistance, toughness, and heat resistance.
ABS plastic is used in a wide range of applications, including:
Automotive parts, such as dashboards, bumpers, and trim
Electronics housings, such as computer cases and phone covers
Toys and recreational equipment, such as LEGO bricks and golf club heads
Medical devices, such as incubators and blood analyzers
Understanding the properties and applications of ABS plastic is essential for successful machining.
Essential Techniques for Successful ABS Plastic Machining
To achieve successful ABS plastic machining, it's important to use the right techniques. Some essential techniques for ABS plastic machining include:
Maintaining a constant feed rate: A consistent feed rate helps to ensure a uniform finish and prevent chipping or cracking.
Using sharp cutting tools: Dull tools can cause tearing and poor surface finish. It's important to keep cutting tools sharp and replace them when necessary.
Minimizing heat buildup: ABS plastic can soften and deform if it gets too hot. To prevent this, it's important to use coolant and keep the cutting tools sharp.
Clamping the workpiece securely: This helps to prevent movement and vibration during machining, which can cause poor surface finish and accuracy.
Choosing the Right Cutting Tools for ABS Plastic Machining
Choosing the right cutting tools is essential for successful ABS plastic machining. HSS and carbide cutting tools are both suitable for ABS plastic machining, but carbide tools are generally preferred for their durability and resistance to wear.
When selecting cutting tools for ABS plastic machining, it's important to consider factors such as the tool's geometry, coatings, and rake angle. A high rake angle helps to reduce cutting forces and prevent heat buildup, while a low rake angle can provide a better surface finish.
Tips for Achieving Precision in ABS Plastic Machining
Achieving precision in ABS plastic machining requires attention to detail and careful planning. Here are some tips for achieving precision:
Using high-quality cutting tools: High-quality cutting tools can provide better accuracy and a smoother finish.
Measuring and marking the workpiece: Measuring and marking the workpiece can help to ensure accurate cuts and prevent mistakes.
Using fixtures and jigs: Fixtures and jigs can help to hold the workpiece securely and ensure consistent positioning during machining.
Common Challenges in ABS Plastic Machining and How to Overcome Them
ABS plastic machining can present some common challenges, including:
Warping and distortion: ABS plastic can warp and distort if it gets too hot. To prevent this, it's important to use coolant and minimize heat buildup.
Poor surface finish: Poor surface finish can be caused by a range of factors, including dull cutting tools, improper feed rate, and vibration during machining.
Chipping and cracking: Chipping and cracking can be caused by excessive cutting forces or improper tool geometry.
To overcome these challenges, it's important to use the right techniques and cutting tools, as well as to maintain a clean and well-lubricated work area.
Best Practices for Surface Finishing in ABS Plastic Machining
Surface finishing is an important aspect of ABS plastic machining, as it can affect the part's appearance, functionality, and durability. Here are some best practices for surface finishing:
Using the right abrasives: Different abrasives can be used for different surface finishes. For example, fine-grit sandpaper can be used for a smooth finish, while coarse-grit sandpaper can be used for a textured finish.
Sanding in the same direction: Sanding in the same direction can help to achieve a uniform surface finish and prevent scratches.
Using a polishing compound: A polishing compound can be used to achieve a high-gloss finish on ABS plastic.
Maximizing Efficiency: Strategies for Optimizing ABS Plastic Machining Processes
Maximizing efficiency in ABS plastic machining requires careful planning and optimization of the machining process. Here are some strategies for optimizing ABS plastic machining processes:
Using the right cutting parameters: Adjusting the cutting speed, feed rate, and depth of cut can help to optimize the machining process and improve efficiency.
Minimizing setup time: Reducing setup time can help to improve efficiency and productivity. Using fixtures and jigs can help to hold the workpiece securely and reduce setup time.
Automating the process: Automating the machining process can help to improve efficiency and reduce the risk of errors.
Troubleshooting Guide: Solutions to Common Issues in ABS Plastic Machining
Even with the best techniques and equipment, issues can still arise during ABS plastic machining. Here are some common issues and their solutions:
Chipping and cracking: Reduce cutting forces, use sharper cutting tools, and adjust tool geometry.
Warping and distortion: Use coolant, minimize heat buildup, and ensure a secure workpiece setup.
Poor surface finish: Adjust the feed rate, use sharper cutting tools, and adjust the rake angle.
By using these troubleshooting tips, manufacturers and fabricators can overcome common issues and achieve successful ABS plastic machining.
In conclusion, ABS plastic machining is an essential skill for manufacturers and fabricators looking to create high-quality, precision parts. By understanding the properties and applications of ABS plastic, using the right techniques and cutting tools, and optimizing the machining process, it's possible to achieve successful ABS plastic machining and create durable, functional parts.
Add Comment
Business Articles
1. Lucintel Forecasts The Glass Fiber In The Global Marine Market To Grow With A Cagr Of 3.7% From 2024 To 2030Author: Lucintel LLC
2. Lucintel Forecasts The Glass Fiber In The Global E&e Market To Grow With A Cagr Of 3.9% From 2024 To 2030
Author: Lucintel LLC
3. Lucintel Forecasts The Global Frp Pole In Telecommunication Market To Grow With A Cagr Of 6.5% From 2024 To 2030
Author: Lucintel LLC
4. Lucintel Forecasts The Global Frp Pole In Power Transmission & Distribution Market To Grow With A Cagr Of 6% From 2024 To 2030
Author: Lucintel LLC
5. Lucintel Forecasts The Global Frp Pipe In Oil And Gas Market To Grow With A Cagr Of 5.1% From 2024 To 2030
Author: Lucintel LLC
6. Lucintel Forecasts The Global Frp Pipe In Chemical Market To Grow With A Cagr Of 3.6% From 2024 To 2030
Author: Lucintel LLC
7. Adopt A Modern Telecom Commission Management System To Fix Revenue Leakages
Author: Kevin
8. Quality Steel Pipes And Tubes With Commitment And Trusted Service
Author: CONTENT EDITOR FOR SAMPHIRE IT SOLUTIONS PVT LTD
9. Lucintel Forecasts The Global Foam Core For The Construction Market To Grow With A Cagr Of 3.7% From 2024 To 2030
Author: Lucintel LLC
10. How Important Is Mutual Fund?
Author: Sagar Shah
11. What Do You Need To Know About Customize Your Own Clothes
Author: Guangzhou Beianji Clothing
12. Detailed Tips To Choose Quality Cabinets And Joinery Melbourne
Author: William Harvey
13. Lucintel Forecasts The Global Foam Core For The Transportation Market To Grow With A Cagr Of 5.4% From 2024 To 2030
Author: Lucintel LLC
14. Silicone Sealing Foam Cord: The Valuable Option For You
Author: Dongguan Senma New Materials Technology Co., Ltd
15. How Investment Banking Companies And Credit Solutions Elevate Wealth Management
Author: Drishti Desai