ALL >> Business >> View Article
Concrete Block Vs. Traditional Brick Construction - A Comparative Analysis
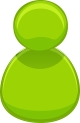
In the world of construction, the choice of materials can significantly impact the quality, cost, and durability of a building. Two widely used materials for building exteriors are blocks and traditional bricks. In this article, we will provide a comparative analysis of these two construction materials, highlighting their respective advantages and disadvantages.
1. Cost
When it comes to cost, blocks generally have an edge over traditional bricks. Blocks are mass-produced and require less labor to install, making them a more budget-friendly option. Additionally, they are larger and cover more wall area per unit, reducing construction time and overall expenses.
On the other hand, traditional bricks are often more expensive due to their production process, which involves firing clay in kilns. Bricklaying is also more labor-intensive, leading to higher construction costs. However, it's important to note that the cost of bricks can vary depending on factors such as location and availability of materials.
2. Durability
Both blocks and traditional bricks offer excellent durability when properly maintained. ...
... Blocks are known for their resistance to moisture, fire, and insects. They are also less prone to cracking or chipping, making them a suitable choice for areas with harsh weather conditions. However, they may require regular sealing or painting to maintain their appearance.
Traditional bricks, on the other hand, have been used for centuries and have proven their longevity. They can withstand the test of time and remain structurally sound for generations. While bricks are susceptible to water absorption, proper sealing and maintenance can enhance their lifespan.
3. Insulation and Energy Efficiency
One of the key differences between blocks and traditional bricks is their insulation properties. Blocks tend to have better thermal insulation due to their density, helping to regulate indoor temperatures. This can lead to energy savings by reducing heating and cooling costs.
Traditional bricks, while still providing some insulation, are generally less efficient in this regard. However, their thermal mass can contribute to stabilizing indoor temperatures and reducing temperature fluctuations.
4. Aesthetics and Design Flexibility
Traditional bricks have a timeless appeal and offer a wide range of colors, textures, and patterns. This versatility allows for unique and aesthetically pleasing designs. The use of bricks can give a building a classic, rustic, or contemporary look, depending on the choice of brick type and laying pattern.
Blocks, while not as visually diverse as bricks, have a more modern and industrial appearance. They are often used in utilitarian or minimalist designs. However, they can be painted or veneered to achieve various aesthetics.
5. Environmental Impact
Both concrete blocks and traditional bricks have environmental pros and cons. Concrete block production consumes more energy and emits more carbon dioxide than brick manufacturing. On the other hand, bricks require clay extraction, which can lead to soil erosion and habitat disruption. However, bricks can be recycled and reused more easily than blocks.
Maintenance: Preserving the Appearance and Functionality
Proper maintenance is key to extending the life of your concrete block structures and ensuring they remain aesthetically pleasing and functional. Here are some essential maintenance tasks to consider:
1. Regular Cleaning:
o Start by removing dirt, dust, and debris from the surface of the concrete blocks using a broom or pressure washer.
o For stubborn stains or mold and mildew growth, use a mixture of water and mild detergent or a specialized concrete cleaner.
o Rinse thoroughly with clean water to remove any residue.
2. Sealing:
o Depending on the finish of your blocks, consider applying a concrete sealer to protect against moisture, stains, and UV damage.
o Sealers are available in various types, including penetrating sealers and film-forming sealers. Choose the appropriate one for your specific needs.
3. Crack Inspection:
o Regularly inspect the concrete blocks for cracks, especially in areas prone to structural stress or settling.
o Small cracks can be repaired easily, preventing them from spreading and causing more significant issues.
4. Landscape Management:
o Ensure proper drainage around your concrete block structures to prevent water from pooling near the foundation, which can lead to erosion and moisture-related problems.
o Trim vegetation and trees near the structure to prevent roots from exerting pressure on the foundation.
Repairing Concrete Block Structures
Over time, concrete block structures may develop various issues that require repair. Here are common problems and steps to address them:
1. Crack Repair:
o For small cracks in the concrete blocks or mortar joints, clean the crack with a wire brush or compressed air.
o Apply a high-quality concrete patching compound to the crack, following the manufacturer's instructions.
o Smooth the patch with a trowel, ensuring it blends seamlessly with the surrounding surface.
2. Efflorescence Removal:
o Efflorescence is a white, powdery deposit that can appear on the surface of concrete blocks due to water evaporation. To remove it:
o Brush off the efflorescence using a stiff brush or scrape it off with a putty knife.
o Rinse the area with water to remove any remaining residue.
o Identify and address the underlying moisture issue to prevent efflorescence from recurring.
3. Replacing Damaged Blocks:
o In cases where blocks are severely damaged or cracked beyond repair, they should be replaced.
o Carefully remove the damaged blocks by chiseling out the mortar around them.
o Install new blocks and re-mortar them in place, ensuring proper alignment and leveling.
4. Repointing Mortar Joints:
o Mortar joints between blocks can deteriorate over time. To repoint them:
o Remove loose or deteriorated mortar from the joints using a chisel or grinder.
o Mix a fresh batch of mortar to match the color and consistency of the existing mortar.
o Fill the joints with the new mortar, ensuring a proper bond with the blocks.
o Tool the mortar joints for a neat finish.
5. Waterproofing:
o If moisture is a recurring issue, consider applying a waterproofing membrane or coating to the exterior of the concrete block structure.
o Ensure proper drainage systems are in place to redirect water away from the foundation.
Professional Assistance and Safety Precautions
While some maintenance and repair tasks can be performed by homeowners, it's crucial to recognize when to seek professional assistance, especially for complex or extensive repairs. Safety should always be a priority when working with concrete block structures. Here are some additional tips:
• Wear appropriate personal protective equipment (PPE), including safety goggles, gloves, and a dust mask when handling concrete and mortar.
• Use proper tools and equipment, such as chisels, grinders, trowels, and safety gear, to ensure safe and effective repairs.
• If you're uncertain about the severity of a structural issue, consult a structural engineer or a qualified contractor for an assessment.
Conclusion
The choice between blocks and traditional bricks ultimately depends on the specific needs and goals of a construction project. Concrete blocks are cost-effective and offer good durability and insulation properties. Traditional bricks, while pricier, provide timeless aesthetics and can be more environmentally friendly.
In the end, the decision should consider factors such as budget, climate, design preferences, and long-term maintenance. By carefully weighing these factors, builders can make an informed choice that meets both functional and aesthetic requirements for their construction project.
Add Comment
Business Articles
1. Repair And Maintenance Guide For Garden FencingAuthor: Vikram kumar
2. Lucintel Forecasts The Global Palatant Market To Grow With A Cagr Of 5% From 2024 To 2030
Author: Lucintel LLC
3. Choosing The Right Gas Regulator In Florida: A Complete Guide
Author: Technico
4. Why Deer Park Learners Trust Local Driving Instructors
Author: Aintree Driving School
5. How To Properly Install And Uninstall Your Air Conditioner System With A Low Budget
Author: Neha Jain
6. What Is The Role Of Pdca In Iso 50001?
Author: William Charles
7. Step-by-step Instructions On How To Generate Inventory Reports Quickbooks?
Author: Jack Edwards
8. How To Track Employee Work Hours Efficiently With Trackhr
Author: TrackHr App
9. From Grounded To Global: 4 Ceos Rewiring India’s Aviation Sky
Author: Skyone
10. The Role Of Automation In Modern Cloud Migration Methodology
Author: Netscribes
11. Master Photo Retouching | Steps To Become A Photo Editing Expert
Author: ukclippingpath
12. Great Dependability And Performance Are The Reasons For Extensive Use Of Hydro Pneumatic Press
Author: David Camp
13. Best Lasik Eye Surgery For A Spectacle-free Life
Author: Anil Eye Hospital
14. Industrial Oven Manufacturers In Coimbatore
Author: Heatcon Sensors
15. Plumbing In North Salt Lake: Your Guide To Reliable Services
Author: Brown Jones