ALL >> Business >> View Article
Streamlined Injection Moulding: Unlocking Potential With Purging Material For Injection Moulding
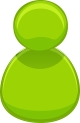
It is wise to know how Purging Material for Injection Moulding streamlines the entire process.
Injection moulding is a highly efficient and widely adopted manufacturing process used to produce a vast array of plastic products. However, over time, impurities, residues, and colourants can accumulate within the machinery, leading to defects, inconsistencies, and decreased productivity. This is where Purging Material for Injection Moulding comes into play, revolutionizing injection moulding by unlocking its true potential. Today, we will explore the significance of Purging Material and ways it streamlines injection moulding processes.
The Importance of Purging Material
Preventing Contamination and Defects
Purging Compound for Injection Molding plays a crucial role in preventing contamination within injection moulding machinery. Residues and impurities left behind during previous production runs can result in defects, such as streaks, burns, or colour inconsistencies in subsequent products. By employing purging material, manufacturers can effectively remove these contaminants, ensuring clean and defect-free ...
... production runs.
Reducing Downtime and Enhancing Efficiency
One of the primary benefits of a Purging Compound is its ability to reduce downtime and increase operational efficiency. Purging between colour or material changes helps eliminate cross-contamination, allowing for faster transition times between production runs. This not only saves valuable production time but also minimizes material waste, ultimately optimizing the overall manufacturing process.
Different Purging Material Options
Mechanical Purging Compounds
Mechanical cleansing compounds are highly effective in removing tough contaminants, such as carbonized resin or stubborn colourants. These compounds work by scrubbing the internal surfaces of the injection moulding machinery, dislodging and flushing out the unwanted residues. Mechanical purging compounds are particularly useful for challenging purging scenarios, ensuring thorough cleaning and improved equipment performance.
Chemical Purging Agents
Chemical purging agents, on the other hand, rely on a chemical reaction to break down and dissolve contaminants. They are typically used for routine maintenance and general cleaning purposes. These agents are versatile and can effectively purge various types of residues, including colourants, additives, and polymer build-up. It is essential to follow the manufacturer's instructions and guidelines when using chemical purging agents to ensure safe and efficient purging.
Best Practices for Purging Material
Proper Purging Procedures
To achieve optimal results, it is crucial to follow proper purging procedures. This includes selecting the appropriate cleaning material for the specific application, ensuring the correct purging temperature, and following the recommended purging sequence. Adhering to these procedures will maximize the efficiency of the purging process and minimize the risk of contamination or equipment damage.
Regular Maintenance and Purging
Implementing a regular maintenance schedule that includes purging with appropriate purging material is essential for long-term success in injection moulding. Regular purging helps prevent the build-up of contaminants and ensures consistent product quality. By incorporating purging into routine maintenance, manufacturers can prolong the lifespan of their equipment, minimize downtime, and maximize productivity.
About the author
Streamlined injection moulding is achievable through the effective utilization of Purging Material from UNICLEANPLUS. By recognizing the importance of purging material in preventing contamination, reducing downtime, and enhancing overall efficiency, manufacturers can unlock the true potential of injection moulding processes. It is wise to call them at +91 9021232809 to order a free sample or to place your bulk order.
Add Comment
Business Articles
1. Lucintel Forecasts The Glass Fiber In The Global Marine Market To Grow With A Cagr Of 3.7% From 2024 To 2030Author: Lucintel LLC
2. Lucintel Forecasts The Glass Fiber In The Global E&e Market To Grow With A Cagr Of 3.9% From 2024 To 2030
Author: Lucintel LLC
3. Lucintel Forecasts The Global Frp Pole In Telecommunication Market To Grow With A Cagr Of 6.5% From 2024 To 2030
Author: Lucintel LLC
4. Lucintel Forecasts The Global Frp Pole In Power Transmission & Distribution Market To Grow With A Cagr Of 6% From 2024 To 2030
Author: Lucintel LLC
5. Lucintel Forecasts The Global Frp Pipe In Oil And Gas Market To Grow With A Cagr Of 5.1% From 2024 To 2030
Author: Lucintel LLC
6. Lucintel Forecasts The Global Frp Pipe In Chemical Market To Grow With A Cagr Of 3.6% From 2024 To 2030
Author: Lucintel LLC
7. Adopt A Modern Telecom Commission Management System To Fix Revenue Leakages
Author: Kevin
8. Quality Steel Pipes And Tubes With Commitment And Trusted Service
Author: CONTENT EDITOR FOR SAMPHIRE IT SOLUTIONS PVT LTD
9. Lucintel Forecasts The Global Foam Core For The Construction Market To Grow With A Cagr Of 3.7% From 2024 To 2030
Author: Lucintel LLC
10. How Important Is Mutual Fund?
Author: Sagar Shah
11. What Do You Need To Know About Customize Your Own Clothes
Author: Guangzhou Beianji Clothing
12. Detailed Tips To Choose Quality Cabinets And Joinery Melbourne
Author: William Harvey
13. Lucintel Forecasts The Global Foam Core For The Transportation Market To Grow With A Cagr Of 5.4% From 2024 To 2030
Author: Lucintel LLC
14. Silicone Sealing Foam Cord: The Valuable Option For You
Author: Dongguan Senma New Materials Technology Co., Ltd
15. How Investment Banking Companies And Credit Solutions Elevate Wealth Management
Author: Drishti Desai