ALL >> Technology,-Gadget-and-Science >> View Article
Mastering Press Size Calculation: Essential Tips For Successful Plastic Injection Molded Projects
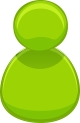
Choosing the right press size is a critical factor in the success of any plastic injection molded project. The press size determines the capacity and capabilities of the machine to produce high-quality parts. In this article, we will discuss essential tips and considerations for calculating the right press size for your project.
1. Understand Your Project Requirements
Before calculating the press size, it is crucial to have a clear understanding of your project requirements. Consider factors such as the type of plastic material, part dimensions, production volume, and desired quality standards. These requirements will help determine the appropriate tonnage and clamping force needed for the project.
2. Calculate Required Clamping Force
Clamping force refers to the pressure applied to hold the mold closed during the injection process. To calculate the required clamping force, consider the projected area of the part, the type of material being used, and the number of cavities in the mold. This calculation ensures that the press can exert enough force to securely hold ...
... the mold and prevent flash or other defects.
3. Determine the Shot Size
The shot size refers to the volume of material injected into the mold. It is important to calculate the shot size accurately to avoid overfilling or underfilling the mold. Consider factors such as the part weight, material density, and desired part characteristics. A larger shot size may require a press with a higher injection capacity.
4. Consider the Mold Size and Design
The size and design of the mold also play a crucial role in determining the appropriate press size. Evaluate the mold dimensions, including the mold base size, maximum mold opening, and mold thickness. Ensure that the chosen press can accommodate the mold size and has enough space for mold installation, cooling, and ejection.
5. Evaluate Machine Specifications and Features
When selecting a press size, it is important to consider the specifications and features of the machine. Look for features such as injection speed, injection pressure, mold open/close speed, and the ability to control temperature and pressure accurately. These features contribute to the overall performance and efficiency of the injection molding process.
6. Factor in the Material Properties
Different plastic materials have varying flow characteristics and require specific injection molding conditions. Consider the melt flow rate (MFR) or viscosity of the material, as it can impact the injection pressure and fill time. Materials with higher MFR may require higher injection pressures and larger press sizes to achieve proper flow and fill the mold adequately.
7. Account for Projected Volume
The projected volume of your production plays a significant role in determining the appropriate press size. If you anticipate high-volume production, it may be beneficial to select a larger press to accommodate increased production speed and reduce cycle times. However, for low-volume projects, a smaller press may suffice.
8. Take Part Complexity into Account
The complexity of the part can influence the required press size. Parts with intricate geometries, thin walls, or multiple undercuts may require higher clamping forces to ensure proper mold filling and ejection. Evaluate the part design and consult with a mold designer or engineer to determine the necessary press size based on part complexity.
9. Consider Future Expansion
If you anticipate future growth or plan to expand your production capabilities, it's advisable to consider a press size that allows for scalability. Choosing a press with slightly higher tonnage than your immediate requirements can provide flexibility for future projects without the need for immediate press replacement.
10. Seek Expert Advice
When in doubt, it is always beneficial to seek advice from a custom injection mould manufacturer. A professional molder can provide valuable insights, conduct thorough analysis, and recommend the most suitable press size based on your specific project requirements. With expertise an experienced molder can help ensure optimal performance, efficiency, and cost-effectiveness in your cheap injection molding process.
Conclusion
Calculating the right press size is a crucial step in ensuring the success of your injection molding solutions. By understanding your project requirements, calculating the required clamping force and shot size, considering the mold size and design, and evaluating machine specifications, you can make an informed decision. Consulting with the best injection molding company can provide valuable insights and expertise to help you select the appropriate press size for your project. Making the right choice will result in efficient production, high-quality parts, and overall project success.
Add Comment
Technology, Gadget and Science Articles
1. Best Hard Disk Data Recovery Services In BangaloreAuthor: Stellar India
2. Magnetic Tablet Wall Mount: The Ultimate Hands-free Solution
Author: John W.
3. The Risks Of Insufficient Security Protocols Enabling Unauthorized Firearm Access
Author: Weapon Tracker IoT
4. The Rise Of Ai Voice Agents: Transforming Communication
Author: precallai
5. Simplifying Pharma-validated Artwork Management With Ease
Author: 5Flow
6. Best Ui/ Ux Design Company In India | Shreeji Software
Author: Shreeji Software
7. Expert Dbt Consulting Services By Helical It Solutions Pvt Ltd
Author: Vhelical
8. Top 10 Benefits Of Moving To Umbraco Cloud
Author: Addxp Technologies
9. Why Does Every Magento 2 Store Need A Delivery Date Scheduler?
Author: Appjetty
10. How Ai Data Visualization Will Impact Global Economies?
Author: Digiprima Technologies
11. Magento 2 Mobile App: The Smartest Way To Grow Your Online Store
Author: Appjetty
12. Superon Technik: Your Ultimate Guide To Flux Core Wire And Flux Core Welding Wire
Author: SUPERON is one of India’s largest manufacturers of
13. Top 15 New Technology Trends For 2023
Author: Impaakt Magazine
14. Data Analytics: Driving Smarter Decisions For Business Growth
Author: Digiprima
15. How Openai Is Revolutionizing Content Creation In The Washington: The Future Of Blogging And Media
Author: Nagraj Rao is the Founder of GroupifyAI, a leading