ALL >> Technology,-Gadget-and-Science >> View Article
A Guide To Plastic Molding Manufacturing And Process
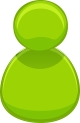
Plastic molding is a widely used manufacturing process that involves shaping plastic materials into various forms for a wide range of applications. In this article, we will provide a comprehensive guide to plastic molding manufacturing and process used by the plastic moulding manufacturers
, including an overview of the different types of plastic molding, the steps involved in the plastic molding process, and some key considerations for successful plastic molding.
Types of Plastic Molding
Injection Molding: Injection molding is the most widely used plastic molding process. It involves injecting molten plastic material into a mold cavity under high pressure. Once the plastic cools and solidifies, the mold is opened, and the finished product is ejected. Injection molding is suitable for producing complex shapes and high-volume production.
Blow Molding: Blow molding is used to produce hollow plastic parts, such as bottles and containers. It involves melting plastic material and then using compressed air to blow it into ...
... a mold cavity, where it takes the shape of the mold. Blow molding is commonly used for producing plastic containers of various sizes and shapes.
Rotational Molding: Rotational molding, also known as rotomolding, is a process used to produce large, hollow plastic parts. It involves heating plastic material in a mold that rotates slowly around two perpendicular axes.
Thermoforming: Thermoforming is a process used to produce plastic parts with a specific shape by heating a plastic sheet and then forming it over a mold using vacuum or pressure.
Steps in the Plastic Molding Process
Here is a general overview of the steps involved in the plastic molding process:
Design and Mold Preparation: The first step in the plastic molding process is to design the product and create a mold for it. The mold is typically made from steel or aluminum and is precision machined to the desired shape of the finished product.
Material Preparation: Once the mold is ready, the plastic material is prepared for molding. This typically involves melting the plastic material to a specific temperature, adding any required additives, and mixing the material to ensure uniformity.
Injection or Molding Process: Depending on the type of molding being used, the plastic material is either injected into the mold cavity under high pressure (injection molding), blown into the mold cavity (blow molding), heated and rotated in the mold cavity (rotational molding), or formed over the mold using vacuum or pressure (thermoforming).
Cooling and Solidification: After the plastic material is molded into the desired shape, it is cooled and allowed to solidify. The cooling time may vary depending on the type and thickness of the plastic material and the complexity of the part being produced.
Mold Opening and Ejection: Once the plastic has solidified, the mold is opened, and the finished product is ejected. This may involve using mechanical or hydraulic systems to release the product from the mold.
Trimming and Finishing: After the product is ejected from the mold, it may require additional trimming or finishing to remove any excess material or improve its appearance. This may involve using cutting tools, sanding, or other finishing techniques.
Key Considerations for Successful Plastic Molding
Here are some key considerations implemented by the plastic injection molding manufacturer
that are crucial for successful plastic molding:
Material Selection: The selection of the right plastic material for your specific application is crucial in plastic molding. Factors such as material properties, melt flow rate, shrinkage, and cost need to be carefully considered to ensure that the chosen material is suitable for the intended use and can be effectively molded into the desired shape.
Mold Design: The design of the mold is critical in plastic molding as it determines the final shape and quality of the product. Factors such as part design, draft angles, wall thickness, gate location, and ejection mechanism need to be considered during mold design to ensure proper filing, cooling, and ejection of the plastic material.
Process Optimization: Optimizing the plastic molding process parameters, such as temperature, pressure, and cooling time, is essential for achieving consistent and high-quality results. Process optimization involves fine-tuning the process parameters to achieve the desired part quality, minimize defects, and maximize production efficiency.
Mold Maintenance: Proper maintenance of the mold is crucial for successful plastic molding. Regular cleaning, inspection, and maintenance of the mold can help prevent defects, extend the mold's lifespan, and ensure consistent production quality.
Quality Control: Implementing robust quality control measures throughout the plastic molding process is essential to ensure that the final products meet the required specifications. This may involve inspecting and testing the raw materials, monitoring process parameters, conducting in-process inspections, and performing final product inspections to identify and address any defects or inconsistencies.
Post-Molding Operations: Depending on the specific requirements of the product, post-molding operations such as trimming, assembly, and finishing may be necessary. Proper handling and finishing of the molded parts can help achieve the desired aesthetic appearance, functionality, and performance of the final product.
Conclusion
Successful plastic molding requires careful consideration of various factors, including material selection, mold design, process optimization, mold maintenance, quality control, post-molding operations, and environmental considerations. By following best practices and implementing effective quality control measures, plastic molding can result in high-quality products that meet the desired specifications.
Add Comment
Technology, Gadget and Science Articles
1. Best Hard Disk Data Recovery Services In BangaloreAuthor: Stellar India
2. Magnetic Tablet Wall Mount: The Ultimate Hands-free Solution
Author: John W.
3. The Risks Of Insufficient Security Protocols Enabling Unauthorized Firearm Access
Author: Weapon Tracker IoT
4. The Rise Of Ai Voice Agents: Transforming Communication
Author: precallai
5. Simplifying Pharma-validated Artwork Management With Ease
Author: 5Flow
6. Best Ui/ Ux Design Company In India | Shreeji Software
Author: Shreeji Software
7. Expert Dbt Consulting Services By Helical It Solutions Pvt Ltd
Author: Vhelical
8. Top 10 Benefits Of Moving To Umbraco Cloud
Author: Addxp Technologies
9. Why Does Every Magento 2 Store Need A Delivery Date Scheduler?
Author: Appjetty
10. How Ai Data Visualization Will Impact Global Economies?
Author: Digiprima Technologies
11. Magento 2 Mobile App: The Smartest Way To Grow Your Online Store
Author: Appjetty
12. Superon Technik: Your Ultimate Guide To Flux Core Wire And Flux Core Welding Wire
Author: SUPERON is one of India’s largest manufacturers of
13. Top 15 New Technology Trends For 2023
Author: Impaakt Magazine
14. Data Analytics: Driving Smarter Decisions For Business Growth
Author: Digiprima
15. How Openai Is Revolutionizing Content Creation In The Washington: The Future Of Blogging And Media
Author: Nagraj Rao is the Founder of GroupifyAI, a leading