ALL >> Business >> View Article
The Battle Of Fr4 Vs G10: Which Material Reigns Supreme?
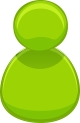
When it comes to choosing the right material for your next project, it can be a daunting task. Two of the most popular options in the world of composites are FR4 and G10. Both materials have their own unique characteristics that make them popular choices for a variety of applications. But when it comes down to it, which material truly reigns supreme? In this post, we'll take a deep dive into the battle between FR4 and G10, exploring their strengths and weaknesses to help you make an informed decision on which one is right for your next project. So buckle up and get ready to discover the ultimate winner in the battle of G10 vs FR4!
Introduction: Understanding the Differences Between FR4 and G10
FR4 vs G10 - these two materials are often compared and debated when it comes to their applications in various industries. FR4 and G10 are both composite materials made from woven fiberglass cloth and epoxy resin, but they differ in terms of their properties and applications.
FR4 is a flame-retardant ...
... material that is known for its high strength, rigidity, and electrical insulation properties. It is commonly used in printed circuit boards (PCBs), electrical insulation, and aerospace applications. On the other hand, G10 is a high-pressure fiberglass laminate that is known for its exceptional strength, durability, and resistance to moisture. It is commonly used in knife handles, gun grips, and other outdoor equipment.
Understanding the differences between FR4 and G10 is crucial in determining which material is best suited for a particular application. In the following sections, we will explore the properties of each material in detail and compare their strengths and weaknesses.
Properties of FR4: Strengths and Weaknesses Compared to G10
FR4 is a composite material made from woven fiberglass cloth and epoxy resin. It is known for its high strength, rigidity, and electrical insulation properties. FR4 has excellent dimensional stability and can withstand high temperatures, making it ideal for use in electronic applications such as printed circuit boards (PCBs). However, FR4 is not as impact-resistant as some other materials and can be prone to cracking or breaking under stress. It also has a higher dielectric constant than some other materials, which can affect signal integrity in high-frequency applications. Overall, FR4 is a reliable and widely used material in the electronics industry due to its excellent electrical properties and affordability.
Applications of FR4 and G10: Which Material is Best Suited for Which Use?
Electronics and Circuit Boards: Choosing the Right Material
FR4 and G10 are both commonly used materials for electronics and circuit boards. While both materials offer high strength, FR4 has a higher dielectric constant which makes it more suitable for applications requiring better signal performance. On the other hand, G10 is mostly preferred in moisture-rich environments since it does not absorb water easily compared to FR4. However, if weight reduction is crucial for an application then G10 would be a wise choice as it has less density than FR4 while providing comparable strength. Overall, choosing between FR4 and G10 depends on the specific requirements of the electronic or circuit board project at hand.
Mechanical Applications: FR4 or G10?
When it comes to mechanical applications, FR4 vs G10 are both excellent choices. However, the decision on which material to use ultimately depends on the specific requirements of the application. FR4 is known for its high strength and rigidity, making it a great choice for applications that require a sturdy material such as circuit boards, insulation panels, and electrical components. On the other hand, G10 is highly resistant to impact and abrasion, making it ideal for applications that require durability such as knife handles, firearm grips, and structural components in marine environments. Consider the specific needs of your mechanical application before choosing between FR4 and G10.
Aerospace and Defense Industries: Which Material Offers Superior Performance?
When it comes to the aerospace and defense industries, FR4 and G10 both have their advantages. FR4, with its high dielectric strength and flame resistance, is often used in circuit boards for satellites and other space-based technology. On the other hand, G10's superior mechanical properties make it ideal for components such as rotor blades on helicopters or armor plating on military vehicles. Ultimately, the choice between these materials will depend on specific needs of each application within these industries.
Environmental Factors to Consider When Deciding Between FR4 and G10
When considering environmental factors, FR4 is best suited for applications that require resistance to moisture and chemicals. This material is commonly used in electronic devices, such as printed circuit boards, due to its high dielectric strength and low water absorption rate. On the other hand, G10 is preferred in applications where exposure to UV radiation or extreme temperatures are a concern. This makes it an ideal choice for outdoor equipment or parts subjected to harsh environments. Ultimately, the decision between FR4 and G10 depends on the specific needs of your project and careful consideration of these environmental factors can help ensure you choose the right material for your application.
Cost Comparison: Is One Material More Economical Than the Other?
When it comes to cost, FR4 and G10 have similar price points due to their comparable manufacturing processes and material costs. However, the ultimate price for each material may differ depending on specific requirements of a project.
In general, FR4 is considered more cost-effective for high-volume productions as it is widely produced and readily available in various sizes and thicknesses. G10, on the other hand, can be more expensive due to its superior performance characteristics that make it suitable for specialized applications such as aerospace or military industries.
Overall, the decision between FR4 vs G10 ultimately depends on your specific application needs and budget constraints. It's important to carefully evaluate both materials based on your unique requirements before making a final decision.
Conclusion: Which Material Reigns Supreme in the Battle of FR4 vs G10?
Which Material Reigns Supreme in the Battle of FR4 vs G10?
There is no definitive answer to this question as there are many factors to consider when deciding which material is best suited for a particular project. However, some key factors to consider include cost, strength and durability. In the end, it is important to choose the material that best suits the needs of the project and provides the best results.
In conclusion, the battle of FR4 vs G10 is a close one, with both materials having their own unique strengths and weaknesses. FR4 is known for its high strength and flame resistance, while G10 boasts excellent electrical insulation properties and durability. The choice between the two ultimately depends on the specific application and requirements of the project. While FR4 may be more suitable for high-stress applications such as aerospace or military equipment, G10 may be better suited for electrical insulation in electronic devices. Additionally, cost may also play a factor in the decision-making process. Overall, both materials have their place in various industries and it's important to carefully consider all factors before making a decision on which material to use.
Add Comment
Business Articles
1. Lucintel Forecasts The Global Satellite Operations As A Service Market To Grow With A Cagr Of 13.3% From 2025 To 2031Author: Lucintel LLC
2. Lucintel Forecasts The Global Satellite Operation As A Service Sale Market To Grow With A Cagr Of 13.5% From 2025 To 2031
Author: Lucintel LLC
3. Ticket Booking Api
Author: RishiHassan
4. Jewelry Photo Magic: Unveiling The Tricks Of Professional Editing
Author: ukclippingpath
5. How Outsourced Accounting Services Improve Cash Flow Visibility
Author: Harsh Vardhan
6. 5 Ways To Make Homes Safer For Seniors
Author: Jack Jones
7. اكتشفي أناقتك مع متجر عبايات: دليلك للتسوق المثالي
Author: Max
8. When Is Assisted Living Needed? 5 Signs To Watch Out For
Author: Jack Jones
9. How To Document Nonconformities In Iso 22000 Audits
Author: Jane
10. Elevate Your Career Opportunities With A Supply Chain Management Certification
Author: jayesh
11. Kpi Vs. Okr: Understanding The Difference For Smarter Goal Setting
Author: TrackHr App
12. Explore The Fascinating Businesses And Landmarks Found Along Luz Church Road
Author: jayesh
13. High Temperature Superconductors Market Size & Share, Analysis 2031
Author: Andy
14. Maximize Medical Practice Profits With Expert Revenue Cycle Management In Houston
Author: patriotmedbill
15. Enhancing Quality Of Life: The Role Of Senior Living Property Management Companies
Author: Trinity Diaz