ALL >> Art >> View Article
Noble Bronze Art Or How Sculptures Are Made
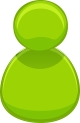
Around 3000 BC, bronze was used in prehistory. The Bronze Age, which got its name from the use of tools made of this metal at the time. It was common to make agricultural tools, but in some areas, such as Greece and Mesopotamia, people also began to create metal art, casting sculptures in bronze. The lost wax method, which is still used today, was one of them.
Bronze was primarily used in the Middle Ages in Europe for the production of weapons and tools, but it was also used for the casting of sculptures and decorations. The great revival of this metal statue design can be seen at the turn of the twentieth century in Atlanta, Georgia, USA, where it was created by great artists - sculptors, making bronze castings, such as the master of this technique and large-size sculptures.
What is bronze?
Bronze is a 9:1 copper-tin alloy that is frequently mixed with lead and zinc. It is distinguished by its durability and strength. What sets it apart from other metal alloys is its ability to reproduce the smallest details of a cast statue, which is critical for sculptors who prefer this metal. Foundry moulds are frequently ...
... made of bronze. Brass, a similarly noble copper-zinc alloy, has similar properties. It is not, however, about him.
Antoine-Louis Barye's "Lion and Serpent" inspired this extremely realistic sculpture with many details.
Basic methods of making bronze castings
Bronze was cast in a variety of ways in antiquity. Sand casting and wax casting were the two most common and widely used methods. The first was a simple technique involving fine sand forms. The second used a wax model, which was then destroyed during the sculpture casting process. The wax is very malleable, so it was simple to carve small details into it. This method was developed by the Greeks thousands of years ago. However, there was one major drawback: we lost a wax prototype during the casting process.
Later, indirect methods such as the repeated use of plaster moulds from the original wax model, which was being destroyed, were used. This technique, however, did not allow for a casting larger than approx. 1 m, due to the sculpture's high material consumption and weight. This was due to the fact that such a sculpture was completely filled inside.
However, the clever Greeks had already developed a method for casting a sculpture that was a hollow metal shell.
Lost wax casting method
The ingenious Greek "lost wax" method, which has since been improved, brought about a true revolution in foundry. It has gained widespread acceptance and is now used not only for bronze castings but also for precious metals such as gold, silver, and brass. A sculpture created using this technique is the result of replacing the model, which can be made of any material, with a replica of a chosen metal, in this case bronze.
A primary model is a project created by the artist, usually out of clay. The sculpture is then covered with a plaster mould known as a negative. When casting more complex works with many details, a flexible silicone is used, which makes the mould easier to remove from the complicated model than a rigid plaster negative. You can disassemble the mould to remove the clay model once the negative has solidified and become quite hard.
The empty form is reassembled and poured with liquid wax, which faithfully reproduces all of the sculpture's negative details. The resulting wax model, which is also hollow and has thin walls, is re-enclosed with another mold, this time made of a special moulding mass with a special tubule system attached to it. The mould is then fired, and the wax is melted as a result. As a result, the term "lost wax" was coined.
Liquid bronze is poured into the mould space left by the molten wax using pouring tubules. After cooling, the mould is broken to release the completed bronze statue. The pouring system remnants are then cut off, and any small gaps caused by incorrect metal filling of the mould are filled. Finally, the sculpture is covered with numerous preparations that bring out the natural beauty of bronze, and it is polished or patinated to achieve the artist's desired effect.
Know more about National Monuments Foundation, please visit www.thenmf.org.
Add Comment
Art Articles
1. Veterans Urge Support For Military Chaplains And The Updating Of Chaplains Hill MonumentsAuthor: Steven Dubin
2. What Defines Surrealism Art And Its Concept?
Author: Hannah
3. Bbva Launches Easter Special Promotion: "10 Days To Easter: Rise & Thrive - Your Business Reborn"
Author: Andy Kowalski
4. The Impact Of Corporate Video Production On Business Growth
Author: Jaxon Floyd
5. Who Are The Famous Still Life Artists?
Author: Hannah
6. How 3d Environment Modeling Enhances Immersion In Open-world Games
Author: Vizent
7. What Is Acrylic Still Life Painting And Its Concept?
Author: Hannah
8. Aces Gallery's Online Spring Estates Auction On Sunday, Apr 27 Is Packed With Over 500 Quality Lots
Author: Alex Fonarow
9. Tantrik In Kolkata And The Famous Tantrik Of Kamakhya
Author: Mark
10. Black Magic Specialist & Muslim Astrologer In Mumbai
Author: Mark
11. Paintings By Aiden Lassell Ripley And Michel Delacroix Top Estimates At Ahlers & Ogletree's Auction
Author: Jamia Berry
12. What Is Traditional Chinese Art And Its Concept?
Author: Hannah
13. Rare, Significant Photographic Image Of Lincoln Will Headline University Archives' Auction, Apr 23
Author: John Reznikoff
14. Which Traditional Mexican Art Is Famous?
Author: Hannah
15. What Is Traditional Japanese Art And Style?
Author: Hannah