ALL >> Service >> View Article
Efficient Tank Cleaning
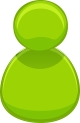
The cleaning of tanks and vessels is often an overlooked source of inefficiency in the manufacturing process. As an “unglamorous” and non-core process the true cost of cleaning is often neglected. However, with some thought significant efficiency gains can be achieved. As will be seen these efficiencies come from a combination of the 4 key elements of the cleaning process i.e. time, mechanical action, heat and chemical action. The focus of this article is on how quick wins can be achieved by improving the mechanical action element of the cleaning mix.
The balancing act – Any cleaning application has four components that contribute towards effective cleaning.
1- Time. The longer the cleaning if performed the greater the cleaning.
2- Chemicals. This is the dissolving effect of chemical cleaning fluids including water.
3- Mechanical action. This is physical action of the cleaning spray to dislodge residue.
4- Heat. Generally the hotter the cleaning fluid the better the cleaning action.
Increasing any of these 4 components will improve overall cleaning but there will be a cost associated ...
... with each. The cost of each of these elements will differ depending on application and there may well be other constraints in place. For example in food processing applications there will be limit on the types of chemical that can be applied.
The differential cost of each element is the key to efficient cleaning. Optimising the mix of elements is the process of increasing one element of the mix that has a lower cost (e.g. mechanical action) so that another element that has a higher cost (e.g. heat) can be reduced. The net cleaning power will remain the same but the cost associated with the cleaning process will be reduced.
Absolute efficiency gains Whilst overall efficiency can be gained by reconfiguring the contributions from each element it is clearly beneficial to strive for efficiencies in each element. If, for example, a cheaper method of heating can be found then this element in its own right becomes more efficient, and thus the whole process is more cost effective.
An absolute gain in one element, however, might be better utilised by reducing the contribution from another more costly element. For example, if a more efficient heating method were found then either heat could be maintained at the current level for a lower cost OR heat could be increased for the same cost. If heat is increased then perhaps time could be reduced whilst keeping overall cleaning power at the same level. If the opportunity cost saved by reducing cleaning cycle time is greater than the savings made by improved heating efficiencies then this configuration is optimum. In other words a gain in efficiency in one element is not always best deployed in that element.
Maximising gains In order to leverage hard won efficiency gains its is sensible to consider how they are best deployed and how they might be used to re-configure the cleaning elements mix.
The importance of water efficiency – Water is money. The true cost of water is often under appreciated.
– Raw utility bill cost per m3 of water
– Cost of filtering and sanitising if recycling wash off – Cost of caustics or other cleaning fluids
On top of this if we reduce the water needed to clean we can
– Lower Pump running costs (electricity) – Lower Maintenance costs – Longer lifetime for the pump. – Potentially use a smaller pump (reduced capex)
As the cost of energy and water are both increasing, and likely to continue to increase, reductions in water usage have significant financial benefits to any organisation. Further more the green / environmental benefits are seen as a moral imperative by many organisations. Future green legislation is only likely to increase the need for more efficient water usage.
The importance of time efficiency – Time is money. It may be a cliché but it’s still true. The time spent cleaning between production runs, whilst necessary, still represents downtime. The opportunity cost associated with this downtime will vary greatly depending on the application, but in almost all cases a reduction on cleaning cycle time will have a direct financial benefit.
Chemical and heat efficiency – Generally there will be limitations on each of these elements. Perhaps more importantly both elements have very rapidly diminishing returns after a certain point. For example, the cost associated with raising cleaning temperatures from 60o – 70o is unlikely to be worth it for most applications. It is likely that chemical and heat action will be the elements that are reduced in any efficiency drive. The typical scenario is that improved mechanical action will result in the reduction of chemical usage or lowering the temperature of cleaning.
When performing these savings calculations it is important to remember the true cost of heat and chemicals. Heat is relatively simple to calculate as it is essentially an energy cost but consideration should be given to maintenance spares and overall capex vs working life of the heating system. The cost of using chemicals should obviously include the raw cost of the chemical but also the cost of disposal of spent chemicals and recycling plant costs (if used).
The Quick Win – Often the simplest absolute efficiency gains can be found by improving the mechanical action element of the mix. These gains can then be deployed to reduce other elements of the mix, if this is appropriate.
The importance of spray nozzle selection
For any impact cleaning process water serves two purposes. Firstly it acts to dissolve residue – this is part of the chemical element of cleaning mentioned above. More importantly, however, water is the mechanism by which the mechanical action element is delivered. The efficiency of a water spray for delivering mechanical energy for cleaning will be greatly affected by the nature of the spray and thus the nozzle used.
Improving the efficiency of mechanical action – Mechanical action is essentially the process of transferring energy from a pump to the surface to be cleaned via water. As with all energy transfer systems efficiency is less than 100%. Much energy is wasted but by reducing this waste through improved nozzle selection we can significantly improve the efficiency of the tank washing system. If this is achieved then we can reduce the amount of energy/water used and achieve the same level of mechanical action.
Effective nozzle selection will obviously not directly affect pipe friction losses but it will affect losses of energy through fluid atomisation and turbulent flow.
Article Source: https://EzineArticles.com/expert/Ivan_Zytynski/1289667
Add Comment
Service Articles
1. Safe From The Start: Hypoallergenic And Natural Baby Care Products For Delicate SkinAuthor: Beba Canada
2. Shopify Development Agency In India
Author: Diksha
3. Kaal Sarp Yoga Puja At Trimbakeshwar: Benefits, Process & Cost
Author: Pandit Laxmi Narayan Guruji
4. Why Micro-moments Are The New Battleground For Digital Marketers
Author: OneData Software Solutions
5. How To Choose The Right Spray Foam Removal Expert In The Uk!
Author: Spray Foam Removal
6. The Importance Of Water Damage Mitigation In Marietta
Author: americasrestorationservices
7. What To Do When Your Garage Door Opener Stops Working
Author: ABC Garage Doors & Repair
8. Why Brands That Educate (not Sell) Win In The Long Run
Author: OneData Software Solutions
9. Tips To Capture Natural Moments In Your Graduation Photoshoot
Author: Magicdow Photography
10. Leveraging Scraped Bigbasket Data To Build A Dynamic Price Comparison Platform
Author: Retail Scrape
11. Home Movers And Packers: The Stress-free Solution For Your Move
Author: Hayder Gilani
12. Complete Guide To Trimbakeshwar Pooja, Costs & Ritual Details
Author: Pooja Trimbakeshwar
13. Smart Teams, Smarter Tech: How Remote Staffing Is Reshaping The Future Of Work - Crest Property Solutions
Author: meetjoshi1911
14. A Complete Guide To Business Bridging Loans In The Uk
Author: Vikram Parekh
15. Cheapest Smm Panel To Boost Your Social Media Growth Fast
Author: cheapest smm panel