ALL >> General >> View Article
Pcb Surface Coating Functions And Selecting Principles
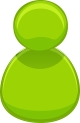
Copper has been selected as conductive material by PCB (Printed Circuit Board) owing to its excellent conductivity and physical performance. However, copper surface tends to be oxidized when exposed to air with a solid and thin oxide layer caused on the surface, which mostly leads defects to occur to solder joints and thereafter will reduce product’s reliability and shorten shelf life. Therefore, it’s of quite necessity to implement protective measures to stop copper surface from being oxidized, which is the original reason for the advent of surface coating that should be heat-resistant and solderable. Up to now, PCB surface coatings have rapidly developed with numerous classifications generated and how to select a proper type still matters. Thus, this article will discuss PCB surface coating functions, classifications and introduce some selecting principles.
What is PCB Surface Coating?
•Significance of PCB Surface Coating
To stop the copper surface of pad on PCB from being oxidized and polluted prior to solderability, it’s of dramatic significance to apply surface coating (also called surface finish) ...
... on copper to carry out protective function.
Copper features the second best conductivity and physical properties (the top best is silver) plus its rich storage and low cost, so copper has been selected as conducting material for PCBs. Nevertheless, as a type of active metal, copper becomes oxidized so easily that oxide layer (copper oxide or cuprous oxide) tends to be generated on the surface, causing defects on solder joints that will reduce product’s reliability and shorten shelf life.
Based on statistics, 70% of defects on PCB boards derive from solder joints due to the following two reasons:
Reason#1: The pollution and oxidization occurring to pad on PCB tend to lead to incomplete soldering and cold solder joints.
Reason#2: Diffusion layer tends to be generated due to diffusion between silver and copper while inter -metallic compound (IMC) tends to be generated between tin and copper, leading interface to be loose and fragile.
Therefore, the copper surface ready to be soldered should implement protective layer with solderability or isolating function so that defects can be eased or avoided.
•Requirement on PCB Surface Coating
The surface coating on PCB pad should be compatible with the following requirement:
a. Heat Resistance
Under the high temperature during soldering, surface finish should be also capable of stopping PCB pad surface from being oxidized and allowing solder to have direct contact with copper.
The heat resistance of organic surface coating refers to the performance of melting point and thermal decomposition temperature. The melting point of surface coating should be close to or lower than that of tin while its thermal decomposition temperature should be far higher than the melting point and soldering temperature of solder. As a result, oxidization won’t take place on copper surface during soldering.
b. Coverability
Basically, PCB surface finish is able to be completely covered on the surface of copper pad without being oxidized or polluted before and during soldering. It won’t drift away, be decomposed or float on the surface of solder joints. Thus, to make sure the melting solder can be completely soldered onto pad, the surface tension of the melting surface coating should be small and the decomposition temperature should be high so that high coverability can be guaranteed before and during soldering.
c. Residue
The residue here refers to the residue left on the surface of pad or solder joints after the implementation of soldering. Generally speaking, the residue is hazardous and should be eliminated, which is why cleaning measures are usually made after soldering.
d. Corrosivity
The corrosivity here refers to the corrosion caused by residual solder to circuit board surface after soldering such as PCB substrate material or metallic layer.
e. Environmental Concerns
Nowadays, environmental concerns are arousing increasingly high attention from the industry. When it comes to surface coating on PCB, the effluent during coating generation and after cleaning and soldering should be easy to be disposed and environment friendly.
How is PCB Surface Coating Classified?
•Based on Manufacturing Technology
Based on manufacturing technology, PCB surface finish can be classified into surface coating and metal coating.
a. Surface Coating
Surface coating refers to the process of adding a thin coating that is both heat-resistant and solderable onto the copper surface in a physical method. The leading property of surface coating lies in the fact that a pure copper surface can be provided to solder for soldering during soldering process. The surface finish, like HASL (Hot Air Solderability Level) or (Organic Solderability Preservative), belongs to this classification.
b. Metal Coating
Metal coating refers to the process that a heat-resistant and solderable metal coating is generated on pure copper surface of pad on PCB in the way of electroless plating and electroplating, such as ENIG (Electroless Nickel Immersion Gold), ENEPIG (Electroless Nickel Electroless Palladium Immersion Gold), Immersion Gold etc.
•Based on Application Effect
Based on application effects, surface finish can be classified into three categories: soldering flux soldered on the coating on isolating layer, soldering flux soldered on the metal coating on diffusion layer and soldering flux soldered on the isolating layer of the metal coating.
Category#1: Soldering flux is soldered on the coating on the isolating layer.
The leading property of this type of surface coating is that the melting solder will drift on the surface of solder after leaving copper during high-temperature soldering. However, IMC will be generated in the interface of soldering joint, which will increase the possibility of defects.
Category#2: Soldering flux is soldered on the metal coating on diffusion layer.
The advent of this type of technology aims to eliminate IMC but it features obvious disadvantages. On one hand, it tends to arouse diffusion; on the other hand, it tends to cause board to suffer from brittleness, which thereafter arouses defects to occur to circuit.
Category#3: Soldering flux is soldered on the isolating layer of the metal coating.
The leading merit of this type of technology is that solder is soldered on the surface of the isolating layer of metal coating instead of direct on copper surface. Therefore, stable IMC won’t be generated at the interface and diffusion won’t be caused between metals.
How to Select PCB Surface Coating?
Great attention has to be paid to PCB surface coating since it’s closely associated with PCB solderability, reliability and shelf life. It should be particularly selected based on application condition and fields.
Owing to different properties and application effect of surface coatings, it should be picked up in accordance with application requirement and specific application fields during PCB manufacturing process and manufacturing complexity and cost cannot be the mainly judging basis.
Generally speaking, in terms of electronic products served for civil industry or ordinary industry, the surface coating whose soldering flux is soldered without isolating layer should be selected, such as HASL, OSP etc.
In terms of the applications striving for high reliability and long shelf life, like medical care, transportation, military, aerospace etc., however, surface coating should be selected whose soldering flux is soldered on the isolating layer, such as ENIG and ENEPIG.
Add Comment
General Articles
1. Choosing The Right Materials For Cnc Plastic Machining: A Comprehensive GuideAuthor: Mike Brogan
2. Vidmate App Download Apk New Version
Author: VIDMATE APP
3. Seal Your Love With A Promise & Embrace It With A Hug: Thoughtful Gifts For Two Special Days
Author: Ajay
4. Ai Website Builder Vs. Free Html Templates
Author: Andrew
5. Crypto_ Advertising Solution Crypto_currency Advertising
Author: cryptocurrencybizopps
6. Best Kitchen Companies In Haywards Heath For Your Dream Kitchen
Author: alex
7. 3bhk Property In Lucknow: The Perfect Mix Of Comfort And Luxury
Author: Star Estate
8. Dermatologist-approved Tips For Managing Skin Allergies
Author: Mayra Singh
9. What Is An Insider Threat? How To Prevent It?
Author: Reinfosec
10. Why Are Google Ads Essential For Modern Dental Marketing?
Author: PSM
11. Luxury Hotel Market Analysis: Emerging Opportunities Worldwide
Author: mmr123
12. Master Java Programming With Infograins Tcs
Author: Infograins tcs
13. Comment Profiter De 50% De Réduction Sur Vos Prix De Moule D'injection ?
Author: MOULDING INJECTION
14. Why Choose Listany For Website Development? Scalable, Secure & Custom Solutions For Your Business
Author: Listany
15. How Udyog Erp Enhances Productivity In The Manufacturing Sector
Author: Udyog