ALL >> Business >> View Article
What Are The 16 Major Losses In Total Productive Maintenance?
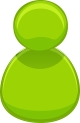
The 16 Major Losses are a set of types in Total Productive Maintenance that includes all types of waste in a production system. In manufacturing, these types help to identify, classify, and ultimately remove wasteful practices. All Losses are separated into three groups: Availability Losses, Performance Losses, and Resource Consumption Losses.
Availability Losses:
It is expressed in time and relates to the availability of machines. These losses play a vast part in lowering a plant’s overall equipment effectiveness.
Breakdown loss: Breakdown loss happens when a machine
• fails and is incapable to be operated.
• runs at a lower-than-normal rate.
• runs with infrequent stoppages.
• wants a part replacement to function correctly.
• wants repairs that last for more than five or ten minutes.
There is a mutual misconception that it’s incredible to attain zero failures; failures are certainly not unavoidable. With the correct mindset and strategy, zero failures can be accomplished. Best practices here are to contain production personnel in the maintenance procedure, ...
... focus more on failure analysis, and upgrade maintenance systems.
Planned maintenance loss: When equipment is purposely shut down for an inspection or maintenance, this falls under planned maintenance loss. Although essential, this type of loss still affects the accessibility of machines, and it should therefore take as short a time as probable.
Setup & adjustment loss: This loss relays to changeovers, either between tools. Setup loss is the time it takes between using the old and new tool. Adjustment loss, in turn, is the time it receipts to tweak the machine until it’s execution its new function correctly. Single minute exchange of dies can be used to keep this loss to a least.
Cutting blade change loss: The time it takes to replace a worn-out, broken, or useless cutting tool.
Startup loss: Comparable to adjustment loss, startup loss happens when bringing a piece of equipment into a best operating state after a shutdown.
Minor stoppage loss: Minor stoppages can last from only a few seconds to some minutes. This loss is determined and regular, and oftentimes hard to detect. There can be different causes for this loss: defective sensors, maladjusted machine settings, compressed materials, etc. A best practice to decrease this loss is to install equipment that’s accomplished of detecting and registering small stoppages.
Speed loss: Speed loss couriers the lost time that’s sustained due to a machine running slower than its standard speed. Speed loss can also be useful to cases where a machine is running at a slower speed than industry standards.
Defect and rework: When a machine are producing a defective product and spending time to rework the defective product that is called defect and rework loss. Occasional defects are not the large problem here, as those are often easily fixed; the issue comes with chronic defects, as the reason of these is both hard to detect and hard to fix.
Performance Losses:
Performance losses is expressed in both time and money, and chiefly relates to losses that are connected to the human workforce.
Management loss: Insufficient management can be an important reason of production halting.
Operating motion loss: Operating motion losses make out of pointless or superfluous operator movement, frequently caused by a sub-optimal layout of the shop floor.
Line organization loss: Line organization loss happens when the speed of the different steps on a line is unstable, causing certain operators to be idle. This is not essentially an equipment-related fault, as there’s also a human factor here. Also, a bottleneck analysis or a line balancing analysis can be very operative in bringing about a balanced, steadily flowing line.
Distribution loss: This loss applies to everything associated to the delivery of products to a factory. The unloading of products is a point where this loss can happen. Though automation can lead to a decrease in unloading time, unloading is generally still done by humans.
Measurement & Adjustment loss: If the quality of products is constantly sub-optimal and the root cause can’t be found, the significance is often an unnecessary number of adjustments to machine settings. This continual inspecting and adjusting can lead to an important waste of time.
Resource Consumption Losses:
Yield loss: Yield loss couriers the loss that happens when a part of the total production output has to be waste because of flaws.
Energy loss: Energy loss includes waste due to the direct material loss of energy and its incompetent use. Energy already forms a big part of manufacturing costs, so decreasing energy loss as much as possible is a high priority for manufacturers.
Die & tool loss: The looses due to repair and replacement of any spare, die, tool, etc. spare get damaged after the service life so it will need to change it.
Total Productive Maintenance management training will validate the goals, methods and advantages of TPM, with maximizing the efficiency of production equipment and decreasing breakdowns. Total Productive Maintenance Management Training deliver detailed information about what is TPM, how to develop Total Productive Maintenance System, how a lean TPM training tool is concerned with maximizing the competence of production machinery, and more.
Add Comment
Business Articles
1. Lucintel Forecasts The Glass Fiber In The Global Marine Market To Grow With A Cagr Of 3.7% From 2024 To 2030Author: Lucintel LLC
2. Lucintel Forecasts The Glass Fiber In The Global E&e Market To Grow With A Cagr Of 3.9% From 2024 To 2030
Author: Lucintel LLC
3. Lucintel Forecasts The Global Frp Pole In Telecommunication Market To Grow With A Cagr Of 6.5% From 2024 To 2030
Author: Lucintel LLC
4. Lucintel Forecasts The Global Frp Pole In Power Transmission & Distribution Market To Grow With A Cagr Of 6% From 2024 To 2030
Author: Lucintel LLC
5. Lucintel Forecasts The Global Frp Pipe In Oil And Gas Market To Grow With A Cagr Of 5.1% From 2024 To 2030
Author: Lucintel LLC
6. Lucintel Forecasts The Global Frp Pipe In Chemical Market To Grow With A Cagr Of 3.6% From 2024 To 2030
Author: Lucintel LLC
7. Adopt A Modern Telecom Commission Management System To Fix Revenue Leakages
Author: Kevin
8. Quality Steel Pipes And Tubes With Commitment And Trusted Service
Author: CONTENT EDITOR FOR SAMPHIRE IT SOLUTIONS PVT LTD
9. Lucintel Forecasts The Global Foam Core For The Construction Market To Grow With A Cagr Of 3.7% From 2024 To 2030
Author: Lucintel LLC
10. How Important Is Mutual Fund?
Author: Sagar Shah
11. What Do You Need To Know About Customize Your Own Clothes
Author: Guangzhou Beianji Clothing
12. Detailed Tips To Choose Quality Cabinets And Joinery Melbourne
Author: William Harvey
13. Lucintel Forecasts The Global Foam Core For The Transportation Market To Grow With A Cagr Of 5.4% From 2024 To 2030
Author: Lucintel LLC
14. Silicone Sealing Foam Cord: The Valuable Option For You
Author: Dongguan Senma New Materials Technology Co., Ltd
15. How Investment Banking Companies And Credit Solutions Elevate Wealth Management
Author: Drishti Desai