ALL >> Business >> View Article
Steps To Implement Poka Yoke Management
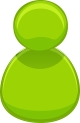
In the early 1960s, Shingo observed that workers were forgetting to insert springs in a simple on/off switch. This one small error resulted in faulty parts being manufactured and shipped. From his observations, Shingo learned that Sometimes people forget to do things.
Knowing that these simple human mistakes were the root cause of the issue, Shingo started working on ways to enhance the procedures and to make it an idiot-proof. After a worker complained that the term was abusive, he changed it to poka-yoke, which shifts the attention from the worker to the procedure. By redesigning the procedures so that the operation could not proceed until the worker had injected the spring into the switch, fewer human mistakes were made and higher quality products were shipped.
How to implement poka-yoke?
Implementing poka-yoke should be easy, low-cost, and associated with current procedures. Organization should see instant benefits and measurable developments in quality and production. Organization can implement poka-yoke by using the steps described below.
Identify the issue: Remember that humans make mistakes. One ...
... or two mistakes are to be predictable. A sequence of mistakes specifies that there is an issue that wants to be addressed. That issue may be with the employee or with a fault in a machine. Essential to observe the procedures to see if it can identify where the issue is happening. Enlist the help of others to determine whether the mistake is human or mechanical.
Find the root cause: After identify the issue, organization will need to determine what is the most likely reason of that issue. Organization may need to consider using the 5 Whys, another quality control technique established in Japan, it helps to find the root cause. By asking and answering five “why” questions, organization will dig down to find the root cause of the issue.
Determine which type of poka-yoke to use: If you can easily stop mistakes from happening, install a control poka-yoke that stops the procedures from remaining until a crucial step is accomplished. If the shape of a component confirms that it can only be implanted in the correct way. If you can’t stop a mistake, install a warning poka-yoke that alerts the operator that attention is required before the procedure can continue. These warnings can contain colors, flashing lights, buzzers, or any type of alerts that tell the employee that something wants to happen before the procedure continues.
Determine the most suitable poka-yoke method to use: There are three poka-yoke methodologies organization can choose from.
• Contact: This method uses shape, size, or other physical features to identify mistakes.
• Constant number: With this method, mistakes are triggered if a specific number of actions are not made. The operator is warned if the wrong number of moves are made.
• Sequence: This method confirms that the correct sequence of events is followed before a procedure can continue.
Test poka-yoke system: Before completely implement a poka-yoke, organization need to assure that it will work. Organization must test it to see if the mistakes is prohibited and to make sure that the fix does not slow down the procedure.
Train employees: Even the simplest poka-yoke can’t be successfully implemented until employees are trained how to do it. Poka Yoke Management Training helps with employee acceptance of the new procedure, especially if they can see that the fix makes their job easier to do. Add new poka-yoke to SOP guide to help employees understand what is expected of them.
Review performance and measure success: Observe the procedure again and measure success. Begin looking for other mistakes that may be impeding production and look for ways to constantly improve.
Add Comment
Business Articles
1. Lucintel Forecasts The Glass Fiber In The Global Marine Market To Grow With A Cagr Of 3.7% From 2024 To 2030Author: Lucintel LLC
2. Lucintel Forecasts The Glass Fiber In The Global E&e Market To Grow With A Cagr Of 3.9% From 2024 To 2030
Author: Lucintel LLC
3. Lucintel Forecasts The Global Frp Pole In Telecommunication Market To Grow With A Cagr Of 6.5% From 2024 To 2030
Author: Lucintel LLC
4. Lucintel Forecasts The Global Frp Pole In Power Transmission & Distribution Market To Grow With A Cagr Of 6% From 2024 To 2030
Author: Lucintel LLC
5. Lucintel Forecasts The Global Frp Pipe In Oil And Gas Market To Grow With A Cagr Of 5.1% From 2024 To 2030
Author: Lucintel LLC
6. Lucintel Forecasts The Global Frp Pipe In Chemical Market To Grow With A Cagr Of 3.6% From 2024 To 2030
Author: Lucintel LLC
7. Adopt A Modern Telecom Commission Management System To Fix Revenue Leakages
Author: Kevin
8. Quality Steel Pipes And Tubes With Commitment And Trusted Service
Author: CONTENT EDITOR FOR SAMPHIRE IT SOLUTIONS PVT LTD
9. Lucintel Forecasts The Global Foam Core For The Construction Market To Grow With A Cagr Of 3.7% From 2024 To 2030
Author: Lucintel LLC
10. How Important Is Mutual Fund?
Author: Sagar Shah
11. What Do You Need To Know About Customize Your Own Clothes
Author: Guangzhou Beianji Clothing
12. Detailed Tips To Choose Quality Cabinets And Joinery Melbourne
Author: William Harvey
13. Lucintel Forecasts The Global Foam Core For The Transportation Market To Grow With A Cagr Of 5.4% From 2024 To 2030
Author: Lucintel LLC
14. Silicone Sealing Foam Cord: The Valuable Option For You
Author: Dongguan Senma New Materials Technology Co., Ltd
15. How Investment Banking Companies And Credit Solutions Elevate Wealth Management
Author: Drishti Desai