ALL >> Business >> View Article
Understand The Rules Of Kanban Implementation
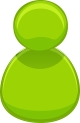
Managing business procedures using Kanban can only be operative if it’s executed appropriately. An operative Kanban system is more than just projecting post-it’s on a board. It is a mindset – a move towards efficiency, organization, and removing waste through a stable flow of work. A strong level of trust between leadership and staff is significant to create a stable flow of work. But in order to accomplish a high level of trust within the organization, expectations must be set. Need a guide so everyone in the team knows how to do work accurately. The rules of Kanban will guide teams towards a successful and effective Kanban system implementation. Let’s explore the rules of Kanban and how they both apply to traditional production and knowledge work.
Never Permit Defective Products: Ambitious procedures shouldn’t permit products that do not meet the standards and level of quality expected. Defective products should be removed from the production line and be distributed with outside of it. This confirms that only quality products go to consumers, reduces waste, and decreases consumer complaints. Policies help confirm ...
... that the desired level of quality is sustained at every step. This is honestly straightforward for tangible goods production. But the same applies to knowledge work.
Take Only What’s Required: A successful Kanban implementation needs those downstream procedures only pull what they want. This stops overproduction, drops costs, and makes operations more reflective of the demands of the market. Applying this rule as one of the six rules of Kanban is honestly straightforward for manufacturing procedures. For knowledge work, this is only working on consumer orders when required.
Produce the Precise Quantity Essential: Taking only what need to lead to only producing the exact quantity of products that are essential. If overproduce, you’re stocking up on more costs. These contain opportunity costs from the resources and money spent to build the item, storage costs, and transportation costs. Also run the risk of having the product become obsolete.
Having a Minimum Viable Product mindset helps in this area. If a consumer wants to have the facility to download a report from app, don’t need to throw in a print feature as well. Focus on the minimum necessities. Build the products as the market demands or as your product direction leads to it.
Level the Production: In order to accomplish a stable flow of work, all units within the Kanban system should only produce the number of items based on the capacity of its limiting supplier. Explore Heijunka, another Lean concept, to see how you can level production activities. In knowledge work, levelling by measure the capacity of every step in Kanban. When spot a bottleneck, you can lessen the burden by augmenting resources or setting your work-in-progress limit based on limiting supplier.
Fine-tune the Process Optimization: Once the team has prepared its Kanban implementation, the next goal should be to utilize their Kanban system to surface pain points and development opportunities. This would need a closer look at how work is flowing and measuring their performance.
Kanban system of measurement such as lead time, cycle time, and throughput will help teams get a measurable and objective assessment of their work. A cumulative flow diagram will help teams spot bottlenecks. Many Kanban management training available online with certification may have these metrics and reports built-in. Teams must use the tools available for them to make informed decisions on how to optimize their procedure. They must look for activities that produce waste. This can be in the form of delays, defects, rework, and unnecessary handoffs. Regular team retrospectives where teams discuss their experiences, pain points, and development suggestions and then formulate solutions to address them are significant to fine-tuning production. As inefficiencies reduction, work-in-progress items also reduction because the procedure is leaner.
Stabilize and Rationalize the Procedure: When you confirm quality, level production, and optimize procedure, process gains stability. A stable procedure allows standardization. Document your process so that there is a mutual shared understanding of how team should operate. Any deviations to the procedure standards should be managed by policies.
Having standards explicit delivers a strong foundation for team to operate with certainty and constancy. Policies and standards can evolve through time as continue to fine-tune procedure. Have regular team reviews to update process and make Kanban system more robust.
Add Comment
Business Articles
1. Lucintel Forecasts The Glass Fiber In The Global Marine Market To Grow With A Cagr Of 3.7% From 2024 To 2030Author: Lucintel LLC
2. Lucintel Forecasts The Glass Fiber In The Global E&e Market To Grow With A Cagr Of 3.9% From 2024 To 2030
Author: Lucintel LLC
3. Lucintel Forecasts The Global Frp Pole In Telecommunication Market To Grow With A Cagr Of 6.5% From 2024 To 2030
Author: Lucintel LLC
4. Lucintel Forecasts The Global Frp Pole In Power Transmission & Distribution Market To Grow With A Cagr Of 6% From 2024 To 2030
Author: Lucintel LLC
5. Lucintel Forecasts The Global Frp Pipe In Oil And Gas Market To Grow With A Cagr Of 5.1% From 2024 To 2030
Author: Lucintel LLC
6. Lucintel Forecasts The Global Frp Pipe In Chemical Market To Grow With A Cagr Of 3.6% From 2024 To 2030
Author: Lucintel LLC
7. Adopt A Modern Telecom Commission Management System To Fix Revenue Leakages
Author: Kevin
8. Quality Steel Pipes And Tubes With Commitment And Trusted Service
Author: CONTENT EDITOR FOR SAMPHIRE IT SOLUTIONS PVT LTD
9. Lucintel Forecasts The Global Foam Core For The Construction Market To Grow With A Cagr Of 3.7% From 2024 To 2030
Author: Lucintel LLC
10. How Important Is Mutual Fund?
Author: Sagar Shah
11. What Do You Need To Know About Customize Your Own Clothes
Author: Guangzhou Beianji Clothing
12. Detailed Tips To Choose Quality Cabinets And Joinery Melbourne
Author: William Harvey
13. Lucintel Forecasts The Global Foam Core For The Transportation Market To Grow With A Cagr Of 5.4% From 2024 To 2030
Author: Lucintel LLC
14. Silicone Sealing Foam Cord: The Valuable Option For You
Author: Dongguan Senma New Materials Technology Co., Ltd
15. How Investment Banking Companies And Credit Solutions Elevate Wealth Management
Author: Drishti Desai