ALL >> Business >> View Article
How To Implement A Total Productive Maintenance Program?
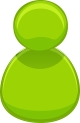
Total productive maintenance is a complete method to preserving equipment. The aim is to enhance production by being proactive and preventive. This means that equipment will be less probable to experience failures, stoppages, running slow or flaws. Instead of replying to a situation, total productive maintenance aspects to deal with problems before they happen. Organizations do this by growing the role of operators and giving them what they want to maintain equipment. Total productive maintenance programs open up a shared relationship for the responsibility of the equipment. Operators, as well as plant workers, are all complicated in maintaining equipment. Imagine, such a method can boost productivity, rise uptime, decrease cycle time and severely decrease equipment defects.
Implementation Steps:
Announce the Total productive maintenance program: Announce intention to implement a Total productive maintenance program and launch a training initiative. Obviously communicate the program’s objectives, benefits, and roles within it.
Classify the Target Area: To avoid overwhelm, focus on one piece of equipment ...
... at a time. The first equipment for which implement the principles of TPM can be either:
• The easiest to enhance.
• The one that chiefs to regular bottlenecks.
• The one has the most issues.
The equipment that is the easiest to enhance will give rapid results. If don’t have a lot of experience with Total productive maintenance, it can be a brilliant starting point. This is also the lowest risk method. Fixing equipment that frequently creates bottlenecks will rapidly enhance productivity. However, if it’s serious, this can be a high-risk plan. It is appropriate for organizations that have experience with Total productive maintenance. Enhancing the most difficult pieces of equipment is frequently hard, but if it’s successful, it will assurance wide acceptance from production personnel. Again, organizations that already have experience with Total Productive Maintenance are well equipped for this.
Bring Equipment to Its Best Condition: This step contains restoring the equipment to its major operational capacity by applying the 5S principles:
• Eliminate all unnecessary tools from the work area.
• Establish all tools and parts that use.
• Methodically clean both the equipment and the working area.
• Take pictures of the current condition of the equipment.
• Perform audits to assure the equipment is maintained in its best condition.
Implement Autonomous Maintenance: Deliver necessary training to machine operators, so that they can accomplish autonomous routine maintenance. Maintenance workers may essential to assist with Total productive maintenance management training and supervision. Open communication between machine operators and maintenance technicians is crucial for the success of total productive maintenance.
Track and Measure Overall Equipment Effectiveness over Time: Track Overall Equipment Effectiveness for this precise piece of equipment and comparison it over time. Classify positive and negative trends and make further improvements as essential. Unexpected stop time is the most mutual reason for drops in OEE. Make sure address the reasons and perform root reason analysis for each incidence. Assemble data over at least a few weeks using a Computerized Maintenance Management System to be able to track trends and proactively remediate problems.
Reduce Losses: Goal to reduce losses, starting with the most significant ones. with the Overall Equipment Effectiveness data, able to analyze the most general reasons for losses. An enthusiastic team wants to identify symptoms and propose solutions. Implement the solutions through scheduled maintenance time. Analyze results once production restarts. Continue tracking Overall Equipment Effectiveness to assess long-term effectiveness.
Introduce Proactive Maintenance: Finally, schedule planned maintenance tasks. Classify asset components prone to wear, stress, and failure. Define and implement maintenance intervals according to these requirements. Create a work order procedure for planned maintenance tasks.
Add Comment
Business Articles
1. Lucintel Forecasts The Glass Fiber In The Global Marine Market To Grow With A Cagr Of 3.7% From 2024 To 2030Author: Lucintel LLC
2. Lucintel Forecasts The Glass Fiber In The Global E&e Market To Grow With A Cagr Of 3.9% From 2024 To 2030
Author: Lucintel LLC
3. Lucintel Forecasts The Global Frp Pole In Telecommunication Market To Grow With A Cagr Of 6.5% From 2024 To 2030
Author: Lucintel LLC
4. Lucintel Forecasts The Global Frp Pole In Power Transmission & Distribution Market To Grow With A Cagr Of 6% From 2024 To 2030
Author: Lucintel LLC
5. Lucintel Forecasts The Global Frp Pipe In Oil And Gas Market To Grow With A Cagr Of 5.1% From 2024 To 2030
Author: Lucintel LLC
6. Lucintel Forecasts The Global Frp Pipe In Chemical Market To Grow With A Cagr Of 3.6% From 2024 To 2030
Author: Lucintel LLC
7. Adopt A Modern Telecom Commission Management System To Fix Revenue Leakages
Author: Kevin
8. Quality Steel Pipes And Tubes With Commitment And Trusted Service
Author: CONTENT EDITOR FOR SAMPHIRE IT SOLUTIONS PVT LTD
9. Lucintel Forecasts The Global Foam Core For The Construction Market To Grow With A Cagr Of 3.7% From 2024 To 2030
Author: Lucintel LLC
10. How Important Is Mutual Fund?
Author: Sagar Shah
11. What Do You Need To Know About Customize Your Own Clothes
Author: Guangzhou Beianji Clothing
12. Detailed Tips To Choose Quality Cabinets And Joinery Melbourne
Author: William Harvey
13. Lucintel Forecasts The Global Foam Core For The Transportation Market To Grow With A Cagr Of 5.4% From 2024 To 2030
Author: Lucintel LLC
14. Silicone Sealing Foam Cord: The Valuable Option For You
Author: Dongguan Senma New Materials Technology Co., Ltd
15. How Investment Banking Companies And Credit Solutions Elevate Wealth Management
Author: Drishti Desai