ALL >> Business >> View Article
Understand The 8 Pillars Of Total Productive Maintenance
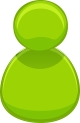
Total productive maintenance is a full method to maintaining equipment. The purpose is to enhance production by being proactive and preventative. This means that equipment will be less likely to experience failures, stoppages, running slow, defects. Instead of responding to a condition, total productive maintenance looks to deal with problems before they arise. Organizations do this by increasing the role of operators and giving them what they want to maintain their equipment. TPM programs open up a shared relationship for the duty of the equipment. Operators, as well as plant workers, are all complex in maintaining equipment. Imagine, such an approach can boost productivity, rise uptime, decrease cycle time and drastically decrease equipment defects.
The 8 Pillars of Total Productive Maintenance:
Including lean manufacturing techniques, TPM is made on eight pillars based on the 5-S system. The eight pillars of total productive maintenance focus on proactive and preventive techniques helps to enhance equipment reliability.
Autonomous maintenance: Confirming operators are fully trained on routine maintenance ...
... like cleaning, lubricating and inspecting, as well as placing that responsibility only in their hands. This gives machine operators a feeling of ownership of their equipment and rises their knowledge of the particular piece of equipment. It also assurances the machinery is always clean and lubricated, helps identify problems before they become failures, and frees up maintenance staff for higher-level tasks. Applying autonomous maintenance contains cleaning the machine to a "baseline" standard that the operator must sustain. This contains training the operator on technical skills for conducting a routine inspection based on the machine's manual. Once trained, the operator sets own autonomous inspection schedule. Standardization confirms everybody follows the similar procedures.
Focused improvement: In manufacturing, kaizen needs improving functions and procedures constantly. Focused improvement looks at the procedure as a whole and brainstorms idea for how to enhance it. Accomplishment small teams in the mindset of proactively working together to implement regular, incremental developments to processes pertaining to equipment operation is significant for TPM. Spreading team members permits for the identification of recurring errors through cross-functional brainstorming. It also combines input from across the organization so teams can see how procedures affect different departments. In addition, focused improvement rises competence by decreasing product defects and the number of procedures while enhancing safety by analyzing the risks of each individual action. Lastly, focused improvement confirms improvements are standardized, making them repeatable and maintainable.
Planned maintenance: It involves studying metrics like failure rates and historical downtime and then scheduling maintenance tasks based around these measured failure rates. In other words, since there is a precise time to perform maintenance on equipment, schedule maintenance around the time when equipment is idle, rarely interrupting production. Also, planned maintenance permits for inventory build-up for when scheduled maintenance arises. when each piece of equipment is scheduled for maintenance activities, having this inventory build-up confirms any reduction in production due to maintenance is mitigated.
Taking this proactive approach greatly decreases the amount of unplanned downtime by permitting for most maintenance to be planned for times when machinery is not scheduled for production. It also let’s plan inventory more thoroughly by giving the capability to well control parts that are prone to wear and failure.
Quality maintenance: All the maintenance planning in the world is all for nothing if the quality of the maintenance being performed is inadequate. The quality maintenance pillar focuses on working design error detection and prevention into the production procedure. It does this by using root cause analysis to identify and eliminate recurring sources of flaws. By detecting the source of errors, procedures become more reliable, producing products with the right specifications the first time. Perhaps the major advantage of quality maintenance is it stops defected products from moving down the line, which could lead to a lot of reworks. With targeted quality maintenance, quality problems are addressed, and permanent countermeasures are put in place, minimizing defects and stoppage related to defected products.
Early equipment management: It takes the practical knowledge and overall understanding of manufacturing equipment developed through total productive maintenance and uses it to enhance the design of new equipment. Designing equipment with the input of people who use it maximum permits suppliers to enhance maintainability and the way in which the machine operates in future designs. When discussing the design of equipment, it's significant to talk about things like the ease of cleaning and lubrication, accessibility of parts, ergonomically placing controls in a way that is comfortable for the operator, how changeovers happen and safety features. Taking this approach rises efficiency even more because new equipment already meets the desired specifications and has rarer start-up problems, therefore accomplishment planned performance levels faster.
Training and education: It apply to operators, managers and maintenance personnel. They are proposed to confirm everybody is on the same page with the TPM process and to address any knowledge gaps so TPM goals are achievable. This is where operators learn skills to proactively maintain equipment and classify emerging issues. The maintenance team learns how to implement a proactive and preventive maintenance schedule, and managers become well-versed in TPM principles, employee growth and coaching.
Safety, health and environment: Sustaining a safe working environment means employees can perform their tasks in a safe place without health hazards. It's significant to produce an environment that makes production more effectual, but it should not be at the risk of an employee's safety and health. To accomplish this, any solutions announced in the TPM process should always consider safety, health and the environment. Apart from the apparent advantages, when employees come to work in a safe environment each day, their attitude tends to be well, since they don't have to worry about this important aspect.
TPM in administration: TPM should look outside the plant floor by addressing and removing areas of waste in administrative functions. This means supporting production by enhancing things like order processing, procurement and scheduling. Administrative functions are frequently the first step in the entire manufacturing process, so it's significant they are streamlined and waste-free.
Total Productive Maintenance training includes information about TPM, and how to develop total productive maintenance system, and more. Total Productive Maintenance Training demonstrates the goals, methods and benefits of TPM, including maximizing the effectiveness of production equipment and reducing breakdowns. how a lean TPM training tool is concerned with maximizing the efficiency of production machinery, and it is useful to enhance change in the work culture.
Add Comment
Business Articles
1. Lucintel Forecasts The Glass Fiber In The Global Marine Market To Grow With A Cagr Of 3.7% From 2024 To 2030Author: Lucintel LLC
2. Lucintel Forecasts The Glass Fiber In The Global E&e Market To Grow With A Cagr Of 3.9% From 2024 To 2030
Author: Lucintel LLC
3. Lucintel Forecasts The Global Frp Pole In Telecommunication Market To Grow With A Cagr Of 6.5% From 2024 To 2030
Author: Lucintel LLC
4. Lucintel Forecasts The Global Frp Pole In Power Transmission & Distribution Market To Grow With A Cagr Of 6% From 2024 To 2030
Author: Lucintel LLC
5. Lucintel Forecasts The Global Frp Pipe In Oil And Gas Market To Grow With A Cagr Of 5.1% From 2024 To 2030
Author: Lucintel LLC
6. Lucintel Forecasts The Global Frp Pipe In Chemical Market To Grow With A Cagr Of 3.6% From 2024 To 2030
Author: Lucintel LLC
7. Adopt A Modern Telecom Commission Management System To Fix Revenue Leakages
Author: Kevin
8. Quality Steel Pipes And Tubes With Commitment And Trusted Service
Author: CONTENT EDITOR FOR SAMPHIRE IT SOLUTIONS PVT LTD
9. Lucintel Forecasts The Global Foam Core For The Construction Market To Grow With A Cagr Of 3.7% From 2024 To 2030
Author: Lucintel LLC
10. How Important Is Mutual Fund?
Author: Sagar Shah
11. What Do You Need To Know About Customize Your Own Clothes
Author: Guangzhou Beianji Clothing
12. Detailed Tips To Choose Quality Cabinets And Joinery Melbourne
Author: William Harvey
13. Lucintel Forecasts The Global Foam Core For The Transportation Market To Grow With A Cagr Of 5.4% From 2024 To 2030
Author: Lucintel LLC
14. Silicone Sealing Foam Cord: The Valuable Option For You
Author: Dongguan Senma New Materials Technology Co., Ltd
15. How Investment Banking Companies And Credit Solutions Elevate Wealth Management
Author: Drishti Desai