ALL >> Business >> View Article
Understand The Best Practices For Effective Kaizen Management
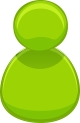
Kaizen is a method to making continuous improvement based on the idea that small, current positive changes can gain important improvements. Typically, it is based on cooperation and promise and stands in contrast to methods that use essential or top-down changes to accomplish transformation. Kaizen is essential to lean manufacturing. It was established in the manufacturing sector to lower flaws, remove waste, boost efficiency, inspire worker purpose and accountability and promote innovation. As a broad idea that carries myriad interpretations, it has been accepted in many other industries, also with healthcare. It can be applied to any area of business and even on the specific level. Kaizen can use a number of methods and tools, such as value stream mapping - which documents, analyses and improves information or material flows essential to produce a product or service and Total Quality Management, which is a management framework that recruits workers at all levels to focus on quality enhancements. Regardless of methodology, in an organizational setting, the effective use of Kaizen rests on gaining support for the method across ...
... the organization and from the CEO down.
Kaizen is a complex of two Japanese words that together translate as "good change" or "improvement." However, Kaizen has come to mean "continuous improvement" through its association with lean methodology and principles. Kaizen has its origins in post-World War II Japanese quality circles. These circles of workers focused on preventing defects at Toyota. They were established partly in response to American management and productivity consultants who visited the country, especially W. Edwards Deming, who argued that quality control should be put more directly in the hands of line workers. Kaizen was carried to the West and popularized by Masaaki Imai via his book Kaizen: The Key to Japan's Competitive Success in 1986. Kaizen management training can give company an important edge over competitors. It contains lean operations and constant improvement, two vital factors to be effective in today’s economy. Another crucial component is empowering team members to participate in finding the opportunity to recover.
Kaizen Best Practices:
Focus on the procedure, not the goal: Process focus might be the most important difference between kaizen management and traditional management styles. Kaizen is based on a philosophy of slight, incremental, constant improvement. When this style is fully operative, it creates a self-sustaining cycle of opportunities and solutions to decrease waste of time, money, and resources. Goal-oriented management attentions on control with a partial definition of success, while kaizen is flexible and adaptive. It uses system of measurement for evaluation rather than to measure the enhancements and meet a predefined number. Finally, process-oriented management appearances at the big picture, while goal-oriented management is more narrowly focused on the short term.
Engage employees in the decision-making process: Employees often feel powerless to make change in their workplaces. They’re supreme resource for ideas and skills, but they believe their voice isn’t heard. Token efforts at engagement like the typical suggestion box don’t produce any meaningful action. On the other hand, Kaizen management contains employees in the development process from identification through execution to recognition. Seeing their position in the company validated gives them the assurance and inspiration to continue looking for more opportunities to improve.
Go after the low-hanging fruit: kaizen management focuses on small, incremental improvement. Employees are encouraged to seek opportunities for change that are low-risk and low-cost. This allows change to be affected fast, creating a momentum that carries through to the next project. It also keeps the energy level high, providing better engagement on the part of employees. These changes make the building blocks that form the culture of continuous improvement.
Do it better, make it better: In traditional business models, if a procedure or system appears to be working reasonably well, it’s expected that it’s operating at maximum effectiveness. Kaizen management assumes that every element of an organization can be enhanced. Employees are encouraged to look at recognized policies and methods with a fresh eye. Instead of thinking up reasons why something can’t be done, they’re urged to ignore conventional limitations and figure out how it can be done.
Eliminate waste in all forms: For many organizations, waste is looked at from a financial viewpoint. For Kaizen management, waste applies to all resources. One resource that can never be replenished is time. Every action must add some value to the company, and employees are encouraged to look for ways to growth efficiency and decrease waste. The workplace is continuously adjusted to be organized in such a way that no pointless steps are taken.
Don't throw money at problems: Some enhancements will need capital, but spending money or hiring people is not kaizen’s first line of defense. Instead, the most successful teams use innovation, creativity, and experimentation to improve before writing a check. In fact, budget-constrained organizations have even more reasons to practice Kaizen.
Add Comment
Business Articles
1. Lucintel Forecasts The Glass Fiber In The Global Marine Market To Grow With A Cagr Of 3.7% From 2024 To 2030Author: Lucintel LLC
2. Lucintel Forecasts The Glass Fiber In The Global E&e Market To Grow With A Cagr Of 3.9% From 2024 To 2030
Author: Lucintel LLC
3. Lucintel Forecasts The Global Frp Pole In Telecommunication Market To Grow With A Cagr Of 6.5% From 2024 To 2030
Author: Lucintel LLC
4. Lucintel Forecasts The Global Frp Pole In Power Transmission & Distribution Market To Grow With A Cagr Of 6% From 2024 To 2030
Author: Lucintel LLC
5. Lucintel Forecasts The Global Frp Pipe In Oil And Gas Market To Grow With A Cagr Of 5.1% From 2024 To 2030
Author: Lucintel LLC
6. Lucintel Forecasts The Global Frp Pipe In Chemical Market To Grow With A Cagr Of 3.6% From 2024 To 2030
Author: Lucintel LLC
7. Adopt A Modern Telecom Commission Management System To Fix Revenue Leakages
Author: Kevin
8. Quality Steel Pipes And Tubes With Commitment And Trusted Service
Author: CONTENT EDITOR FOR SAMPHIRE IT SOLUTIONS PVT LTD
9. Lucintel Forecasts The Global Foam Core For The Construction Market To Grow With A Cagr Of 3.7% From 2024 To 2030
Author: Lucintel LLC
10. How Important Is Mutual Fund?
Author: Sagar Shah
11. What Do You Need To Know About Customize Your Own Clothes
Author: Guangzhou Beianji Clothing
12. Detailed Tips To Choose Quality Cabinets And Joinery Melbourne
Author: William Harvey
13. Lucintel Forecasts The Global Foam Core For The Transportation Market To Grow With A Cagr Of 5.4% From 2024 To 2030
Author: Lucintel LLC
14. Silicone Sealing Foam Cord: The Valuable Option For You
Author: Dongguan Senma New Materials Technology Co., Ltd
15. How Investment Banking Companies And Credit Solutions Elevate Wealth Management
Author: Drishti Desai