ALL >> Business >> View Article
Refractory Silica Brick For Hot Blast Stove
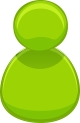
After the high temperature area of the hot blast stove is transformed with a silica brick lining, due to the characteristics of the volume expansion of the silica brick at 270-310°C and 570-610°C, the temperature of the silica brick hot blast stove must be precisely controlled during the baking process.
1. The purpose of the oven
(1) Slowly drive away the moisture in the masonry of the hot blast furnace, avoid sudden and massive evaporation of the moisture in the masonry due to the rapid temperature change, and cause damage to the refractory; make the refractory bricks expand evenly, slowly and fully to avoid the masonry refractory due to heat Stress concentrations or lattice transformations cause damage, extending their useful life.
(2) Make the 3# hot blast stove regenerator checkered bricks accumulate enough heat, and can provide high air temperature for the blast furnace after being put into use.
2. The principle of hot blast furnace for silica brick
(1) During the drying process of the 3# hot blast furnace, the temperature of the left and right arch sides is used as the reference basis for ...
... temperature rise, and the temperature of the exhaust gas and the interface temperature of the silica brick are taken into account for the furnace.
(2) The properties of refractory materials vary greatly. The oven should be dried strictly according to the oven curve. By adjusting the flow of gas and air pressure, the actual temperature curve of the dome of the oven should be as close as possible to the corresponding value in the oven curve.
When the vault temperature is in the range of 100-700°C, the temperature deviation should be controlled within ±2°C; when the vault temperature exceeds 700°C, the temperature deviation should be controlled within ±3°C.
(3) The oven is continuously carried out, and it is strictly forbidden to interrupt it.
(4) During the drying process, pay attention to controlling the temperature of the flue, to avoid the temperature of the flue rising too fast due to improper control, so that the high temperature area at the top cannot be controlled according to the temperature required by the oven.
(5) When the oven is finished, close the oven manhole, and lead the blast furnace gas to pass through the burner for normal burning. The gas conversion process should not take too long, and the temperature of the arch side should not be lower than 900 °C when the blast furnace gas is introduced.
3. Preparation before the oven
(1) The masonry of the 3# hot blast stove is completed, and the acceptance is qualified according to the quality standard. The site is cleaned and tidy, and the safety facilities are fully restored.
(2) All testing instruments run accurately, and the cooling water pressure and water flow of the cooling system are normal.
(3) The hydraulic and electrical systems of each valve before the 3# hot blast furnace are debugged, and the linkage test is carried out, with manual and automatic operation conditions.
(4) The installation and debugging of the mixed gas pipeline and valve for the furnace are completed, the switch is flexible, and the mixed gas and compressed air are led to the manhole valve of the hot blast furnace (the mixed gas pipeline is pressed for leak testing, and the glasses valve is debugged in advance) , the work was completed before November 17, 2017.
(5) Lay two layers of clay checkered bricks around the circumference of 2000mm in front of the large wall of the oven manhole, each with an area of about 8m2, and add a fire retaining wall in front of the checkered bricks with a height of 800mm, and lay on the surface of the laid clay checkered bricks. 2mm iron plate, the iron plate evenly cuts 10mm holes every 150mm.
(6) Make 2 oven burners, insert the oven burner into the combustion chamber through the manhole on the arch side, and the insertion length is 2500mm (that is, the distance from the flange surface of the manhole to the center line of the burner head); make DN50mm 1 pistol. The manhole shall be shielded with a shielding board or refractory bricks to prevent a large amount of air from entering the hot blast stove. Cut a 50mm peep hole on the board or leave a 50mm peep hole on the temporary brick wall for visual inspection of the flame.
(7) The blind plate of the outer flange of the combustion valve in the early stage of the oven is not removed (when the temperature of the arch side reaches 900°C, the blind plate is removed and blast furnace gas is introduced for the oven).
(8) Install 2 temporary thermocouples used in the oven on the arch side of the hot blast stove and the interface of the silica brick.
Add Comment
Business Articles
1. Essential Photo Editing Tips To Enhance Your Website's AppealAuthor: ukclippingpath
2. 5 Ways To Revolutionize Telecom With Smart Inventory Management Software
Author: Kevin
3. Rubber Roller: Enhancing Industrial Efficiency And Performance
Author: Anar rub tech pvt.ltd.
4. Tips For Cleaning And Prepping Jars For Candle Making
Author: Namo Creations
5. Vip Desert Safari Dubai
Author: Safari kings deserts
6. Why Byst Offers The Best Mentorship Programs For Entrepreneurs
Author: Byst Youth
7. How A 5kw Solar System Can Power Your Home And Save You Money
Author: Keyur Patel
8. How Long To Get A Title Loan In Wyoming | Ez Car Title Loans
Author: Ez Car Title Loans
9. Lucintel Forecasts The Global Thermoplastic Composites Market To Reach $26 Billion By 2030
Author: Lucintel LLC
10. Essential Features To Look For In An Event Management App
Author: Event Management App
11. Technology Landscape, Trends And Opportunities In The Global Micro-led Market
Author: Lucintel LLC
12. Data Visualization Software Market Forecast: Growth In Cloud Solutions
Author: mmr
13. Lucintel Forecasts The Global Food Packaging Market To Reach $xx Billion By 2024
Author: Lucintel LLC
14. Beyond Wealth: Unlocking The Power Of Family Office Services In India
Author: Drishti Desai
15. Enteral Single Use Syringes Market Size & Share, Analysis 2031
Author: Andy