ALL >> Business >> View Article
Why Frp Pressure Tubes Are The Technology Of The Future
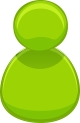
In today’s industrial setting, FRP or Fiber-reinforced thermosetting plastic is being used in various applications, including the storage and transport of highly corrosive and toxic materials or other materials in corrosive environments. Fiber-reinforced plastic first became a preferred alternative to steel, stainless steel, and other materials in 1948. Today, FRP has various applications that take advantage of its corrosion resistance, strength-to-weight ratio, low maintenance, and life cycle cost. This article discusses the multiple applications of FRP pipes and the technological advances that utilize them.
What is Fiberglass?
Fiberglass tanks and pipes are made of glass fiber reinforcement embedded in a cured thermosetting resin called fiberglass reinforced plastic.
FRP piping should not be confused with ordinary thermosetting piping like PVC or polyethylene. These systems usually use non-reinforced pipes and injection-molded fittings, and their strength comes from the bulk of the material used.
On the other hand, FRP piping materials are manufactured by winding processes ...
... that use epoxy resins reinforced with continuous glass filaments. These resins undergo thermosetting, i.e., they experience irreversible chemical reactions as they cure, which results in superior temperature capabilities, while the filament reinforcement makes the components of the pining mechanically far more resistant and sturdier than ordinary non-reinforced thermoplastics.
Using the proper combination of resin, glass fibers, additives, and design, FRP pressure tube manufacturers in India can create a product that meets the equipment designer’s standards.
How are Fiberglass Tubes used?
Initially, FRP pressure tubes were used in oil field gathering lines for various applications ranging from handling flammable and combustible liquids to sewer and water mains in the municipal and industrial markets. There are multiple areas in which FRP pressure tubes are used.
1. Oil and Gas Production Industry: in the oil and gas production industry, it is used for high-pressure applications up to 4000 psi. in harsh environments, like the cold in the Arctic Circle to the heat of the Middle East, FRP pressure tubes are used in both above ground and underground. FRP pressure tubes are also used in hydraulic fracturing and saltwater and CO2 injection.
In the future, oil and gas production industries will require higher pressure rated and larger diameter pipes to control any corrosion. In addition to solving corrosion problems, FRP pressure tubes can also be designed with a flame-resistant additive to reduce flame spread in critical areas.
2. Handling Of Flammable and Combustible Liquids: The best FRP pressure tube is also used to transport flammable and combustible liquids, including high concentrations of alcohol, and to transfer aviation and marine fuels in retail and commercial vehicle refueling facilities.
Since chemical processing involves exposure of tubes to chemicals like acetone, methylene chloride, hydrochloric acid, and so on, special metals like titanium are used for resistance to such chemicals but are very expensive. Using FRP pressure is an ideal alternative that can be used as these are extremely solvent resistant and cost-effective.
3. Sewer and Drainage Piping: While concrete pipes are primarily used in sewer and drainage facilities, many areas prefer the usage of FRP piping. This is mainly because concrete deteriorates rapidly in sewage due to hydrogen sulfide. Hydrogen sulfide decomposes the upper layer of the pipe and eventually causes a cave-in. On the other hand, FRP is unaffected by hydrogen sulfide. As a result, FRP pipes are used as an alternative to concrete pipes.
FRP systems can be more cost-effective than concrete pipes as they have a smoother outside surface and lighter weight. This feature reduces the jacking pressure required to push the piping, thus reducing installation costs and time.
4. Industrial Water and Wastewater: FRP pressure tube for wastewater management can save the customer money in the long-term maintenance and pump operating costs as it is corrosion-resistant. FRP pipes are also resistant to the effects of seawater and wastewater containing acids, alkalis, and other corrosive compounds. Typical uses of FRP pipes in water supply and wastewater applications are desalination plants, seawater intakes, industrial wastewater treatment, and caustic and wastewater transport.
One of the primary reasons fiberglass tanks or piping is used in aggressive environments is corrosion resistance. FRP pressure tube manufacturers provide corrosion-resistant FRP piping solutions for industries. Typical types of corrosion do not affect fiberglass, including galvanic, aerobic, pitting, and inter-granular corrosion that harms metals but not fiberglass.
Although fiberglass can resist various chemicals and temperatures, it requires the right design, fabrication, and installation. The best FRP pressure tube manufacturers in India can provide solutions to match the appropriate application.
Today fiberglass tanks and fiberglass tanks are used in corrosive environments and high-pressure applications. These systems are widely used in retail petroleum, exploration, production, chemical, municipal and industrial applications.
FRP pressure tube manufacturers provide complete fiberglass piping systems for various applications. They also assist customers with site layout, anchoring, support spacing, flow rate design, material selection, and installation procedures. These fiberglass pipes provide uninterrupted transportation despite earthquakes, resident environment, or any aggressive modes of transportation.
About Author
I have been writing informative and high-quality article on Wastewater Treatment Plant. In the above articles have covered topics such as frp pressure tube manufacturers in India, frp pressure tube for wastewater management, frp pressure tube, frp pressure tube manufacturers
Add Comment
Business Articles
1. Essential Photo Editing Tips To Enhance Your Website's AppealAuthor: ukclippingpath
2. 5 Ways To Revolutionize Telecom With Smart Inventory Management Software
Author: Kevin
3. Rubber Roller: Enhancing Industrial Efficiency And Performance
Author: Anar rub tech pvt.ltd.
4. Tips For Cleaning And Prepping Jars For Candle Making
Author: Namo Creations
5. Vip Desert Safari Dubai
Author: Safari kings deserts
6. Why Byst Offers The Best Mentorship Programs For Entrepreneurs
Author: Byst Youth
7. How A 5kw Solar System Can Power Your Home And Save You Money
Author: Keyur Patel
8. How Long To Get A Title Loan In Wyoming | Ez Car Title Loans
Author: Ez Car Title Loans
9. Lucintel Forecasts The Global Thermoplastic Composites Market To Reach $26 Billion By 2030
Author: Lucintel LLC
10. Essential Features To Look For In An Event Management App
Author: Event Management App
11. Technology Landscape, Trends And Opportunities In The Global Micro-led Market
Author: Lucintel LLC
12. Data Visualization Software Market Forecast: Growth In Cloud Solutions
Author: mmr
13. Lucintel Forecasts The Global Food Packaging Market To Reach $xx Billion By 2024
Author: Lucintel LLC
14. Beyond Wealth: Unlocking The Power Of Family Office Services In India
Author: Drishti Desai
15. Enteral Single Use Syringes Market Size & Share, Analysis 2031
Author: Andy