ALL >> General >> View Article
How To Control Speed Of Servo Motor & Anti-interference Measures
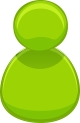
the microelectronic servomotor for control of toys
A servomotor refers to the actuator to control the operation of mechanical components in the servo system and is a subsidy motor indirect transmission device. The servo motor can control speed, whose position accuracy is high, and convert voltage signal into torque and speed to drive the controlled object. A servomotor speed is controlled by the input signal, responding quickly.
In an automatic control system, it is used as an executive component, and has the characteristics of a small electromechanical time constant, high linearity, starting voltage. Besides, it can convert the received electrical signal into the angular displacement or angular velocity output on the motor shaft.
It is divided into DC servo motor and AC servo motor. When the signal voltage is zero, there is no rotation, and the speed decreases uniformly with the increase of torque.
The servo motor as the muscle of the automation factory, is unavoidable in the design and maintenance of the industrial control, so today we will summarize the servo speed control and anti-interference ...
... measures.
This article will introduce the most used 3,000 RPM AC servo.
an ac servo motor, 200v, 3000 rpm, 17-bit
The adjustment of servo speed depends on the control mode. Whether we use pulse to control the speed, analog or direct drive set to control the speed, the corresponding control mode is also different. This article will summarize the speed changes from three different control methods.
Torque Control
Torque control is a kind of mode that we usually adopt. The output torque is set by external analog or direct address assignment. Then the corresponding speed is not confirmed, because the change of friction coefficient of equipment aging and the that of load will affect the output of the speed.
In this case, we basically do not need to adjust the speed. It’s because the speed is automatic, and we need to maintain the stability of the system as well as ensuring that the torque is stable for a long time.
* Solution
You can vary the set torque by changing the analog value in real-time, and you can also change the value of the corresponding address through communication. This method is mainly used in the winding and unwinding device which require strictly on the force of the material, such as the optical fiber pulling device. The purpose of the servo is to prevent the change of the force of the winding material.
Position Control
It is precisely positioned. And the speed and torque can be strictly controlled. In this mode, the rotation speed is generally determined by the frequency of the external input pulse, and the rotation angle is by the number of pulses. Some servos can directly assign the speed and displacement by means of communication.
The tight control of the position mode to speed and position decides it is usually applied in positioning devices. Application fields include CNC machine tools, printing machinery and so on.
We must calculate the upper speed of the servo, only the appropriate servo model can meet the requirements of the field.
cnc machine tool in the industry
Servo upper operating speed = Command pulse rated frequency * Servo upper speed
The servo controller is equipped with an encoder that can receive feedback pulse. The encoder feedback pulse frequency is set on the speed loop and the encoder is set.
Feedback pulse frequency = Number of feedback pulses * Set speed of servo motor (r/s)
Command pulse frequency = Feedback pulse frequency / Electronic gear ratio
So you can also change the “command pulse frequency” to set the servo motor speed.
Speed Mode
The speed can be controlled by the input of analog quantity or the frequency of the pulse. The speed mode can also be located when the outer loop PID control of the upper control device is used, but the position signal of the motor or that of the direct load must be fed back to the upper control device to achieve the calculation.
Relative to the position mode, the position signal of the speed mode has errors. The signal of the position mode is provided by the terminal load detection device, which reduces the intermediate transmission error and relatively increases the positioning accuracy of the whole system.
To use the speed mode when the load inertia is large, we need to set the speed loop gain to make the system more responsive. The vibration of the equipment should be taken into account when adjusting, and the system vibration should not be generated due to the response speed.
When you apply the speed control, you should also pay attention to the acceleration and deceleration settings. If there is no closed-loop control, you need to bring the motor to a complete stop by the zero clamp or proportional control. When the position is closed-loop, the analog quantity cannot be automatically zeroed.
The control system sends the analog voltage instruction of +/-10V to the servo drive to control the speed. The advantage is that the servo will respond quickly, but it is sensitive to field interference and the debugging is a little complex.
The application of the speed control is quite wide, such as the continuous speed control system, closed-loop positioning system by upper position, as well as a system that requires rapid switching of multiple speed segments.
In the process of using and debugging the servo system, a variety of unexpected interference circumstances will occur, especially for the application of the servomotor.
Interference from the Power Supply
In general, you can add the filter to the power module and motion controller of the rotary encoder by adding a voltage regulator, isolation transformer, etc. You should switch the drive to a DC reactor to reduce the interference caused by power input and avoid system failures.
The power line of the servo system should be routed separately, and the distance between the drive and the motor power line should be shortened, so as to avoid interfering with the control line and causing driver failure.
the motion controller lk-03b
Chaotic Grounding System
The ground connection is an effective way to improve the anti-interference performance of electronic equipment, which can suppress the interference of equipment as well as the external interference.
the grounding system with four terminals
But the wrong grounding method will introduce serious interference signals, so that the system can not work normally. The ground wire of the control system generally includes systematic, shielding, alternating and protective.
If the grounding system is chaotic, the potential distribution of each grounding point is uneven, and the potential difference exists between the two ends of the cable shield, the grounding wire, the ground, and the ground points of other devices, which will cause the ground loop current and affect the normal operation of the system.
* Solution
It’s key that you should distinguish the grounding mode that provides good grounding performance for the system.
In addition, you should pay attention to environmental electromagnetic compatibility, and shield high-frequency electromagnetic waves, radiofrequency devices. You are supposed to suppress and eliminate the noise source.
For instance, there shall be not high frequency, medium frequency, high power rectifier and inverter power device on the same power transformer or distribution bus.
The reason is that the distribution line inevitably has a large source of interference. You can install the drive separately in the cabinet, use a mounting plate that is non-metallic, suspend the ground associated with the servo drive, and ground the other measurement system.
Interference inside the System
Electromagnetic radiation between components and circuits in the system will cause interference, such as mutual radiation of logic circuits, analog and logical interaction and mutual mismatch between components.
* Solution
You should choose the shielding line as the signal line and control line to prevent interference.
When the line is longer, for example, the distance is more than 100 m, you should increase the wire section.
You should put the signal and control lines through the pipe to avoid their interference with the power lines.
The main transmission signal is a current signal whose anti-interference performance is relatively good. In practical applications, the sensor output is mostly a voltage signal, which you can convert through a converter.
When you filter the DC power supply of the analog circuit, you can add two capacitors of 0.01uF(630V), of which one is connected to the positive and negative terminals of the power supply, the other connected to the housing and the ground.
If the servo makes a sound and outputs high-frequency harmonic interference, you can connect the 0.1u / 630v CBB capacitor to the housing respectively at the P and N terminal of the servo drive bus power supply.
The shield layer of the control line of the boarding card is connected, and the driver end is not. You should pull out a section of the shield layer and twist it into a strand exposed to the outside.
Use an electromagnetic EMI filter, weld anti-interference resistance on the control line, or connect a magnetic ring on the motor power line.
a three-phase emi filter
The actual conditions may be much more complex, and you need to analyze them on a case-by-case basis.
OKmarts.com Online Store | We provide leading brands of refrigeration compressors, servo motors, Air cylinder and more all over the world. More product's information please visit https://okmarts.com/
Add Comment
General Articles
1. Categorization Of Plant Life CycleAuthor: Anthea Johnson
2. Commercial Spaces Need Style Too! Transforming Cafés & Resorts With Custom Pergolas
Author: Noor Mariam
3. Level Up Your Hana Adventure: Why An Audio Tour Is Your Best Road Trip Companion
Author: Katie Law
4. Best Erp Software Solution Company In Noida For Schools And Colleges
Author: CONTENT EDITOR FOR SAMPHIRE IT SOLUTIONS PVT LTD
5. Hinduism: Environmental Friendliness And Protecting Nature
Author: Chaitanya Kumari
6. From Ai To App Store: How Generative Tech Is Reshaping Ios Experiences
Author: Sara Wilson
7. Faston Service In Noida — Reliable, Affordable & Quick Home Ac Repair Services
Author: faston services
8. What Are The Uses And Benefits Of A Vegetable And Fruit Dryer?
Author: DYNAMIC DRYERS INTERNATIONAL
9. Primary Care Without Insurance In Raleigh
Author: satyamprimarycare
10. All Four Paws Offers Champion English Cream Golden Retriever Puppies In Indiana
Author: Geroge
11. Box Truck Wraps: The Ultimate Moving Billboard For Your Brand
Author: Saifee Signs
12. Generative Ai And Data Science Course In Hyderabad
Author: Hari
13. Mca Guidelines For Company Name
Author: Startupporta Business Services
14. Seo Services In Chennai: Boost Your Online Visibility With Proven Strategies
Author: istudio technologies
15. Best Internet Marketing Service In India
Author: Matrix Web Studio