ALL >> Business >> View Article
Operational Challenges Of Manufacturing Plants And Solutions For Increasing Productivity
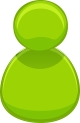
Introduction
The objective of this article is to understand the operational challenges that a manufacturing plant goes through, the root cause of such operational challenges, and how these can be fixed so that there is a smoother flow of goods and higher productivity.
The Symptoms: The Month-end Skew Phenomenon
It is not uncommon to find a lot of trucks waiting outside the Finished Goods area of a manufacturing plant, especially if you happen to visit a plant towards the very end of a month. Have you ever wondered why this happens? The answer is surprisingly simple – a majority of the orders gets completed closer to month-end, and therefore, the dispatches are skewed.
But let us probe a bit further. How can a plant justify this? Are all the end consumers of these products desirous of making purchases only at the end of the month? Surely, this cannot be the case? (For example, let us take the case of a plant that manufactures modular kitchens. It is absurd to think that customers require a kitchen only at the end of the month!) Absurd, this might be; but the truth is, this problem – the ‘month ...
... end skew phenomenon’ - is rather endemic, especially when it comes to Make to Order (MTO) companies. And, it is not limited to just one industry, but across industries. In short, wherever there is assembly of components involved (kitchen/ office furniture, equipment manufacturing, etc.), this is a chronic problem. Better synchronization of components required for assembly somehow happens during the last week of the month. And, this leads to dispatch skew at month-end.
Similarly, if you analyze textiles / garment manufacturing or leather processing plants, where an order has multiple items, and has to be delivered together, you may not notice a production skew; but the order completion improves towards month-end. This again leads to dispatch skew. And, despite these challenges, most of these companies claim very high on time delivery performance!
Why is there an end of the month skew?
Let us suppose that a product requires 10 different components. In assembly plants, even if one component is missing, the product cannot be completed, and therefore, cannot be dispatched. And, typically, a plant does not manufacture just one product. So, we can imagine multiple products requiring multiple components getting manufactured simultaneously. Different Work Centres (WCs) involved in operations in the manufacturing plant start making components during the month, but because one or the other component is missing, there is likely to be only a trickle of completed orders. What happens at month-end is that there is significant expediting of the missing components. With better synchronization of components, a slew of orders gets completed! But how is it possible that companies can report on time delivery after such a skew? Afterall, customers need products throughout the month, and there is no skew in the pattern in these requirements.
Creative Definitions for On Time Delivery
If companies are claiming high on time delivery performance in spite of experiencing dispatch skews at month, they are - let us put it this way – resorting to creative ways of defining the metric. If an order is completed anytime during the month, rather than on the initially committed customer due date, it is considered on time. Similarly, if an order has multiple items, and has to be delivered together, but if the order is delivered partially, it is considered to be delivered on time, even though it means nothing to the customer!
If a company truly has efficient operations, and has high on time delivery performance, it will not experience customer urgencies, nor would the customers feel the need to follow up on their orders. Such companies will not need to quote a range such as ‘3 to 4 weeks’ or ‘4 to 6 weeks’ while setting a delivery period. Such a range clearly reveals that customers would be foolish to put their faith in delivery reliability.
Technological Advances to the Rescue?
This chronic unreliability is strange considering the plethora of technological advances that have occurred in recent years, and the systems/ applications that are deployed in manufacturing companies today (especially in MTO environments), such as ERP, APO, robotics/ automation. The main reason for poor improvement in reliability is the fact that such technological advances have not solved the operational problems at the root level. They are merely addressing/ treating the symptoms. For example, if while trying to expedite a late order, the machine breaks down at the last moment, or if the trained operator is not available owing to an emergency, we tend to come to the conclusion that it is an operations problem, that the real problem is machine reliability or absenteeism. And, the entire focus then shifts to improving operational efficiencies by developing better machines, deploying Total Preventive Maintenance, automation, IT for better visibility, etc. And, let us assume for a moment that the manufacturing plant does succeed in building better machines, etc. Do we see on time delivery going up significantly? Not at all. Order execution lead time remains the same as earlier, more or less. Reason? The root cause or the underlying conflict has not been solved at all.
What is the Root Cause of all these Challenges?
In their desire to utilize all the work centres to the maximum with minimal change overs, the production planner releases a plan (usually monthly) with a loading that is often more than the available immediate capacity of the plant. The thinking is that if you load more, it will create pressure, which, in turn, will lead to better operational efficiencies, better utilization and higher output. However, this is not true. When one loads the plant more, it provides a large choice set of orders to every WC. Every WC “cherry picks” products, or clubs orders to form bigger batches (even if due dates of each order are far apart) in order to minimize set-ups and to get better productivity. Compounding this problem further is the fact that the cherry picking or clubbing considerations are different at each WC. This elongates production lead times. However, as the month progresses, the pressure of billing and customer follow-up/ urgencies force the plant to focus on order completion. This is the time when different components required for an order or product start coming together, resulting in production skew towards the month-end, and poor on time performance.
Due to poor plant reliability and a production skew at month-end, the planner can come up with the next month’s plan only after month-end, considering the back log and the orders for the next month. During this finalization of the planning-for-the-next-month phase, the plant undergoes starvation in the beginning of the month. This starvation, along with urgencies (especially towards the later part of the month) lead to loss of output, which, in turn, puts further pressure to load more. Result? The plant is caught in a never-ending vicious loop of poor on time delivery, loss of output, higher order lead times and high inventories. Even though intuitively the plant knows that if they load with a few orders, they would get better on time delivery and lower lead times, the fear of poor utilization, forces them to load more.
In a nutshell, the conflict between capacity utilization and on time delivery remains unresolved.
Solutions that Failed
Academicians, including IT folks, have tried to solve the conflict by deploying a tool that would take into account the precise capacities of each WC, loading the plant according to the capacities defined, and which could also quickly do corrections in the plan when things go haywire, rather than waiting till month end – what is known in the industry as Advanced Planning & Optimization (APO). But this did not prove beneficial either.
Firstly, getting precise capacities itself is a big challenge due to product mix impact. This can be a really complex task in plants that handle a variety of products and sub-components with varying process times. Therefore, loading the plant exactly based on capacities defined itself is practically not achievable. Even though plans can be re-scheduled easily and frequently, the practice of releasing a plan for the month continues. Due to this practice, cherry picking/ clubbing future orders also continues, leading to all the symptoms as explained earlier. If the plant is highly unreliable, the ability to re-schedule quickly is of no use, because no plant can really follow a plan that keeps changing often! Let me explain this better using what happens in our airports.
An Analogy – The Scene at an Airport
Typically, on Monday mornings or Friday evenings, one would witness long queues at the check-in counters. There are two types of people that one would be able to see in these queues – people who get to the airport at the last moment, that is, those who have a flight to catch, say, in the next 45 minutes or an hour; the second type being those who have a flight in the next two to three hours. Now, let us suppose that it is not possible to add more check-in counters. What would ensue? Simple, some people may miss their flights, while a few would have checked in very early. How can we solve this problem?
It is simple really. Do not allow people to check-in if their flights are departing after, say, one and a half hours. This way, those travellers who have a flight to catch in the next 45 minutes have a greater chance of not missing their flights.
Let us apply this learning in the case of a plant. Many WCs in a plant work on components in the WIP phase, even though their due date is not imminent. At the same time, there might be a basket order waiting for just one component to be ready so that the entire order can be dispatched, but which is not being worked upon by any WC. So, the solution is to allow only a few orders to be worked upon at a time. In most environments, where touch time (i.e., just the machine process time, and no waiting time), is less than 10% of the total production lead time, visibility to the plant can be reduced by half. This means that in a plant where production lead time is, say, about a month, the plant is allowed to work only on those orders that are due in the next 15 days, and not on all the orders required in the entire month. (The one-and-a-half-hour limit in the case of the airport analogy.)
Since the choice set available at each WC is limited (around half from the earlier case), it prevents “cherry picking”/ clubbing of future orders for bigger batches. This leads to faster order completion.
But the old question continues to haunt us – if we do not load the plant optimally, then does this not mean poor utilization of resources?
The way out of this operational challenge is to deploy a solution with ‘Push-Pull’ mechanism. The ‘Push’ mechanism is from a planning perspective. Orders are packed to capacity on the constraint resource (because Critical Constraint Resource [or CCR] determines the output of the plant) based on its current capability. Approximate capacities are good enough. One does not need a precise definition unlike APO. Order due dates are determined based on the current pending load and not by overloading the plant.
The ‘Pull’ mechanism is deployed in execution. Since CCR determines the output of the plant, a certain WIP is maintained between the CCR and the first WC, which is half of the current WIP (as explained earlier). The objective of this load/ WIP is to not only prevent cherry picking but also starvation of CCR. So, if for some reason, this load drops below the desired level, more orders can be released into the manufacturing plant. Similarly, if this load is going up due to lower output, further release of orders is stopped.
In short, we can be conservative in planning by not overloading the plant, but be aggressive in execution by pulling orders when the load goes down. By doing this, the plant becomes highly reliable, and the need for re-scheduling the plan goes away. One is able to achieve not only higher CCR utilization, but also perfect de-coupling between Planning and Execution – something that was next to impossible in the previous scenario.
The fact that the plant will achieve increased productivity, high on time delivery and reduced order execution time if one deploys the Push-Pull solution is just the tip of the benefits that a plant can hope to enjoy. We can additionally put a priority mechanism in place depending on how close the order is to its due date. Thus, if an order has a due date that is earlier than that of another one, the first order would get a higher priority at the WC. This priority can be shown visually at the shop floor (and shown in an easy-to-understand manner). The outcome would be an entire system that runs almost on auto-pilot.
The entire focus of this method is to ensure that orders can be completed faster. That is, reduce production lead time, increase productivity, and thereby, facilitate high on time delivery. For this, we continuously collect data regarding where the orders are waiting for the highest time, and then launch an improvement initiative to reduce this waiting time. For example, if the waiting queue is high before a particular WC, then the improvement project would explore how productivity can be improved so that the waiting time reduces. Techniques such as Lean, Six Sigma, etc. can be deployed to improve productivity of that WC. And, these initiatives should be taken continuously. It is called POOGI. It not only helps reduce lead time in the plant but also increases output of the system.
The Benefits
WIP and production lead time will reduce by half. Fire-fighting/ urgencies from customers will get eliminated due to reduced lead time. On time delivery is expected to sustain in the high 90s. The flow of material in the plant will be faster as the plant is working on a few orders. There will be no jams, and, therefore, the output from the plant is staggered throughout the month rather than showing a skew at month end. Also, since there is no starvation at the beginning of the month, there will be better flow. And, without urgencies / re-scheduling, the output of the plant (i.e., plant productivity) can increase significantly - by at least 30%.
And, if this is not exciting enough, the icing on the cake is - this change does not require any investment or additional resources!
Add Comment
Business Articles
1. Why Bookkeeping For Cpa Firms Is Essential For Growth And ComplianceAuthor: Niharika Jain
2. Kitchen Remodels Ideas: Farmhouse Kitchen Design Ideas To Warm Your Heart
Author: Vikram kumar
3. Top 8 Bi Tools With Intelligent Data Analytics Capabilities
Author: Maria
4. Top 5 Mistakes To Avoid When Getting An International Shipping Quote
Author: Tom
5. The Ultimate Guide To Cheap Rdp: Affordable And Secure Remote Desktop Solutions
Author: DigiRDP
6. The Role Of Financial Advisory Companies In India
Author: Drishti Desai
7. How Jaspire Makes Student Visa Approvals Faster And Easier
Author: pavitra
8. Finding The Best Pediatric Eye Doctor In Thane For Your Child’s Vision Care
Author: Anil Eye Hospital
9. Retirement Planning In 2025
Author: jkanishk
10. Cynosure Apogee For Rent: Expand Your Laser Hair Removal Services Without The Upfront Cost
Author: Ryan
11. Selectech, Inc. Receives Environmental Product Declaration For Ecolock
Author: Steven Dubin
12. Master Photo Editing With Google Photos: Top Tips And Professional Services To Elevate Your Images
Author: Sam
13. Mg Astor Automatic Price In Chennai: A Smart Suv Worth Exploring
Author: balaji
14. Find The Best Morris Garage Showroom
Author: balaji
15. How To Save Hours On Editing With Smart Clipping Path Techniques
Author: ukclippingpath