ALL >> Business >> View Article
Digital Transformation Is The Key To Leading The Innovation Of Chemical Suppliers
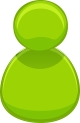
A few decades ago, chemical suppliers were among the first to take advantage of the wave of digital transformation, integrating data into R & D teams and using computer assistance in facility design. "However, in recent years, the chemical sector has lagged behind companies in banking, retail, media and telecommunications, exploring innovative ways to use digital technology to improve their companies' business only when they are running, but also in attracting customers and generating new value," a recent report shows management consulting firm Bain and the company. "Now, chemical suppliers are starting to innovate and catch up."
Industry leaders have recognized that they need not only to implement digital solutions for it, but also to focus on digital tools, which can help them to complete a pre-set, company wide strategy. Chemical plant managers can no longer see their technology as a means of identifying and solving individual problems or equipment components. The reactive attitude is that technology is just another way to improve the old business model, because factories need ...
... to build flexibility and full collaboration, so it no longer makes sense. The complexity and complexity of plant operations require data and machine learning monitoring so that all parts of the plant can communicate. This is necessary to provide plant managers with tools to promote production, cut costs, prevent delays and promote innovation. It is also necessary for more and more popular measurement methods, such as overall equipment efficiency (OEE) formulas, which are used to accurately collect where the factory has achieved success and where it has not achieved expectations.
Opportunities brought by the new reality of Globalization
According to the data of the international society of automation, the demand for imported chemicals in Asia has surged in recent years, which has promoted the development of the global market. Asia has half the world's middle class. As markets in Europe and North America stagnate, surging demand in countries such as China has opened new avenues for growth.
But at the same time as this windfall, the global dynamics agency has also brought new pressure. The volatility of global commodity prices is affecting already meager profit margins. With the diversification of the market, small-scale digital native companies have opened up market segments through personalized products. In 2016, the European chemical agency estimated that about 70000 new chemical companies were preparing to apply for registration, including many small and medium-sized specialty chemical suppliers. This is three times as much as the two rounds of financing in 2013 and 2010. These companies have established a new level of customer demand and brought new competition to the large producers who once dominated the field.
Data collection method
As such challenges continue to grow, industry leaders have recognized that data is the solution. Data is expected to accelerate the growing trend of cooperation between it (or information technology, including the Internet of things, artificial intelligence and advanced analysis) and ot (or operation technology, usually refers to the control and automation technology supporting operation, including additive manufacturing, advanced materials and Robotics). According to solutions, a data management consulting firm, "the growing collaboration between the IT team and the operations technology team provides an opportunity to share a strategic vision and better integrate all systems (including it and OT) with the business objectives of the enterprise."
In addition, data feedback from intelligent sensors (such as those captured by Sam guard's AI drive system) can identify patterns, predict and diagnose possible faults. Smart devices like precognize's predictive monitoring platform can send information to plant operators about maintenance updates, potential failures, parts ordering and delivery plans. All of these enable manufacturers to minimize planned or reactive maintenance and focus on predictive maintenance.
These systems constitute a real-time knowledge database for the whole company, which in turn creates space for different plant departments, even different plants around the world, to benefit and learn from problems or successes in predictive maintenance, performance optimization and facility design. With this high-resolution overview of plant activities, managers can enjoy control over the plant and its operations, and be able to adjust more quickly and accurately when manufacturing or supply chain problems arise.
Add Comment
Business Articles
1. Repair And Maintenance Guide For Garden FencingAuthor: Vikram kumar
2. Lucintel Forecasts The Global Palatant Market To Grow With A Cagr Of 5% From 2024 To 2030
Author: Lucintel LLC
3. Choosing The Right Gas Regulator In Florida: A Complete Guide
Author: Technico
4. Why Deer Park Learners Trust Local Driving Instructors
Author: Aintree Driving School
5. How To Properly Install And Uninstall Your Air Conditioner System With A Low Budget
Author: Neha Jain
6. What Is The Role Of Pdca In Iso 50001?
Author: William Charles
7. Step-by-step Instructions On How To Generate Inventory Reports Quickbooks?
Author: Jack Edwards
8. How To Track Employee Work Hours Efficiently With Trackhr
Author: TrackHr App
9. From Grounded To Global: 4 Ceos Rewiring India’s Aviation Sky
Author: Skyone
10. The Role Of Automation In Modern Cloud Migration Methodology
Author: Netscribes
11. Master Photo Retouching | Steps To Become A Photo Editing Expert
Author: ukclippingpath
12. Great Dependability And Performance Are The Reasons For Extensive Use Of Hydro Pneumatic Press
Author: David Camp
13. Best Lasik Eye Surgery For A Spectacle-free Life
Author: Anil Eye Hospital
14. Industrial Oven Manufacturers In Coimbatore
Author: Heatcon Sensors
15. Plumbing In North Salt Lake: Your Guide To Reliable Services
Author: Brown Jones