ALL >> Business >> View Article
Oxyfuel Gas Cutting
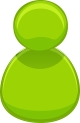
The oxyfuel cutting process is the most widely applied industrial thermal cutting process because it can cut thicknesses from 0.5mm to 250mm, the equipment is low cost and can be used manually or automatic. There are several fuel gas and nozzle design options that can significantly enhance performance in terms of cut quality and cutting speed.
Oxyfuel cutting, also referred to as oxyfuel flame cutting and oxyfuel gas cutting, is the most economical process for cutting mild and low-alloy steel, even with weld preparations involved. Oxyfuel cutting is regarded as one of the most important production processes in the entire metal industry.
Over 120 years, Messer Cutting Systems has provided and developed leading-edge technology for the global metalworking industry. We have
perfected the design and function of straight oxyfuel cutting machines and bevel oxyfuel cutting machines, which deliver high-quality cuts, reliable service, and considerable savings to the cutting process.
When Should the Oxyfuel Cutting Process Be Used?
The oxyfuel cutting process is ideal for when the surface of the material ...
... to be cut is made of mild steel and low alloy steel and the thickness of the material to be cut is greater than 2 inches (50 millimetres).
The oxyfuel cutting process is favoured when the cut edge of plasma is deemed unacceptable or if you are looking for a low-cost alternative.
If you have questions about whether the oxyfuel cutting process is ideal for an application, our sales team is available to address your questions and discuss specific products.
Oxyfuel Cutting Advantages and Disadvantages
With oxyfuel cutting applications, fuel gas and oxygen are used to generate the cutting flame. Messer Cutting Systems supplies gases-including acetylene, MAPP, propane and natural gas-and information relative to your requirements.
Advantages:
Straight-edge quality and high accuracy.
Bevel strip cutting.
Pierce mild steel up to 4 inches thick (101 millimeters) to 5 inches (127 millimeters) thick.
Edge start and cut steel 10 inches (254 millimeters) to 12 inches (304 millimeters) thick.
With multiple torches, produce multiple parts, reducing time and labor.
Disadvantages:
Cannot cut stainless steel under normal circumstances.
Slower cut speeds compared with plasma cutting.
Thin material cutting might warp.
Difficult to produce holes smaller than two times the steel’s thickness.
What Does the Oxyfuel Cutting Process Involve?
Oxyfuel cutting is a combustion process using oxygen or a fuel gas flame. The heating flame warms up the material to its ignition temperature. Next, an oxygen jet of at least 99.5 percent purity is blown onto the heated spot, oxidizing the metal. Burning metal immediately turns to liquid iron oxide.
This oxygen jet is the origin of the term “flame cutting.”
The torch is then moved, and a narrow cutting slot, commonly called a kerf, is created. The slag is removed from the kerf. The cut’s quality depends
on the material’s surface condition, cut velocity and thickness.
All low-alloy steel with a material thickness of as much as several inches can be cut using this process. Despite the growing prominence of other cutting processes such as plasma cutting and laser cutting, oxyfuel flame cutting remains a highly economical process. When it comes to cutting heavy material thicknesses up to 35 inches (900 millimeters), oxyfuel flame cutting simply is unrivaled as a cutting process.
Oxyfuel cutting ensures reliable hole piercing and high cut quality. Component production will be at their finished sizes without any need for further processing. For weld seam preparations, V, Y, X and K bevels can be produced.
Oxyfuel Cutting Characteristics
Plate thickness: 3 millimeters up to 35 inches (900 millimeters).
Typical: 10 millimeters up to 12 inches (300 millimeters).
Oxyfuel Cutting Features
Good cut quality.
Smooth, vertical planes of cut.
Metallurgical perfect surfaces (oxidized).
Carbonizing and hardening within the area of the heat-affected zone.
High heat input.
Wide range of material thickness.
Low cutting speed.
Oxyfuel Cutting Gas Types
Common fuel gas types include acetylene, MAPP, propane and natural gas.
Acetylene: Hottest gas but can be unstable and expensive.
MAPP: Hot gas but not as available as other gases.
Propane: Cheaper and clean-burning but not as hot as other gases.
Natural gas: Cheaper and widely available but offers low delivery pressure.
For more details visit: https://in.messer-cutting.com/
Add Comment
Business Articles
1. Essential Photo Editing Tips To Enhance Your Website's AppealAuthor: ukclippingpath
2. 5 Ways To Revolutionize Telecom With Smart Inventory Management Software
Author: Kevin
3. Rubber Roller: Enhancing Industrial Efficiency And Performance
Author: Anar rub tech pvt.ltd.
4. Tips For Cleaning And Prepping Jars For Candle Making
Author: Namo Creations
5. Vip Desert Safari Dubai
Author: Safari kings deserts
6. Why Byst Offers The Best Mentorship Programs For Entrepreneurs
Author: Byst Youth
7. How A 5kw Solar System Can Power Your Home And Save You Money
Author: Keyur Patel
8. How Long To Get A Title Loan In Wyoming | Ez Car Title Loans
Author: Ez Car Title Loans
9. Lucintel Forecasts The Global Thermoplastic Composites Market To Reach $26 Billion By 2030
Author: Lucintel LLC
10. Essential Features To Look For In An Event Management App
Author: Event Management App
11. Technology Landscape, Trends And Opportunities In The Global Micro-led Market
Author: Lucintel LLC
12. Data Visualization Software Market Forecast: Growth In Cloud Solutions
Author: mmr
13. Lucintel Forecasts The Global Food Packaging Market To Reach $xx Billion By 2024
Author: Lucintel LLC
14. Beyond Wealth: Unlocking The Power Of Family Office Services In India
Author: Drishti Desai
15. Enteral Single Use Syringes Market Size & Share, Analysis 2031
Author: Andy