ALL >> Business >> View Article
Zinc Plating Process: Types, Process & Conclusion
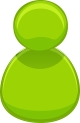
Zinc is known for its non-corrosive properties. This is the main reason why zinc plating is becoming so famous among the manufacturers. Zinc plating simply stops the rusting process from getting started. There are various forms of zinc plating available in the market: Chloride Zinc plating, alkaline non-cyanide zinc, Zinc alloy plating, and alkaline cyanide zinc.
Choosing among all these options is a really tough decision for you. To get to know the best form of zinc electroplating, you have to keep various things in mind because every equipment you manufacture needs the right and suitable plating line.
Zinc Plating Process: Types and Forms:
The application of zinc coating/plating depends on the type of substrates, coating requirements and the cost of the process. You have to keep in mind the specifications of the substrate required for the process every time before you choose any of the zinc plating methods. You also have to consider the zinc deposit and the zinc alloy deposit of substrate you chose. Keep in mind the corrosion protection requirements and the uniformity of the deposit thickness before ...
... starting the process. Do not forget to include the cost of the whole operation and the environmental restrictions. After making sure all the prerequisites, you can proceed with the process of zinc plating. You can opt for any process you find suitable as per your product’s need:
1. Acid Chloride Electroplating: This method makes the whole plating process faster, efficient, produces less waste and less side reactions due to high cathode efficiency. But this method has one major downside and that is the zinc plating chemicals used in the process are highly corrosive. Hence, if not performed with high precision and thorough rinsing, the process might pose a danger to the final coating.
v2. Zinc Cyanide Electroplating: this method is the most common zinc electroplating method in the industry. Due to high regulations imposed on this method, its popularity keeps on fluctuating. The advantage of this method is the usage of a low current density to parts and the major setback of the same is the hydrogen embrittlement problem of the used cyanide which could disturb the whole process.’
3. Alkaline Non-Cyanide electroplating: People prefer this method because of its cost efficiency and reliability. Though, the zinc plating chemicals used in this method consists of high levels of carbonates that sometimes cause a reduction in the solution conductivity which later on, disrupts the depositing process. This is the major drawback of the method.
To deal with all above-mentioned processes and their setbacks, you require a high level of technical knowledge, expertise, special advanced machinery, good quality electroplating equipment, rectifiers, ancillary tanks plating station, and the reservoir to perform zinc plating process.
Typical Zinc Application Process includes:
1. Preparation of the surface by proper cleansing: Before starting the plating process, you should make sure that the surface of the substrate that you have chosen for plating is properly cleaned. Any contaminants, dirt or dust will reduce the adhesion between the zinc and the substrate’s molecules, and you will not get the smooth coating surface.
2. Preparation of electroplating solution: To make an appropriate electroplating solution, you have to make sure that the chosen substrate gets fully immersed in the solution (also known as plating bath) that contains zinc ions and other chemicals that boost up the plating process.
Acid zinc and alkaline zinc can be used in the process. Though acid zinc is more efficient than alkaline zinc in terms of fast electro-deposition rate and better coverage, you will find it less powerful and flexible as compared to that of alkaline zinc.
3. Opting for the best plating procedure: Once you are done with the solution part, you are ready for starting the plating process. You can opt for either rack plating procedure or barrel plating procedure. In rack plating, the larger particles are fixed to the metal racks which are then placed within the tank that contains the plating bath. On the other hand, in the case of barrel plating, smaller particles/components are kept in the barrel plating equipment. After placing the components, they are rotated to provide a smooth finished coating surface.
4. Electric current: Since electroplating works on the principle of electro-deposition, the substrate chosen in the process is used as a cathode. Then you will observe the introduction of a direct current (DC) in the solution originated from the anode. The DC starts flowing towards the cathode that is the substrate and starts depositing zinc ions on its surface. When the whole circuit is completed, you will observe the current flowing back towards the anode. This process continues till you get the whole surface of the substrate to be covered with the zinc.
5. Post-treatment activities: once these parts are ready to use, you should rinse them thoroughly with clean water to remove the leftovers or contaminants. Then the final products are expected to pass through the dryness test. Zinc-plated parts must be dry. In case of additional corrosion protection, you can also consider the application of sealers.
Takeaways:
1.Avoid using zinc plating in extreme situations like the temperature level more than 260 degrees Celsius.
2.Avoid using zinc plating for seawater/marine applications because of the high salinity of the water that might corrode the zinc layer.
3.Avoid tropical environments because they are highly humid and can easily cause severe corrosion to the zinc.
4.Avoid the contact of zinc-plated equipment with high moisture condensed spaces/areas to avoid their corrosion.
Add Comment
Business Articles
1. Lucintel Forecasts The Glass Fiber In The Global Marine Market To Grow With A Cagr Of 3.7% From 2024 To 2030Author: Lucintel LLC
2. Lucintel Forecasts The Glass Fiber In The Global E&e Market To Grow With A Cagr Of 3.9% From 2024 To 2030
Author: Lucintel LLC
3. Lucintel Forecasts The Global Frp Pole In Telecommunication Market To Grow With A Cagr Of 6.5% From 2024 To 2030
Author: Lucintel LLC
4. Lucintel Forecasts The Global Frp Pole In Power Transmission & Distribution Market To Grow With A Cagr Of 6% From 2024 To 2030
Author: Lucintel LLC
5. Lucintel Forecasts The Global Frp Pipe In Oil And Gas Market To Grow With A Cagr Of 5.1% From 2024 To 2030
Author: Lucintel LLC
6. Lucintel Forecasts The Global Frp Pipe In Chemical Market To Grow With A Cagr Of 3.6% From 2024 To 2030
Author: Lucintel LLC
7. Adopt A Modern Telecom Commission Management System To Fix Revenue Leakages
Author: Kevin
8. Quality Steel Pipes And Tubes With Commitment And Trusted Service
Author: CONTENT EDITOR FOR SAMPHIRE IT SOLUTIONS PVT LTD
9. Lucintel Forecasts The Global Foam Core For The Construction Market To Grow With A Cagr Of 3.7% From 2024 To 2030
Author: Lucintel LLC
10. How Important Is Mutual Fund?
Author: Sagar Shah
11. What Do You Need To Know About Customize Your Own Clothes
Author: Guangzhou Beianji Clothing
12. Detailed Tips To Choose Quality Cabinets And Joinery Melbourne
Author: William Harvey
13. Lucintel Forecasts The Global Foam Core For The Transportation Market To Grow With A Cagr Of 5.4% From 2024 To 2030
Author: Lucintel LLC
14. Silicone Sealing Foam Cord: The Valuable Option For You
Author: Dongguan Senma New Materials Technology Co., Ltd
15. How Investment Banking Companies And Credit Solutions Elevate Wealth Management
Author: Drishti Desai