ALL >> Business >> View Article
Process Fans In Manufacturing Of Coke
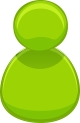
In melting iron ore, coke finds its use as fuel and also a reducing agent. Coke is grey, porous and hard, and contains a few impurities along with high carbon content. Coke is produced when coal is baked, and it turns into carbon. The impurities in it burn off, leaving behind the high carbon coal. Burning coke produces little smoke, but the heat produced here is immense. Therefore, coke is used in smelting steel and iron. The manufacturing process of coke involves the extensive use of industrial fans.
Two processes are involved in the manufacturing of coke. These are the by-product process and the heat recovery process
By Product Process:
In this process, coal is carbonated without the presence of air in coking chambers by indirect heating. The impurities are to be baked at a high temperature, often ranging between 1000 to 2000 degrees Celsius. Volatile materials escape from the coal mass as gases during this process when the required temperature is attained. These gases are piped to a by-product plant where they are cooled down in several steps to extract the by-products.
Heat Recovery Process: ...
...
The heat recovery process involves combusting volatile matter which leads to heat generation. Through conduction and radiation, this heat gets across to the mass of coal. The heat of the flue gases is used for the production of steam and generation of power. In this process, only coke is obtained from the ovens and no by-products are recovered.
How Do Process Fans Help In Manufacturing Coke?
Primarily, three types of industrial fans are used in the manufacturing of coke. These include combustion fans, exhaust fans and cooling fans.
Combustion Fans
Industrial process fans are used in the coke oven plants as combustion fans. This ensures that the air is combusted, in burning the coal. Combustion in the coke oven releases hot air which bakes the coal in the oven. The combustion process gets a boost when these fans are used.
Exhaust Fans
Industrial process fans are used in the coking oven to eliminate the gases. Exhaust fans are used in removing the evolved gases that are used to form by-products or used in steam production and generation of power. These exhaust fans ease up the process of making coke.
Cooling Fans
In the final stage of producing coke, cooling fans are used to eliminate the heat generated as a result of compression from the gas oven of coke. The efficiency of many by-product production processes is significantly improved at a lower temperature. Failure to use the right cooling equipment can mess up the efficiency of the production process. Besides, certain processes like the removal of water wash ammonia take place at lower temperatures. Unless the materials are cooled down, proper functioning will not take place. Therefore, cooling fans are used to reduce the temperature of the coke oven gas, connecting it directly with a cooling medium. In manufacturing plants, either wash oil or water is used as the cooling medium.
As can be seen above, the process of making coke involves a lot of heat and very hot gases. The product process requires the right equipment for the efficient and smooth production of coke. In the coke manufacturing process, industrial process fans find several applications at various stages of the process.
Reitz India manufacturer of centrifugal fans and blowers is committed to provide tailor-made solutions to various industrial processes and air pollution control systems in India and other neighboring countries. Reitz India centrifugal fans find wide applications in pollution control, ventilation, dust collection, fume extraction, ID, FD and PA fans in boilers and furnaces etc.
Add Comment
Business Articles
1. Lucintel Forecasts The Glass Fiber In The Global Marine Market To Grow With A Cagr Of 3.7% From 2024 To 2030Author: Lucintel LLC
2. Lucintel Forecasts The Glass Fiber In The Global E&e Market To Grow With A Cagr Of 3.9% From 2024 To 2030
Author: Lucintel LLC
3. Lucintel Forecasts The Global Frp Pole In Telecommunication Market To Grow With A Cagr Of 6.5% From 2024 To 2030
Author: Lucintel LLC
4. Lucintel Forecasts The Global Frp Pole In Power Transmission & Distribution Market To Grow With A Cagr Of 6% From 2024 To 2030
Author: Lucintel LLC
5. Lucintel Forecasts The Global Frp Pipe In Oil And Gas Market To Grow With A Cagr Of 5.1% From 2024 To 2030
Author: Lucintel LLC
6. Lucintel Forecasts The Global Frp Pipe In Chemical Market To Grow With A Cagr Of 3.6% From 2024 To 2030
Author: Lucintel LLC
7. Adopt A Modern Telecom Commission Management System To Fix Revenue Leakages
Author: Kevin
8. Quality Steel Pipes And Tubes With Commitment And Trusted Service
Author: CONTENT EDITOR FOR SAMPHIRE IT SOLUTIONS PVT LTD
9. Lucintel Forecasts The Global Foam Core For The Construction Market To Grow With A Cagr Of 3.7% From 2024 To 2030
Author: Lucintel LLC
10. How Important Is Mutual Fund?
Author: Sagar Shah
11. What Do You Need To Know About Customize Your Own Clothes
Author: Guangzhou Beianji Clothing
12. Detailed Tips To Choose Quality Cabinets And Joinery Melbourne
Author: William Harvey
13. Lucintel Forecasts The Global Foam Core For The Transportation Market To Grow With A Cagr Of 5.4% From 2024 To 2030
Author: Lucintel LLC
14. Silicone Sealing Foam Cord: The Valuable Option For You
Author: Dongguan Senma New Materials Technology Co., Ltd
15. How Investment Banking Companies And Credit Solutions Elevate Wealth Management
Author: Drishti Desai