ALL >> Business >> View Article
How To Choose The Right Crusher For The Right Job
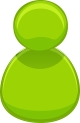
Rock crushers are heavy-duty machines that reduce the size of rock according to specific requirements. They are most widely used in mining applications but have also been adapted to the construction and other industries. There are several types of rock crushers. These include jaw crushers, cone crushers, gyratory crushers, hammer crushers and mobile crushers. Each has distinct features and advantages which makes it suitable for a specific purpose. There are a number of criteria that will decide what rock crusher is required for the job at hand. Before evaluating your options, you first need to establish the details of your specific project.
What Application is the Rock Crusher For?
This is a simple question that will quickly eliminate crushers that are not suitable for your purpose. If you need a rock crusher for construction or road works, there are a number of custom designed purpose built crushers specific to those industries. Alternatively, if you require a rock crusher for mining applications then you have a broader scope of choice. It is then that you will have to look more closely at the requirements of ...
... your job to differentiate which crusher will best suit your purposes.
What Type of Rock Will be Crushed?
Different types of rock vary in density, hardness, water content and abrasiveness. All of these are factors that determine what type of crusher would be optimal for crushing a specific type of rock. Certain crushers are suited to rocks that are less abrasive or have higher water content. The different types of crushers use different motions to crush the rock. Some use sheer pressure and force between two plates and others use circular motions or hammer actions in order to crush the rock. Comparing the type of rock and the specific applications of each type of crusher will help you find the right crusher for your job.
Where Will the Rock Crusher be Located in the Workflow Process?
This may seem like an obvious question but it is quite important when it comes to deciding on the right crusher for a specific job. You get primary, secondary and tertiary crushers. As the names suggest, the crushers are either the first, second, or third machines to crush the materials. In some applications, you could even have as many as five rock crushers in the workflow process. The primary crushers are the biggest and have the largest workload. This is because they are the first to receive the unrefined rock from the mine. The rock is usually in very large uneven chunks and difficult to handle and process. It is the job of the primary crusher to reduce the size of the rock so that it is more manageable and can be more easily processed and transported. A secondary or tertiary crusher each has the job of further crushing and refining the materials.
Another consideration regarding the type of crusher to be used is to decide if the crusher will be part of a stationary processing plant or if it will be a stand-alone mobile crushing unit. If the crusher needs to be on-site and will be used for exploratory work then a mobile crusher plant may be considered. However, the downside of mobile crushers is that they do not always have the same capacity as larger stationary crushers.
What is the Estimated Capacity Required of the Rock Crusher?
In your projections and planning, you should have a good idea of the output capacity of the mine. You should also have an indication if this output is likely to increase, stay the same or decrease over time. These projections will help you to select a rock crusher that has a capacity that is consistent with the mine output. This is a vital part of the planning process. If you select a crusher that does not have a large enough crushing capacity, it will bottleneck the workflow process. On the other hand, if your crusher capacity far exceeds the mine output, you could be wasting valuable resources such as electricity that could be better utilized elsewhere.
What Final Products are Required as a Result of the Crushing Process?
Most crushers are required to deliver rock that is a certain size and shape so that it can be transported for manufacturing or for further processing. Knowing the input size and output size requirements for the crushing process will help you select the right type of crusher for the job. Each machine has set specifications and the manufacturers will be able to supply you with this information.
About Author:
For heavy equipment such as jaw crushers, visit Crusher-Mills.com online where they supply efficient equipment and the latest technology.
Add Comment
Business Articles
1. Lucintel Forecasts The Glass Fiber In The Global Marine Market To Grow With A Cagr Of 3.7% From 2024 To 2030Author: Lucintel LLC
2. Lucintel Forecasts The Glass Fiber In The Global E&e Market To Grow With A Cagr Of 3.9% From 2024 To 2030
Author: Lucintel LLC
3. Lucintel Forecasts The Global Frp Pole In Telecommunication Market To Grow With A Cagr Of 6.5% From 2024 To 2030
Author: Lucintel LLC
4. Lucintel Forecasts The Global Frp Pole In Power Transmission & Distribution Market To Grow With A Cagr Of 6% From 2024 To 2030
Author: Lucintel LLC
5. Lucintel Forecasts The Global Frp Pipe In Oil And Gas Market To Grow With A Cagr Of 5.1% From 2024 To 2030
Author: Lucintel LLC
6. Lucintel Forecasts The Global Frp Pipe In Chemical Market To Grow With A Cagr Of 3.6% From 2024 To 2030
Author: Lucintel LLC
7. Adopt A Modern Telecom Commission Management System To Fix Revenue Leakages
Author: Kevin
8. Quality Steel Pipes And Tubes With Commitment And Trusted Service
Author: CONTENT EDITOR FOR SAMPHIRE IT SOLUTIONS PVT LTD
9. Lucintel Forecasts The Global Foam Core For The Construction Market To Grow With A Cagr Of 3.7% From 2024 To 2030
Author: Lucintel LLC
10. How Important Is Mutual Fund?
Author: Sagar Shah
11. What Do You Need To Know About Customize Your Own Clothes
Author: Guangzhou Beianji Clothing
12. Detailed Tips To Choose Quality Cabinets And Joinery Melbourne
Author: William Harvey
13. Lucintel Forecasts The Global Foam Core For The Transportation Market To Grow With A Cagr Of 5.4% From 2024 To 2030
Author: Lucintel LLC
14. Silicone Sealing Foam Cord: The Valuable Option For You
Author: Dongguan Senma New Materials Technology Co., Ltd
15. How Investment Banking Companies And Credit Solutions Elevate Wealth Management
Author: Drishti Desai