ALL >> Business >> View Article
Pipe Fittings Manufacturing Process
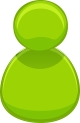
There are numerous Pipe Fittings Manufacturing Process that castoff to manufactured Elbow, Tee, Reducers and other pipe fittings.
Fittings are mass-produced from Seamless Pipe and Welded Pipe with filler material (ERW & EFW pipes cannot be used to manufactured fittings). Ss Pipe fittings are manufactured at large scale in Kolkata click here to know more.
To mass-produced wrought fitting numerous methods are used, these are the unlike type of Hot and cold forming process.
These methods are
• Hot forming or Extrusion Method
• Hydraulic Bulge method – Cold forming
• UO or Single weld seam Method
• Monaka or Double weld seam Method
• Deep Drawing Method for caps
• Flare Method for Stub ends
ELBOWS Manufacturing Process:
1. Mandrel method (Hot Forming)
One of the most well-known Pipe Fittings Manufacturing Process for assembling Elbows from the pipe is mandrel strategy which is somewhat hot framing techniques.
In this technique, the pipe is cut in pieces and push with the assistance of pressure driven smash. Enlistment warming loop warms ...
... the pipe and, it is pushed over a pass on called "mandrel" which enables the pipe to extend and twist all the while. This technique can be utilized to make a wide scope of the distance across of elbows
2. Extrusion Method
In cool Extrusion strategy, a pipe with a similar width as completed item is pushed through a bite the dust and framed into its ideal shape. Typically applied to treated steel little to medium sizes elbows.
3. UO Method
UO technique is utilized to produce medium size of the elbow, tee, and reducers. The plate is removed into an uncommonly planned shape, it is framed first into a U-shape utilizing a pass on and afterward into an O-shape or cylindrical structure utilizing another kick the bucket, that is the reason this strategy is known as UO technique. When the fittings framed in tumbler formed it is welded from inside and outside of the end crease. A cut plate is first from fit as a fiddle and afterward fit as a fiddle.
4. Hot Forming Method
In a Hot Forming Die Bending technique, a Pipe is warmed to framing temperature and shaped in the bite the dust with the particular shape, this procedure might be rehashed as expected to get the necessary shape, estimate and divider thickness. Typically applied to thick-divider things that can't be bowed on a mandrel kick the bucket.
TEE Manufacturing Process:
1. Hydraulic Bulge Method
Water powered Bulge technique is utilized to make Tee. Cut bit of Pipe is put in water driven bite the dust and fluid is fill inside the pipe, Hydraulic pressure pushes out the branch, in the fixed opening in the bite the dust. This technique gives the great surface completion. Be that as it may, higher thickness Tee can't be made by this technique.
2. Hot Extrusion Method
Tee with huge widths, substantial divider thickness and/or unique material with testing usefulness that can't be fabricated utilizing the pressure driven lump strategy are produced utilizing hot Extrusion Method. In hot Extrusion Method, Normally Bigger distance across pipe is utilized than the completed item size, the branch outlet is expelled from the pipe with assistance of expulsion device. Different measurements of body and branch can likewise be balanced by squeezing the pass on whenever required.
Reducer Manufacturing Process:
External Die Method
Most basic technique for assembling Reducers is Outer Die strategy. The pipe is cut and squeezed in the external pass on; packing the one finish of the pipe into a littler size. This strategy is helpful for assembling of little to medium size of reducers.
Cap Manufacturing Process:
Profound Drawing Method
Tops are made by Deep Drawing technique. In this strategy, Plate is removed around and shaped by profound drawing kick the bucket.
Stub end Manufacturing Process:
Flaring Method
Stub Ends or Lap Joints Flange are made by flaring technique. Pipe end is a flare or saved out to frame rib face. Stub closes are likewise produced by manufacturing in which fashion square are machined to definite measurement.
Fitting Heat Treatment
Hot completed pipe fittings don't require heat treatment, be that as it may, for Cold completed pipe fittings Heat treatment is required according to relevant ASTM standard.
Common Heat Treatment for Fittings are
1. Normalizing
2. Quenching
3. Tempering
4. Solution Annealing
5. Stress relieving
6. And Combination of above
Add Comment
Business Articles
1. Repair And Maintenance Guide For Garden FencingAuthor: Vikram kumar
2. Lucintel Forecasts The Global Palatant Market To Grow With A Cagr Of 5% From 2024 To 2030
Author: Lucintel LLC
3. Choosing The Right Gas Regulator In Florida: A Complete Guide
Author: Technico
4. Why Deer Park Learners Trust Local Driving Instructors
Author: Aintree Driving School
5. How To Properly Install And Uninstall Your Air Conditioner System With A Low Budget
Author: Neha Jain
6. What Is The Role Of Pdca In Iso 50001?
Author: William Charles
7. Step-by-step Instructions On How To Generate Inventory Reports Quickbooks?
Author: Jack Edwards
8. How To Track Employee Work Hours Efficiently With Trackhr
Author: TrackHr App
9. From Grounded To Global: 4 Ceos Rewiring India’s Aviation Sky
Author: Skyone
10. The Role Of Automation In Modern Cloud Migration Methodology
Author: Netscribes
11. Master Photo Retouching | Steps To Become A Photo Editing Expert
Author: ukclippingpath
12. Great Dependability And Performance Are The Reasons For Extensive Use Of Hydro Pneumatic Press
Author: David Camp
13. Best Lasik Eye Surgery For A Spectacle-free Life
Author: Anil Eye Hospital
14. Industrial Oven Manufacturers In Coimbatore
Author: Heatcon Sensors
15. Plumbing In North Salt Lake: Your Guide To Reliable Services
Author: Brown Jones