ALL >> Business >> View Article
Sheet Metal Fabricators
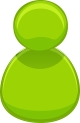
Sheet metal fabricators are machines that are used to punch holes in, or form sheets of metal. The typical products made with a sheet metal fabricating machine are the fronts, backs and sides of a machine or electrical appliance enclosure. These parts typically have louvered air vents, holes for switches, lights and gauges, and holes for fasteners to assemble the sheet metal parts onto a finished product. These parts are so common in our lives, that we are virtually surrounded by these parts - in your kitchen, the bottoms of all your appliances, even your toaster are typical examples of fabricated sheet metal parts.
The parts you find in your kitchen are, in actual fact, made with high-speed presses and CNC turret punches - not on what we are referring to as "sheet metal fabricators". Sheet metal fabricators are typically used to do prototype work or low volume production. Their value is their ability to make a part without requiring complex expensive tooling or the need to write a program - a fabricator requires no set up time. You simply attach a piece of sheet metal to the machine using clamps, insert the appropriate ...
... punch and die into the holders and turn some handles to position the sheet of metal properly and start making holes.
These sheet metal fabricators were made by Amada, Strippit, Weidermann and others and are found in most fabricating shops as handy tools to quickly make a part. The machines consist of a "C" frame, a power source, a table and work holding system and a punch holder and die holder. The power source can be either a hydraulic system with a cylinder that drives the punch down into the die, or a motor driving a flywheel and crank to move the punch down into the die. The "C" frame must be heavily constructed to maintain correct alignment when the punch is forced downward cutting thru the metal and into the die. Exact tolerances must be maintained to cut the metal cleanly and for long tool life.
The two main specifications on a sheet metal fabricator are the throat depth and the tonnage. The throat depth determines the size of piece of sheet metal the machine can handle and the tonnage determines the size hole that can be punched in a certain thickness of metal. A typical example of a sheet metal fabricator is a Strippit Super 30/30. The 30/30 in the model designates the 30" throat depth and the 30 ton pressing force of this model fabricator. It is one of the most common fabricating machines in existence.
The punches and dies used in these machines can be used to form metal, not just punch holes. For example, a dimple can be made, or a louver cut just as easily as punching a hole. The mechanism for positioning the sheet metal is generally a couple of hand wheels with some form of gauging system to determine exact positioning. Sometimes a digital readout system is used to provide the operator with exact X and Y coordinates. If a number of identical parts need to be made, some fabricators have a template and duplicator system that allows the operator to quickly go from hole to hole location without having to look at a gauge or readout.
Most parts require a number of different punches and dies. Each time a different hole or shape is required the operator must change both the punch and die on these machines. It requires a number of seconds to pull out the old punch and die and slip in the new ones and lock them in. This is done much more quickly if the machine is equipped with a turret. In a turret machine the punches and dies are held in top and bottom, rotating turrets that can be moved together to change to a new punch and die. In this system the punches and dies are pre-loaded and pre-aligned and always ready to go simply by rotating to the next station.
While fabricators fill a valuable need in many shops they are not the way to make large numbers of parts. CNC turret punches can make many parts in the time an operator can make one part on a manual fabricating machine. But, when a product is in the design phase or the production volume is really low, it is a cost effective, highly versatile and valuable machine to have in a shop.
Add Comment
Business Articles
1. Lucintel Forecasts The Glass Fiber In The Global Marine Market To Grow With A Cagr Of 3.7% From 2024 To 2030Author: Lucintel LLC
2. Lucintel Forecasts The Glass Fiber In The Global E&e Market To Grow With A Cagr Of 3.9% From 2024 To 2030
Author: Lucintel LLC
3. Lucintel Forecasts The Global Frp Pole In Telecommunication Market To Grow With A Cagr Of 6.5% From 2024 To 2030
Author: Lucintel LLC
4. Lucintel Forecasts The Global Frp Pole In Power Transmission & Distribution Market To Grow With A Cagr Of 6% From 2024 To 2030
Author: Lucintel LLC
5. Lucintel Forecasts The Global Frp Pipe In Oil And Gas Market To Grow With A Cagr Of 5.1% From 2024 To 2030
Author: Lucintel LLC
6. Lucintel Forecasts The Global Frp Pipe In Chemical Market To Grow With A Cagr Of 3.6% From 2024 To 2030
Author: Lucintel LLC
7. Adopt A Modern Telecom Commission Management System To Fix Revenue Leakages
Author: Kevin
8. Quality Steel Pipes And Tubes With Commitment And Trusted Service
Author: CONTENT EDITOR FOR SAMPHIRE IT SOLUTIONS PVT LTD
9. Lucintel Forecasts The Global Foam Core For The Construction Market To Grow With A Cagr Of 3.7% From 2024 To 2030
Author: Lucintel LLC
10. How Important Is Mutual Fund?
Author: Sagar Shah
11. What Do You Need To Know About Customize Your Own Clothes
Author: Guangzhou Beianji Clothing
12. Detailed Tips To Choose Quality Cabinets And Joinery Melbourne
Author: William Harvey
13. Lucintel Forecasts The Global Foam Core For The Transportation Market To Grow With A Cagr Of 5.4% From 2024 To 2030
Author: Lucintel LLC
14. Silicone Sealing Foam Cord: The Valuable Option For You
Author: Dongguan Senma New Materials Technology Co., Ltd
15. How Investment Banking Companies And Credit Solutions Elevate Wealth Management
Author: Drishti Desai