ALL >> Business >> View Article
Cumberland Plastic Granulators
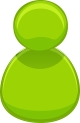
Plastic granulators are machines that are used to break down plastic products to enable them to be more easily recycled. Recent research has reported that many different products can be recycled in this way, and since discarded plastic products account for as much as 40 percent of all solid waste, recycling this plastic could substantially reduce what ends up in landfills. Because plastic cannot biodegrade, the solution is to break the plastic down mechanically into small pellets which can be reused to make new products. Since plastic does not degrade on it is own, recycling is the one and only option available for reducing the amount of plastic finding it is way into the landfills. One of the solutions to this problem is Cumberland plastic granulators, which are industrial quality machines capable of converting large quantities of plastic waste into reusable or saleable plastic pellets.
Cumberland is a long established brand name plastic granulator manufacturing company. The plastic granulators made by Cumberland have filled an important role in auxiliary equipment for plastic manufacturing industry for many years. ...
... Cumberland plastic granulators are used side by side with plastic injection molding machines and blow molders.
Cumberland makes many types of plastic granulators. There are several different subsets that make up the complete line of plastic granulators and grinders, and choosing the right one can have a profound impact on the ability to create desired results. These three categories of plastic granulating machines have different purposes and fit different needs - choosing the right one is essential to best achieve your desired purpose.
"Beside the Press" Cumberland Plastic Granulators
When plastic injection molded or blow molded products are manufactured, parts are made by melting plastic pellets into a viscous liquid state, then injecting this liquid plastic into a mold. The molds are constructed with channels to allow the plastic to flow into all corners of the mold. When the plastic hardens, these channels are filled with hard plastic that is called sprue. The sprue is broken or picked off the parts by humans or robots. This pure plastic is dropped into a granulator to be converted back into pellets that go right back into the injection molding machine to be re-melted and made into new parts.
These "beside the press" style plastic granulators are designed to fill needs for the injection molding market when it comes to scrap reclamation and similar processes. From small runners and sprues to large and finished parts, these plastic granulating products can get the job done. The recycling happens right at the machine lowering the injection molders raw material cost and eliminating the need to dispose of waste material. The reprocessing and reclamation of these materials can save a significant amount of time, money, capital and even landfill space.
"Under the Press" Cumberland Plastic Granulators
The under the press style plastic granulating units are designed to be auger fed for the purpose of thermoforming applications, injection molding and web processing, primarily within the thermoform industry. Through the reclamation of this material, which can be quite valuable for many applications, environmental resources as well as financial resources can be effectively conserved.
"Central" Cumberland Plastic Granulators
The purpose of these central style granulators is to serve as large units, and they have been designed primarily for the reclamation of larger volumes of material or larger size materials. They are typically installed in strategic sites that are convenient for a particular manufacturing application, and as such, these units are able to process much larger quantities of plastic and resin for the purpose of selling or reprocessing. There are a wide variety of different units that can be purchased and utilized in order to meet the unique requirements for any manufacturing facility. These large size machines can also be used to recycle refuse plastic, like PET bottles (soda bottles) or the like.
Add Comment
Business Articles
1. Transform Your Outdoor Space With Landscape Man Professional Services UkAuthor: Vikram kumar
2. The Ultimate Guide To Best Investment Real Estate In Konkan
Author: codename oxygen
3. Lucintel Forecasts The Global Induction Flushing System Market To Grow With A Cagr Of 3.6% From 2024 To 2030
Author: Lucintel LLC
4. Why Your Business Needs A Dynamics 365 Customer Portal
Author: crmjetty
5. Lucintel Forecasts The Global Indium Trioxide Market To Grow With A Cagr Of 3.8% From 2024 To 2030
Author: Lucintel LLC
6. Mg Hector Gloster Price In Chennai: A Comprehensive Overview
Author: balaji
7. Chennai Mg Hector On Road Price: An Extensive Overview
Author: balaji
8. Maximizing Financial Success With Investment Banking, Wealth Management, And Credit Solutions
Author: Drishti Desai
9. Airline Inventory System
Author: Yugababu
10. Lucintel Forecasts The Global Exterior Insulation And Finish System Siding Market To Grow With A Cagr Of 9.9% From 2024 To 2030
Author: Lucintel LLC
11. Looking For Erp With Crm? Ultimate Solution For Sales And Customer Support
Author: Emmanuel Mathew
12. Lucintel Forecasts The Global Ergonomic Office Chair Market To Grow With A Cagr Of 4.9% From 2024 To 2030
Author: Lucintel LLC
13. Lucintel Forecasts The Global Embedded Host Bridge Market To Grow With A Cagr Of 5.3% From 2024 To 2030
Author: Lucintel LLC
14. Lucintel Forecasts The Global Digital Paraffin Warmer Market To Grow With A Cagr Of 3.4% From 2024 To 2030
Author: Lucintel LLC
15. Common Lead Gen Pitfalls And How To Overcome Them
Author: tim seifert